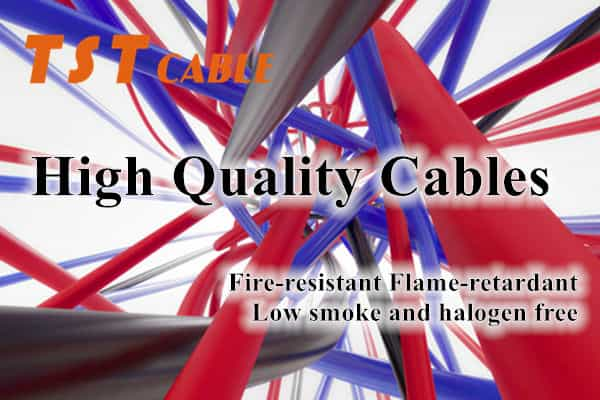
First TSTCABLES First of all, the concept of crosslinking, crosslinking – through physical or chemical methods to transform linear polyethylene molecules into a three-dimensional mesh structure, so as to improve its mechanical and physical properties and heat resistance. There are two main categories of crosslinked insulation: physical and chemical crosslinking.
Physical cross-linking is also known as irradiation cross-linking cables, generally applicable to low voltage cables with thin insulation thickness.
Chemical cross-linking is mainly divided into peroxide cross-linking and silane graft cross-linking of two kinds, of which: medium-voltage, (super) high-voltage cable insulation using peroxide cross-linking, conventional low-voltage crosslinked cables generally use silane graft cross-linking.
Irradiation crosslinking process is mainly applied to special low-voltage crosslinked cable manufacturing, such as nuclear-grade cables, higher operating temperature cable (long-term operating temperature of up to 150 ℃), crosslinked low-smoke halogen-free flame-retardant wires and cables, etc., by the material technology and the impact of the penetration of y-ray radiation, etc., the irradiation crosslinking process is not suitable for medium-voltage, (ultra-) high-voltage cable manufacturing.
UV cross-linking technology is another new cross-linking technology developed after chemical cross-linking and irradiation cross-linking, which is a technological innovation developed by our country with independent intellectual property rights. The principle of UV cross-linking is: polyolefin as the main raw material to add the appropriate amount of photoinitiator, the use of ultraviolet light irradiation, through the absorption of specific wavelengths of ultraviolet light by the photoinitiator initiated by the generation of polyolefin free radicals, which occurs in a series of rapid polymerization reaction, the generation of a three-dimensional mesh structure of the cross-linking of the polyolefin, crosslinking the production of cable has opened up a new way to be put into the low-voltage crosslinking cable manufacturing. The following mainly introduces the chemical crosslinking.
First, peroxide crosslinking
Peroxide crosslinking method is by adding crosslinking agent and initiating crosslinking method. It is mainly suitable for the rated voltage of 10kV and above, a variety of cross-sectional area of crosslinked polyethylene insulated power cable manufacturing.
(A) steam crosslinking (SCP)
Steam crosslinking manufacturing technology is a rubber continuous vulcanization technology as the background of the evolution of one of the most “ancient” crosslinking method. This method is to a certain pressure, a certain temperature of water vapor as a heating and pressurization medium, so that the polyethylene to achieve crosslinking. Steam cross-linking was successfully researched by GE in 1957, and Sumitomo Electric introduced this technology in 1959 and put it into production in 1960.
In the early stage, the use of saturated steam as a medium, the pressure and temperature of the crosslinking tube has a direct correlation, such as to increase the steam temperature, you must also increase the steam pressure, the temperature rises 10 ℃, the pressure will be increased by about 5kg, to reach a sufficiently high temperature will be difficult to achieve, and energy consumption is also high; later on, the development of the wall of the crosslinking tube can be heated to increase the temperature of the steam (known as superheated steam, without increasing the pressure to raise the temperature), and later developed into a crosslinking tube wall heating to improve the steam temperature (called superheated steam, not by increasing Later, it was developed that the steam temperature could be increased by heating the wall of the cross-linking tube (called superheated steam, which does not need to be increased by increasing the pressure to raise the temperature), and it is mainly used in rubber vulcanizing units. As the water vapor in the crosslinking tube directly in contact with the molten state of polyethylene, water will penetrate into the insulation inside the diffusion of the cooling process in the cable, the insulation inside the water vapor saturated state and the formation of microporous, put into operation and then triggered by the dendritic discharge, which is the Achilles’ heel of this method. Thus, since the 1960s, there are some new dry crosslinking process.
(B) infrared crosslinking method (RCP) and dry crosslinking
Infrared cross-linking method is also called thermal radiation cross-linking method (RCP), is a dry cross-linking process invented by Sumitomo Electric Company in Japan in 1967.
The method of cross-linking polymers with infrared rays was patented as early as 1937 by General Electric (GE) of France for vulcanization of rubber products, and in 1961 W.R. Grace of the U.S.A. patented the manufacturing of polyethylene film by infrared irradiation. Sumitomo Electric Co., Ltd. was inspired by the above two patents, and applied for a patent in June 1966, in which a layer of cross-linked polyethylene containing organic peroxide cross-linking agent was extruded on the conductor, and the polyethylene was radiantly heated in an inert gas at a pressure of more than 2kg/cm² to make the polyethylene undergo a cross-linking reaction. In April 1967, Sumitomo Electric filed another patent application, proposing that the entire cross-linking unit consisted of a radiant heating section, a cooling section, and a water-cooled section. In the process of long-term cross-linking reaction, the inner wall of the cross-linking tube forms a layer of black dirt deposited by peroxide, which is a layer of naturally occurring infrared emission of the black body, through technological advances, the RCP process is gradually replaced by the general electric heating dry cross-linking process. At present, the hanging cross-linking process technology and VCV vertical tower cross-linking process technology are widely used.
The heating and pre-cooling sections are protected by nitrogen. In the heating crosslinking tube, the main role of nitrogen is as a heat transfer coal, and to protect polyethylene at higher temperatures under the surface does not occur oxidative degradation, while the insulation to exert enough pressure, so that the insulation in the process of crosslinking does not occur or as little as possible to occur in the air gap, the flow of nitrogen can also take away a large amount of water volatilized by the cooling water and the water and volatiles decomposed by peroxides in the crosslinking reaction. In the pre-cooling but part of the main role of nitrogen is the cable insulation core surface pre-cooling but, so that the core surface at a lower temperature into the water cooling part of the core, thus preventing the core suddenly cold insulation stress affect product quality. Due to the use of electric heating, it can be used to increase the temperature of the method to improve production speed. Cross-linked polyethylene insulation, dry cross-linking method of water content of only 0.018%, while the steam cross-linking method of water content of 0.29%, the test shows that the dry cross-linking method of AC breakdown strength and impact breakdown strength of insulation is higher than the steam cross-linking method.
Dry crosslinking production equipment, mainly hanging crosslinking unit, vertical tower crosslinking unit two, VCV vertical tower crosslinking unit using a vertical extrusion method, more conducive to the control of the eccentricity of the insulation of large thickness.
(C) long bearing mold (MDCV) crosslinking
Long bearing mold crosslinking is the United States Anaconda wire and cable company (Anaconda) invented in 1959, the same year they applied for a patent, known as the MCP process. Later, due to the fierce competition in the wire and cable industry, the company withdrew from the cross-linked polyethylene wire and cable manufacturing competition, so that this new process could not be put into practice. 1971 Dai Nippon Electric Wire & Cable Company and Mitsubishi Petrochemical Company cooperated, purchased the patent of Anaconda Company, so that this method can be realized, known as the MDCVI process. 1973 Dai Nippon Electric Wire & Cable Company applied for a patent of the MDCV process. The original meaning of MDCV is “Mitsubishi Dainippon Continuous Crosslinking Method”, while the technical meaning is “Long Bearing Die Crosslinking Process Method”.
The MDCV method uses a horizontal cross-linking tube, which is installed in the extruder head. The extrusion die is 20 meters long. While extruding the insulated core, the tube is filled with lubricant, which cross-links the polyethylene in this die.
The MDCV method is characterized by low investment in equipment, small footprint, stable manufacturing of large cross-section cables, production speeds comparable to CCV cross-linking units, stable and reliable quality of manufactured products, and the AC breakdown field strength of cables manufactured using this process is 60% to 70% higher than that of steam cross-linked cables. However, when the need to produce different specifications of the cable, to replace the entire long bearing mold, the flexibility is not strong, and therefore has not been promoted for use.
(D) pressurized molten salt crosslinking (PLCV) process
This method was originally invented by the Italian company Carrero (Careillo) In August 1976, the company and the British General Engineering Corporation to cooperate in research, so that it is used in the manufacture of cross-linked polyethylene-insulated power cables. 1977 British General Engineering Corporation Jelalade Smuts published the results, and to the United Kingdom BICC sold the first equipment. PLCV system used in the The salt used in the PLCV system is the same as that used in the rubber vulcanization LCM method. Examples of molten salt formulations: a mixture of inorganic salts consisting of 53% potassium nitrate, 40% sodium nitrite, and 7% sodium nitrate, this mixture melts at 145°C to 150°C and remains stable until 540°C. The molten salt cross-linking tube is sealed, and during the cable manufacturing process, a pressure of (3~4) atmospheres is generally applied, the molten salt temperature is 200℃~250℃, and the cooling section is also pressurized. Due to the specific gravity of the molten salt mixture, to solve the problem of large weight cable towing pipe, a combination of factors, the process is used by the rubber vulcanization production line, especially suitable for large weight rubber cable manufacturing.
(E) silicone oil crosslinking (FZCV) process
In 1979, Japan’s Fujikura Electric Wire Co. Kuma Sadayoshi and others invented the silicone oil crosslinking process (FZCV), this method uses pressurized silicone oil as a heating and cooling coal. Under the pressure of the silicone oil, the cable can be suspended in the silicone oil without rubbing the tube and eccentricity. The silicone oil can be recycled. Fujikura Electric Wire & Cable began producing 275kV cross-linked polyethylene cables with two FZCV units in 1979, effectively solving the high-voltage technical problem of large cross-section cross-linked polyethylene cables. Due to the high input cost and other reasons, it has not been widely used.
In the above chemical cross-linking process, a combination of factors, hanging cross-linking unit, vertical tower cross-linking unit in the plastic medium-voltage, (super) high-voltage power cable manufacturing has been the most widely used. In the above cross-linking methods, are external heating cross-linking method, in 1975 West Germany’s Mench (G. Menger) proposed to shorten the cross-linking time through the conductor heating method, he proved experimentally, every 1 mm thick polyethylene insulation, cross-linking time of about 1 minute, for this reason, only to slow down the speed of the line or to increase the length of the cross-linking tube to be able to do. If the current of 1000 amperes to make the conductor temperature rise to 200 ℃, the crosslinking time is shortened by 20%. At present, many crosslinking production units have adopted the conductor preheating technology, the production efficiency has been effectively improved, and at the same time is conducive to insulation quality.
Second, silane crosslinking
Silane cross-linking, also known as warm water cross-linking, 1960 British Dow Corning (Dow-Corning) proposed the development of, also known as the Sioplas method, that is, silane grafting cross-linking process, which is grafted and extruded into two processes, known as two-step silane cross-linking. In the first step, the silane cross-linking agent and the base material are grafted and extruded by the insulating material plant on the extruder and pelletized, which is called A material (grafting material), and the masterbatch, which is called B material, is also provided with catalysts and coloring agents. The second step is to mix the A material and B material in a certain ratio (eg: A material: B material is 95:5), in the ordinary extruder extrusion package in the cable conductor, and then into the 80 ℃ ~ 95 ℃ warm water crosslinking pool or in the steam room to complete the crosslinking. This process has low investment cost and can be processed by general extruder. The material price is moderate, and it is widely used.
But there are also the following disadvantages:
(1) grafted polyethylene is easy to occur with moisture in the air prior to crosslinking, shortening the storage time, the general storage period of six months.
(2) The mixture of grafted polyethylene and catalyst masterbatch, the storage period is generally not more than 3h, so it needs to be mixed while extruding.
(3) Since the two-step method is easy to lead to the mixing of impurities through multiple mixing, it is mainly used for the manufacture of cable insulation below 10kV.
In order to overcome the limitations of Sioplas, in 1977, the British BICC and the Swiss Maillefer Company cooperated and invented a one-step silane cross-linking process, also called Monosil process, based on the two-step method invented by Dow Corning. It will be polyethylene base material, antioxidant and liquid silane at the same time measurement, mixing, that is, the grafting reaction and adding catalyst process is merged, and the use of length to diameter ratio of 30:1 extruder will be extruded insulation packages in the cable conductor, will be grafted and extruded by a step of the insulating layer, so it is called one-step method. It has the lowest material cost, the chance of contamination by impurities is reduced, and the material storage period can be greatly increased. However, the investment in equipment for this process is larger than that of the two-step method, and a liquid silane feeding system needs to be equipped.
With the development of materials technology, for the application of one-step silane cross-linking technology, can also be pre-mixed uniformly by high-speed mixer polyethylene base material, antioxidant and liquid silane, and parked in certain conditions, so that the added antioxidant and liquid silane fully infiltrated, and then use the ordinary extruder to complete a one-time grafting and extrusion, extrusion process should be strictly controlled extrusion process of the material temperature, the material temperature requirements, high. Ensure that the extrusion process to complete the silane grafting, after extrusion of the insulation core into the warm water crosslinking pool or steam room to complete the crosslinking; if the extrusion process is too low material temperature is not completed when the grafting, extrusion of insulation will not be able to crosslinking.
Time came to the eighties, in absorbing the advantages of two-step and one-step method based on the development of copolymerization. Copolymerization method is also a silane copolymerization monomer a vinyl-trimethoxysilane, just using a different process. The process is not the organic silane grafted to the polymer chain, but in the polymerization process can be introduced into the hydrolyzable silane, thus producing an easy-to-process silane copolymers, the method is in a high-pressure reactor, so that the copolymerization of ethylene and silane copolymerization monomers, the key to the process is that the copolymer monomer selected must contain an unsaturated group that can be reacted with the polymer chain with ethylene. Ethylene silane copolymers are structurally identical to Sioplas grafted compounds.
Since the silane copolymer is manufactured in a reactor, it ensures a high degree of cleanliness and avoids the problem of contamination with peroxide residues during grafting. An even more important advantage of silane copolymers is that the amount of silane required during the polymerization reaction is lower than that required for silane grafted compounds because of the regular distribution of the crosslinking lattice achieved by a single input of the silane copolymer monomer. Due to the advanced and unique process of the copolymerization method, the silane cross-linked polyethylene materials produced have the following advantages:
(1) Good storage stability, storage time can generally exceed one year, better than grafted materials.
(2) Copolymerization method of cross-linked polyethylene processing, mixing of free substances and impurities is very small, thus improving the cable insulation properties.
(3) can be extruded in the ordinary extrusion machine, manufacturing process stability.
Later developed a solid-phase one-step process and curing silane process. Solid-phase one-step process is the silane through silica and other carriers to penetrate into the PE base material. Cured silane process is to improve the silane feeding method, liquid silane can be adsorbed in porous polypropylene plastic or PE plastic to form solid silane, both processes are derived from the one-step process.
With the advancement of materials technology, on the basis of two-step silane crosslinking technology, the introduction of silane self-crosslinking polyethylene insulating material (also known as silane room temperature crosslinking polyethylene insulating material), the principle of which is to improve the catalyst masterbatch (B material), the addition of a composite water-producing agent and a highly efficient catalyst, the use of grafting material (A material) and catalytic material (B material) mixed with the extruded material, in general in the room after the placing of (2 to 7) days later (such as high ambient temperature, placed for a short period of time) can be completed crosslinking, do not need to be in the warm water crosslinking pool or steam room for crosslinking, the material cost is high, but due to the convenience of the production, but also get a certain degree of application.
Comprehensive features of different silane crosslinking process, material costs and other factors, the current one-step silane crosslinking, two-step silane crosslinking has been the most widely used, in which the two-step silane crosslinking process, due to the A material has completed the grafting reaction, the core insulation extrusion temperature requirements are low, and is conducive to change the gauge production. One-step silane cross-linking process, low material cost, grafting and extrusion is completed at one time, the extrusion temperature requirements are high, the material temperature does not meet the requirements can not complete the grafting, the extruder is set at a high temperature, such as frequent shutdowns to change the gauge prone to clinker, suitable for the production of large-length cable cores.
TST CABLES adopts advanced cross-linking technology, the cable structure is more compact, electrical performance is more excellent. High temperature resistance, corrosion resistance, long service life, effectively reduce the safety risks. Widely used in nuclear power, wind power, ships, construction, industry, transportation and other fields, is your trusted expert in power transmission solutions, if your industry needs cross-linked cables or have other questions, you can send an email to communicate with us.
Also available in:
English