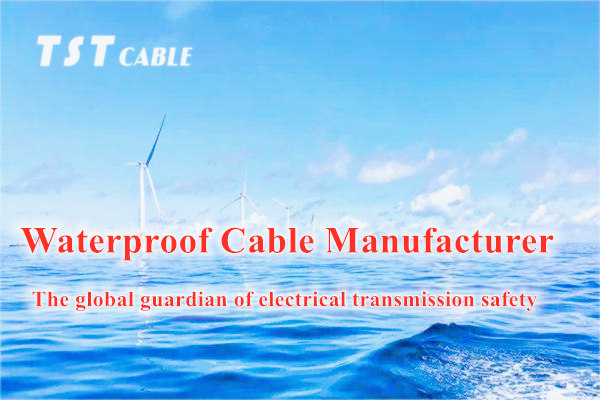
Tick Tock … Water leakage of cables will cause its insulation to degrade, accelerate aging, and lead to power failure. Cable leakage will affect the quality of signal transmission, affecting the normal work of communication. Water leakage of cables will make the cable interface corrode, which will lead to short circuit, fire and other accidents.How to solve the water leakage of cables? How to protect your cable from the pain of immersion?TST CABLES give you a waterproof cable purchase strategy!
First, the characteristics of waterproof cable
Waterproof cable is made of special materials, with waterproof, moisture-proof, oil-proof, corrosion-proof and other characteristics, can be in the wet, high humidity, susceptible to oil contamination and other environments stable transmission of electrical energy. Therefore, waterproof cables are widely used in transportation, petrochemical enterprises and other industrial and civil facilities in coastal areas. Waterproof cables are also more suitable for the installation and use of outdoor electrical appliances, solar energy, vehicle-mounted and other equipment.
Waterproof cable shell using special materials, with excellent waterproof performance, and the use of special joint structure design, so that the waterproof sealing of the connection joints can reach a higher level, even in heavy rain or immersed in water can still maintain a stable power transmission.
Second, waterproof cable structure and technology
Waterproof cable structure design is reasonable, the cable core and outer sheath surface seamless fit, and through the filling material to achieve the effect of waterproof sealing. Its workmanship is fine, including the choice of materials, cable structure of reasonable design, waterproof coating of uniform coating and strict process control, which ensures the high quality of waterproof cable.
Third, waterproof cable standard:
IEC 60794-1-2: This is the International Electrotechnical Commission (IEC) issued a standard describing the structure and performance requirements of fiber optic cables, which also includes waterproof performance requirements.
IEC 60502-1: This standard applies to low-voltage power cable systems with rated voltages of 1 kV and below, and includes requirements and test methods for watertight cables.
IEC 60092-375: This standard is for cable systems in the field of marine and offshore engineering and specifies the requirements for watertight performance of cables.
In addition, countries have their own national standards, such as China’s GB/T 12706.1-2008, which specifies the general requirements and test methods for watertight cables; and Europe’s EN 60529, which is also an important implementation standard for watertight cables. At the same time, there are industry standards for specific applications, such as China’s YD/T 1401-2010 for power communication cable, and DL/T 1148-2004 provides for electric power, petrochemical, metallurgical station application of the cable standards.
Fourth, the difference between waterproof cable and ordinary non-waterproof cable
Waterproof cable made of special materials, with greater waterproof, moisture, corrosion, oil resistance, can be in the wet, high humidity, oil pollution and other environments to play its function well. Non-waterproof cables, on the other hand, are relatively poor and not suitable for these environments.
Therefore, TST CABLES suggests that enterprises need to choose the appropriate cable according to the actual need when choosing cables. If it is humid, easy to water pollution environment, you should choose waterproof cable; if it is dry, ordinary indoor environment, you can choose not waterproof cable.
Five, waterproof cable purchase strategy:
Power engineering cable in the production and manufacture of the whole is not allowed to enter the water, the cable must be dry internally, due to the harsh electric field operating voltage experiments, so the water into the cable can never leave the factory. Once the cable into the water, under the effect of electric field, will produce water tree embrittlement condition, will cause the cable penetration. Insulation in the residue, out of air holes and insulation and its outer semi-conductive layer of fusion surface of the disproportionate residence generated by part of the high electric field position is the starting point of the water tree. The direct entry of water into low voltage power engineering cables causes galvanic corrosion of the strip, copper foils etc. and a reduction in the insulation characteristics. When water passes through the insulation, it can cause cable penetration, and even explosions causing injuries and so on. Cable into the water after drying solution is very difficult, generally not equipped with the corresponding machinery and equipment. During operation, if the cable R6 into the water, generally just saw off the front of how many meters, such as into the cable has been into the water, then it can not be used. Therefore, to avoid water in the cable to prevent problems before they occur is particularly critical.
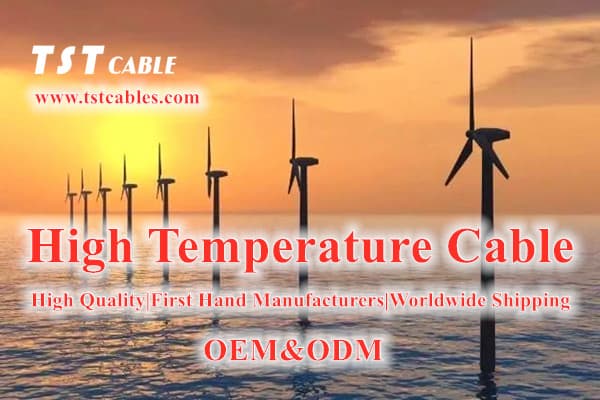
- Moisture-proof cable head should be sealed: saw off the edge of the cable, whether it is piled up or laid, should be sealed up with plastic (choose the cable special type of sealing sleeve), to avoid moisture penetration.
- Moisture-proof cable head production: cable lines should be laid immediately after the production of cable head.
- When purchasing moisture-proof cable, be sure to pick a solid quality manufacturer. Because the residue in the insulation, air holes, etc. is the starting point of the water tree, so the quality of the cable is particularly important to avoid water tree embrittlement.
- Enhance the management of moisture-proof cable head processing technology: once the cable into the water, then penetrate the situation is usually the cable head, so the cable head is well made, can increase the overall service life of the cable.
- Selection of heat-shrinkable cable head: heat-shrinkable silicone cable fittings, the production of simple and convenient, no gas furnace, no need for solder wire. And silicone cable fittings have ductility, firmly affixed to the cable, get rid of the defects of heat-shrinkable materials.
- Selected PVC/XLPE (cross-linked polyethylene)/Ethylene Propylene Rubber insulating material cable: the pipe has excellent insulation, heat, cold and moisture resistance as well as better waterproof performance. Corrosion resistance, inner cavity is smooth, compressive strength and ductility is excellent, so when the cable is laid directly buried, it can greatly reduce the cable outer sheath damage. It is mainly used in high-rise buildings, subways, highways, tunnels, nuclear power wind power, ocean engineering, petrochemical natural gas and other wet, high temperature, high pressure and other complex environments. Your final choice of which waterproof material cable, you need to confirm with a professional waterproof cable manufacturer engineers after detailed communication, so as not to buy the wrong.
- Pay attention to the safety of waterproof cable:
Choose waterproof cables that comply with relevant standards and regulations, such as having UL, CE, EN and other certifications to ensure the safety performance of waterproof cables. - Consider the special environmental conditions of waterproof cable:
Cables used in special environmental conditions (such as high temperature, high humidity, corrosion, etc.) need to pay special attention to their weather resistance and moisture and waterproof, corrosion resistance. - High-temperature waterproof suppliers of technical information and certification:
Ensure that waterproof cable suppliers to provide complete technical information and certification documents, so that there is a clear reference and guidance in the use of the process. - Consider waterproof cable supplier after-sales service:
Choose waterproof cable suppliers with good after-sales service, such as TST CALBES has one-on-one engineers to provide full pre-sales and after-sales guidance, so that the cable can be resolved in a timely manner when problems arise during use.
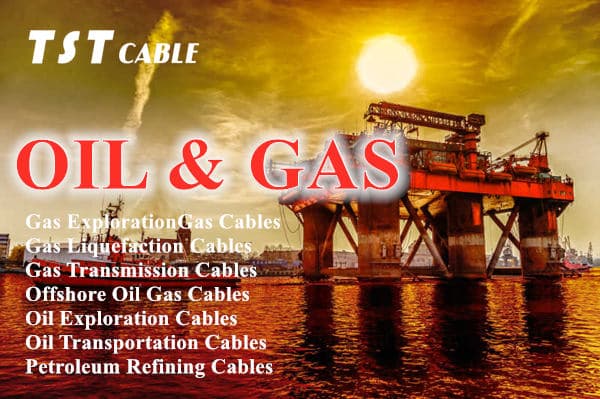
Waterlogged cables are a common problem that can adversely affect the normal operation of power systems. In order to avoid the harm caused by waterlogged cables, we should start from the design, installation, maintenance and other aspects, and take emergency measures. Only in this way can we ensure the normal operation of the power system and avoid the occurrence of power accidents.
TST CABLES waterproof Cables Manufacturer, the guardian of global electrical transmission safety! TST CABLES waterproof cable products use top waterproof materials and unique technology, with excellent waterproof, moisture-proof, high and low temperature resistance, low smoke and halogen-free flame retardant, anti-electromagnetic interference, corrosion and other characteristics, to adapt to a variety of extremely harsh environments, to ensure the stable operation of your electrical system. No matter where you are in the world, whether it is aerospace, rail transportation, nuclear power, wind power, marine engineering, petrochemical gas or construction projects, TST CABLES waterproof cables can provide you with the most reliable power transmission guarantee.
TST CABLES–Specializing in high temperature resistant cable applications and solutions
Fluoroplastic Cables|Polyimide (PI) Cables|Polyetheretherketone (PEEK) Cables|Silicone Rubber Cables
Rail way | Aviation | Marine | Nuclear | Oil & Gas | Wind Power industry applications
For more information on waterproof Cables,Silicone Cables,low-smoke, halogen-free, flame-retardant, high-temperature-resistant cables or to customize cables for your machinery or system, visit https://www.tstcables.com/product/
or send an e-mail to:lixiangchao@testeck.com
Also available in:
English