
- Home
- /
- Unit function control system
Application of Cables in Wind Turbine Equipment Control Systems
1. Scene Introduction
With the optimization of the global energy structure and the enhancement of environmental protection awareness, wind power generation, as an important part of clean energy, has been developed rapidly. As a crucial connecting part of the wind power system, the performance and quality of the cables of the wind turbine equipment control system directly affect the safe and stable operation of the wind power system. Therefore, it is especially critical to design a set of efficient, stable and reliable cable solutions for wind turbine equipment control system.
Wind Turbine Cables: The mechanical energy generated by the turbine blade rotation needs to be converted into electrical energy, and this process involves the transmission of electricity between the generator and the turbine, thus requiring cable connections.
Generator cables: The power generated inside the generator needs to be transported via cables to the wind farm’s converter or substation, which in turn is connected to the grid.
Converter cables: The converter is responsible for converting the power generated by the generator into a voltage and frequency suitable for the grid, and cables are needed to connect the generator to the converter during this conversion process.
Control system cables: The control system of a wind turbine includes sensors, data acquisition systems, data processing systems and actuator systems, which require cables to transfer signals between them and to the control room.
Safety system cables: wind turbines are also equipped with safety systems, such as emergency stop buttons, fire alarm systems, etc. The signal transmission of these systems also requires cable support.
Communication system cables: wind turbines need to communicate with the wind farm control center or other equipment to achieve remote monitoring, data transmission and fault diagnosis and other functions, communication cables play an important role in this process.
2. The pain point analysis
In the application of cables in the control system of wind turbine equipment, there are several major pain points: firstly, wind farms are usually located in remote areas with harsh environments, and the cables need to withstand the impact of extreme climatic conditions; secondly, the cables need to transmit a large number of control signals and power, which has high requirements for the electrical performance of the cables; in addition, the wind power system has strict requirements for the reliability and safety of the cables in order to ensure the stable operation of the wind farm. Stable operation of the wind farm.
3.The wind turbine equipment control system on the cable requirements
Wind turbine equipment control system on the cable requirements mainly include: excellent electrical performance, high reliability, good environmental adaptability, strong resistance to electromagnetic interference, low attenuation, high bandwidth and so on. Cables also need to meet the special environment of the wind farm fire, water, weather and other requirements.
4. The certification standards
In order to ensure that the performance and quality of the cables meet the highest standards in the industry, TST CABLES products fully comply with the following international and domestic certification standards:
UL Certification: The Underwriters Laboratories of the United States of America conducts rigorous testing of the electrical and mechanical properties of the cable to ensure that it meets safety standards.
CE certification: A mark of conformity with the requirements of the European Union directives, indicating that the cable meets the requirements of the European Union’s regulations on safety, health, and environmental protection.
RoHS certification: A directive restricting the use of certain hazardous substances, ensuring that cables are environmentally friendly during production and use.
In addition, our cables meet industry-specific standards such as IEC 60228, IEC 60754, IEC 60332 (standard for combustion performance of cables) and EN 50264, GB/T 2423.1, GB/T 2423.2, IEC 60068-2-1, IEC 60068-2-2, EN 60068-2-1, EN 60068-2-2, etc. to ensure the safety and reliability of the cables in applications.
In addition, the cable products also need to pass the specific certification of the wind power industry to ensure that they are adapted to the special operating environment of wind farms.
5.Product Selection
According to the requirements of wind turbine equipment control system, TST CABLES recommends the selection of cable products with excellent electrical performance, high reliability and good environmental adaptability. Specifically, low-smoke halogen-free flame retardant cables can be selected to meet the fire protection requirements of wind farms; at the same time, cable sheath materials with excellent weather resistance are selected to cope with the harsh outdoor environment.
Selection parameters for reference (can be customized according to actual needs)
Rated voltage: 300V AC
Temperature range: -40°C to 90°C
Bending radius: 6D (D refers to the outer diameter of the cable)
Characteristic impedance: 120Ω+12Ω (0.75~3MHz)
Attenuation: <1.5dB/100m (1.5MHz), <2.0dB/100m (3MHz)
Operating Capacitance: <46pF/m (1.0MHz)
Transmission Impedance: <20mΩ/m (20MHz)
Tinned Copper
Antioxidant
High conductivity
Wear-resistant
No deformation
6. Product Characteristics
The cable products in this solution have the following remarkable characteristics:
Excellent electrical performance: the cable conductor is made of high-purity copper, and the insulating material has excellent insulation performance and electrical stability, ensuring that the cable has low attenuation and high bandwidth when transmitting control signals and electrical energy.
High reliability: the cable adopts multi-layer shielding structure to effectively resist electromagnetic interference and ensure the accuracy and stability of data transmission. Meanwhile, the cable joints are processed with special technology to ensure reliable connection and not easy to loosen.
Good environmental adaptability: the cable sheath is made of weather-resistant material, which can keep the electrical performance stable under extreme climatic conditions. In addition, the cable also has excellent waterproof and fireproof performance, ensuring safe operation even in harsh environments.
Recommended Products
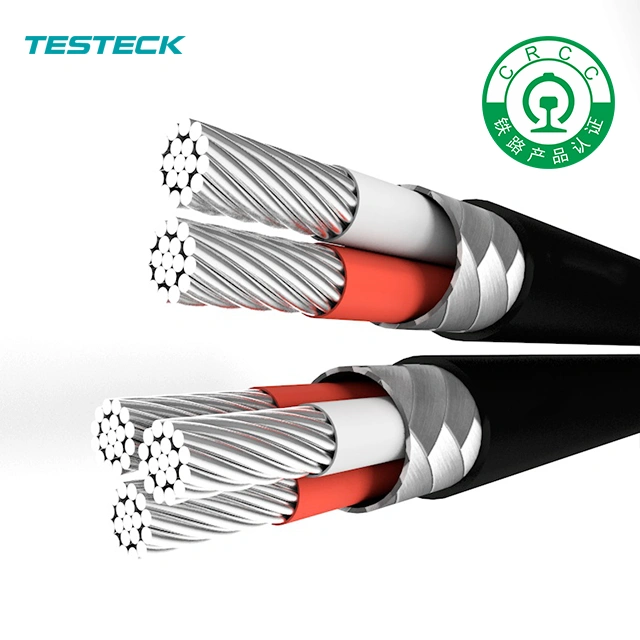
The wind turbine functional control system cable is suitable for harsh environments and is wear-resistant. It is an essential component in the wind turbine system and is responsible for transmission between the control unit and the functional components of the wind turbine (such as the pitch system, generator, and braking system). control signal.
7.Technical Tests
In order to ensure the performance and quality of the cable products, TST CABLES has carried out a series of strict technical tests.
Electrical performance test: the electrical performance of the cable is stable, in line with the design requirements, and can meet the needs of wind farms for power transmission and control signal transmission.
Environmental adaptability test: the cable passed the test under extreme conditions such as high salt spray, strong wind and big waves, proving that it can operate stably for a long time under the harsh marine environment.
Low-smoke halogen-free flame retardant and fire resistance performance test: low-smoke halogen-free, the cable’s flame retardant performance reaches grade A, and the fire resistance time is more than 1 hour, which meets the safety requirements of offshore wind farms.
Electromagnetic compatibility test: the cable has a strong anti-electromagnetic interference capability, which can effectively resist the interference signals in the complex electromagnetic environment of wind farms.
A number of test results show that the cable products in TST CABLES wind power solutions meet the design requirements in various properties, and can meet the needs of the wind turbine equipment control system.
8. Cable laying installation and commissioning
TST CABLES provides professional cable laying installation and commissioning services to ensure that the wind turbine equipment cable can be correctly and safely connected to the wind turbine equipment control system. In the process of laying, TST CABLES strictly abide by the safety regulations to ensure that the cable is not damaged; in the commissioning stage, we conduct a comprehensive inspection of the cable to ensure the accuracy and stability of data transmission.
9. After-sales maintenance & technical support
TST CABLES provides comprehensive after-sales maintenance and technical support services to ensure that customers encounter problems in the process of use can be resolved in a timely manner. We have a professional technical team that can provide customers with technical advice, troubleshooting and maintenance services to ensure the stable operation of the wind turbine equipment control system.
10.Actual Cases
This project is located in the sea off the eastern coast of China, with a total installed capacity of 500 MW, including 100 wind turbines.TST CABLES takes into account the special characteristics of the offshore environment, the project party pays special attention to the selection and application of the control system cables of the wind turbine equipment to ensure the stable operation of the wind farm.
Application effects
Failure rate reduction: Since the installation of the cable, the failure rate of the wind turbines has been reduced by 90%, of which the failure rate related to the control system has been reduced by 85%.
Stability of data transmission: The stability of control signal transmission has increased by 90%, ensuring the stable operation of the wind farm and efficient power generation.
Cable performance: After two years of operation, the electrical performance and environmental adaptability of the cable have remained good, with no significant aging or damage.
Other solutions for cables in wind power applications.
WHY CHOOSE TST CABLES
10 years of experience
Specializing in the production of railway cables for 10 years
Engineer-to-engineer one-on-one support
Engineers provide one-on-one service to assist with product selection and problem-solving
Customization according to requirements
With a strong R&D team, we support customized cables based on specific needs
Quality certification
Stringent adherence to industry standards, complete certification
Fully testing facilities
Various tests based on customer requirements
10,000 ㎡ factory
Welcome to visit our factory face to face
RELATER NEWS
Also available in:
Arabic
English
German
Indonesian
Japanese
Russian
Spanish
Thai
Vietnamese
Portuguese (Brazil)