triplex cable (Three-core cable) is a common type of power transmission cable, widely used in residential, commercial and industrial power distribution systems. It consists of three independent conductors and is usually used for power distribution in three-phase alternating current (AC) systems. Three-core cable is widely used in various occasions due to its high efficiency and reliability. Understanding its characteristics and scope of application can help better plan and implement power engineering projects. Whether in new buildings or upgrades to existing facilities, the rational selection of three-core cables can provide users with a stable and reliable power supply. Below, TST CABLES will take you to learn some relevant information about three-core cables.
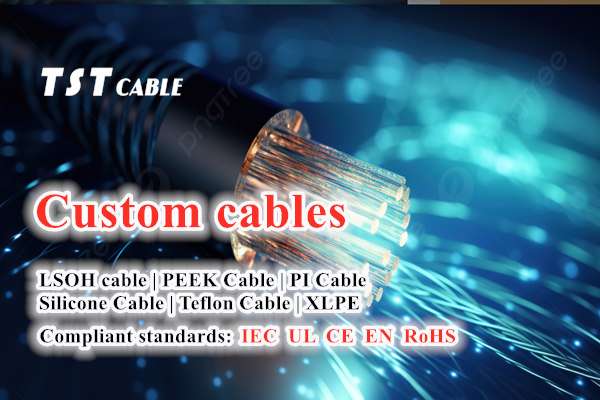
Three-core cable structural features
Three conductors: Each conductor is responsible for transmitting one phase (A, B, C) of the three-phase electricity, which makes it effective in supporting three-phase loads.
Insulation layer: Each conductor is wrapped with a layer of insulating material to prevent short circuits and other electrical faults. Commonly used insulating materials include polyvinyl chloride (PVC), cross-linked polyethylene (XLPE cable), etc.
Protective layer/sheath: In addition to all conductors, there is an outer sheath to provide additional mechanical protection, and sometimes a shielding layer is included to reduce electromagnetic interference.
Application scenarios of three-core cables
Residential buildings: Suitable for powering homes, especially when they need to be connected to a three-phase power supply.
Commercial facilities: Office buildings, shopping malls and other places often use three-core cables for power distribution.
Industrial use: Factories and manufacturing plants often rely on three-core cables to meet the power needs of large mechanical equipment.
Infrastructure projects: Three-core cables may also be used in road lighting, tunnel projects, etc.
Advantages of three-core cables
High efficiency: Three-phase systems are more efficient than single-phase systems, especially when transmitting high power over long distances.
Good stability: Since the current is evenly distributed between the three phases, voltage drops and harmonic distortion are reduced.
Easy installation: Compared with multiple single-core cables, using a three-core cable simplifies the installation process and reduces costs.
Precautions for three-core cables
Choose the right specification: It is very important to choose the appropriate cable size according to the actual load requirements. Too small may cause overheating or even fire risks.
Environmental adaptability: Consider the laying environment conditions (such as temperature, humidity, corrosive soil, etc.) and choose cables with corresponding protection levels.
Safety measures: Ensure proper grounding and follow relevant safety regulations and standards.
Selecting the right three-core cable requires a comprehensive consideration of multiple factors to ensure the safety, efficiency and reliability of power transmission. Below are some suggestions from TST CABLES cable engineers on the key points to consider when selecting three-core cables.
1. Determine the electrical load requirements
Power requirements: Calculate the required current based on the total power of the load (kW or kVA).
Voltage level: Confirm the rated voltage of the system, which will directly affect the choice of cable. Common low-voltage system voltages are 230V/400V, while medium-voltage systems may reach 10kV or higher.
Number and type of phases: Since a three-core cable has been selected, it is suitable for three-phase alternating current (AC) systems.
2. Three-core cable cable size
Current carrying capacity: Select the appropriate conductor cross-sectional area based on the expected maximum current. Cables of different specifications have different current carrying capacities, and too small a current carrying capacity may cause overheating or even fire risks.
Ambient temperature: When working in a high-temperature environment, a cable with a larger cross-section needs to be selected to compensate for the decrease in current carrying capacity caused by the increase in temperature.
Laying method: Different laying conditions such as whether the cable is laid openly in the air, laid in a conduit or buried underground will affect its maximum allowable current carrying capacity.
3. Insulation material
PVC (polyvinyl chloride): low cost, suitable for general indoor applications, but not suitable for extreme temperature environments.
XLPE (cross-linked polyethylene): good temperature resistance, can be used in higher temperature occasions, suitable for outdoor or underground laying.
Other special materials: such as halogen-free flame retardant materials, suitable for places with strict fire protection requirements.
4. Mechanical protection
Armor type: For areas susceptible to mechanical damage, cables with steel belt or steel wire armor can be selected for additional protection.
Sheath material: usually PVC or PE (polyethylene), the latter is more suitable for outdoor use because it has better UV resistance and weather resistance.
5. Environmental adaptability
Humidity and water immersion: If the cable needs to be installed in a humid environment or may be immersed in water, a waterproof cable should be selected.
Chemical corrosion: Corrosive gases or liquids may exist in some industrial environments. At this time, cables with corresponding protection capabilities should be selected.
Rodent or other biological damage: Anti-gnawing design may also need to be considered in certain areas.
6. Regulatory compliance
Make sure the selected cable complies with local electrical installation standards and specifications, such as IEC, GB (China National Standard), BS (British Standard), DIN (German Industrial Standard), etc.
7. Cost-benefit analysis
Consider the initial investment cost while also evaluating the long-term operating costs, including maintenance costs and potential energy losses.
For large projects, a life cycle cost analysis is sometimes required to determine the most cost-effective option.
8. Supplier reputation and service support
Choose reputable manufacturers and suppliers to ensure reliable product quality and timely technical support and service guarantees.
With the above considerations, you can more accurately select three-core cable products that meet your specific needs. It is important to note that in actual operation, you should also consult TST CABLES professional electrical engineers or consultants to ensure that all safety and technical requirements are met. If you have any questions about three-core cables, please email us and get free samples.
Three-core 26/35KV (Um=42KV) cable structure parameters
Nominal cross-sectional area | Unarmored Cable | Round wire armor | |||||||||||
Insulation nominal thickness | Copper tape thickness | Copper wire shielding area | Nominal sheath thickness | Approximate outer diameter | Approximate Weight | Nominal pad thickness | Armor thickness | Nominal thickness of sheath | Approximate outer diameter | Approximate Weight | |||
CU | AL | CU | AL | ||||||||||
mm2 | mm | mm | mm2 | mm | mm | kg/km | mm | mm | mm | mm | kg/km | ||
50 | 10.5 | 0.1 | 16 | 3.4 | 79.7 | 5928 | 5053 | 1.9 | 3.5 | 4.0 | 93.5 | 12050 | 11150 |
70 | 10.5 | 0.1 | 16 | 3.5 | 83.6 | 6900 | 5634 | 2.0 | 4.0 | 4.1 | 97.5 | 13150 | 11850 |
95 | 10.5 | 0.1 | 16 | 3.6 | 87.2 | 7863 | 6131 | 2.1 | 4.0 | 4.2 | 101.5 | 14800 | 12950 |
120 | 10.5 | 0.1 | 16 | 3.8 | 90.7 | 8817 | 6634 | 2.2 | 4.0 | 4.4 | 105.5 | 16050 | 13800 |
150 | 10.5 | 0.1 | 25 | 3.9 | 94.1 | 10085 | 7361 | 2.3 | 4.5 | 4.5 | 108.5 | 17420 | 14640 |
185 | 10.5 | 0.1 | 25 | 4.0 | 99.1 | 11573 | 8120 | 2.3 | 4.5 | 4.6 | 112 | 19200 | 15700 |
240 | 10.5 | 0.1 | 25 | 4.1 | 103.6 | 13387 | 9023 | 2.4 | 4.5 | 4.7 | 117 | 21050 | 16800 |
300 | 10.5 | 0.1 | 25 | 4.3 | 109.2 | 15658 | 10060 | 2.5 | 4.5 | 4.8 | 122.5 | 24900 | 19100 |
400 | 10.5 | 0.1 | 35 | 4.5 | 115.6 | 19013 | 11657 | 2.6 | 4.5 | 5.1 | 129 | 29200 | 21560 |
*Copper tape composite can be used as an option for the shielding layer. The shielding nominal area is shown in the table above for reference. TST CABLES can also customize cables with other parameters you need.
Flat steel wire armor | Double steel belt armor | |||||||||||
Nominal cross-sectional area | Nominal thickness of cushion layer | Armor size | Nominal thickness of sheath | Approximate outer diameter | Approximate Weight | Nominal thickness of cushion layer | Armor size | Nominal thickness of sheath | Approximate outer diameter | Approximate Weight | ||
CU | AL | CU | AL | |||||||||
mm2 | mm | mm | mm | mm | kg/km | mm | mm | mm | mm | kg/km | ||
50 | 1.9 | 0.8 | 3.5 | 86.5 | 10880 | 9990 | 1.9 | 2×0.8 | 3.7 | 87.5 | 10690 | 9800 |
70 | 2.0 | 0.8 | 3.6 | 90.5 | 12000 | 10795 | 2.0 | 2×0.8 | 3.8 | 91.4 | 10800 | 10590 |
95 | 2.1 | 0.8 | 3.8 | 94.0 | 13360 | 11570 | 2.1 | 2×0.8 | 3.9 | 95.2 | 13110 | 11327 |
120 | 2.2 | 0.8 | 3.9 | 96.4 | 13705 | 12710 | 2.2 | 2×0.8 | 4.0 | 98.7 | 14300 | 12110 |
150 | 2.3 | 0.8 | 4.0 | 99.5 | 16160 | 13440 | 2.3 | 2×0.8 | 4.1 | 102.1 | 15550 | 12800 |
185 | 2.3 | 0.8 | 4.1 | 105.1 | 18505 | 14465 | 2.3 | 2×0.8 | 4.2 | 107.3 | 17810 | 13765 |
240 | 2.4 | 0.8 | 4.2 | 109.8 | 20390 | 15890 | 2.4 | 2×0.8 | 4.4 | 112.2 | 19650 | 15150 |
300 | 2.5 | 0.8 | 4.4 | 115.5 | 22970 | 17280 | 2.5 | 2×0.8 | 4.6 | 118.0 | 22200 | 16500 |
400 | 2.6 | 0.8 | 4.6 | 122.1 | 26600 | 19430 | 2.6 | 2×0.8 | 4.8 | 124.6 | 25780 | 18600 |
Electrical performance parameters
Nominal cross-sectional area | DC resistance CU / AL | AC resistance CU / AL | Conductor short circuit rating CU / AL 1 sec | capacitance | Charging Current | Copper wire shield short circuit rating per core 1 sec | Copper tape shield short circuit rating per core 1 sec | inductance | Reactance |
mm² | µΩ/m | µΩ/m | kA | pF/m | mA/m | kA | kA | µΩ/m | nH/m |
50 | 387/641 | 494/822 | 6.8/4.4 | 131 | 0.97 | 2.6 | 1.2 | 146 | 470 |
70 | 268/443 | 343/568 | 9.8/6.3 | 145 | 1.07 | 2.6 | 1.2 | 139 | 430 |
95 | 193/320 | 248/410 | 13.3/8.5 | 158 | 1.18 | 2.6 | 1.3 | 132 | 420 |
120 | 153/253 | 196/325 | 17.2/11.0 | 169 | 1.26 | 2.6 | 1.3 | 128 | 400 |
150 | 124/206 | 159/265 | 21.2/13.5 | 178 | 1.36 | 4.3 | 1.4 | 123 | 390 |
185 | 99.1/164 | 128/211 | 26.6/17.0 | 185 | 1.44 | 4.3 | 1.4 | 118 | 380 |
240 | 75.4/125 | 98/161 | 34.9/22.3 | 203 | 1.57 | 4.3 | 1.5 | 113 | 360 |
300 | 60.1/100 | 80/130 | 43.8/28.0 | 219 | 1.72 | 4.3 | 1.6 | 109 | 350 |
400 | 47.0/77.8 | 64/102 | 57.3/36.6 | 245 | 1.85 | 5.8 | 1.7 | 105 | 320 |
Also available in:
Arabic
English
Japanese
Russian
Portuguese (Brazil)