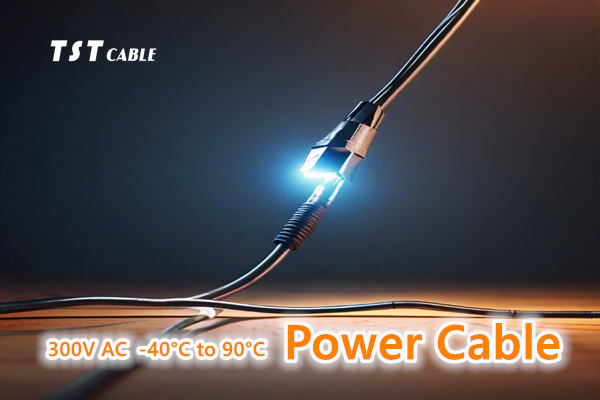
I. Introduction to power cables
Power cable is used for transmission and distribution of electrical energy cables, power cables are commonly used in urban underground power grids, power station lead lines, industrial and mining enterprises internal power supply and underwater transmission lines across the river and sea.
In the power line, the proportion of cable is gradually increasing. Power cables are used to transmit and distribute high-power power cable products in the backbone of the power system, including 1-500KV and above, various voltage levels, a variety of insulated power cables.
Second, the historical development of power cables
The use of power cables has been more than a hundred years of history. 1879, the American inventor T.A. Edison in the copper rods wrapped around the jute and will be threaded into the iron pipe, and then filled with asphalt mixture made of cable. He laid this cable in New York, creating underground power transmission. The following year, the British Callender invented asphalt-impregnated paper-insulated power cables. 1889, the British S.Z. Ferranti in London and Detford between the laying of 10 kV oil-impregnated paper-insulated cables. 1908, the United Kingdom built a 20 kV cable network. Power cables are more and more widely used. 1911, Germany laid into 60 kV high-voltage cable, began the development of high-voltage cables. 1913, the German M. Hochstetter developed phase-shielded cables, improve the electric field distribution inside the cable, eliminating the tangential stress on the insulation surface, becoming a milestone in the development of power cables. 1952, Sweden in the north of the power plant laid 380 Kilovolt ultra-high voltage cable, the realization of the application of ultra-high voltage cable. To the 80s has been made 1100 kV, 1200 kV of ultra-high voltage power cables.
Third, the classification of power cables
According to the voltage level
According to the voltage level can be divided into medium and low-voltage power cables (35 kV and below), high-voltage cables (110 kV and above), ultra-high-voltage cables (275-800 kV) and ultra-high-voltage cables (1000 kV and above). In addition, they can be divided into AC cables and DC cables according to the current system.
According to the insulation material
- oil-impregnated paper-insulated power cables to oil-impregnated paper as the insulation of power cables. Its application history is the longest. It is safe, reliable, long service life, low price. The main drawback is that the laying of the drop restrictions. Since the development of non-drip paper-immersed insulation, to solve the problem of fallout restrictions, so that oil-impregnated paper-insulated cables to continue to be widely used.
- Plastic insulated power cables Insulation layer of extruded plastic power cables. Commonly used plastics are polyvinyl chloride, polyethylene, cross-linked polyethylene. Plastic cable structure is simple, easy to manufacture and process, light weight, easy to lay and install, not subject to the restrictions of laying the fall. Therefore, it is widely used for low and medium voltage cables, and there is a trend to replace the viscous impregnated oil paper cable. Its biggest drawback is the existence of dendritic breakdown phenomenon, which limits its use in higher voltage.
- Rubber insulated power cables Insulation layer of rubber with a variety of agents, after sufficient mixing and extrusion package in the conductive core, after vulcanization and temperature. It is soft, flexible, suitable for frequent movement, laying of small bending radius occasions.
Commonly used for insulation rubber material has natural rubber – butyl rubber mixture, ethylene propylene rubber, butyl rubber, etc..
According to the voltage level
- Low-voltage cable: suitable for fixed laying in AC 50Hz, rated voltage 3kv and below on the transmission and distribution lines for the transmission of electrical energy.
- Medium and low voltage cables: (generally refers to 35KV and below): PVC insulated cables, polyethylene insulated cables, cross-linked polyethylene insulated cables and so on.
- High-voltage cables: (generally 110KV and above): polyethylene cables and cross-linked polyethylene insulated cables.
- Ultra-high voltage cables: (275-800KV).
- Extra-high voltage cable: (1000KV and above).
Fourth, the basic structure of power cables
Any kind of power cable, its basic structure by the conductive core, insulation and protective layer of three basic parts.
Power cable conductive core
Core is the conductive part of the power cable, used to transport electrical energy, is the main part of the power cable. Core loss is mainly determined by the conductor cross-section and the conductivity of the material. In order to reduce the loss of cable core, cable core is generally made of copper or aluminum with high conductivity.
Power cable insulation
Insulation is the core and the earth and different phases of the core in the electrical isolation from each other, to ensure the transmission of electrical energy, is an indispensable part of the structure of the power cable. The insulation layer isolates the core conductor from the protective layer and prevents leakage. Insulation layer is used to withstand the role of voltage, the work of the field is very high, due to the insulation layer will inevitably remain some bubbles, these bubbles in the role of strong electric field, it is easy to be ionized and produce partial discharge, and accompanied by the production of ozone corrosion of the insulating layer, so the insulating layer is required to have a corona-resistant good special. At present, 110kV and the following cable insulation materials, cross-linked polyethylene dominates.
Power cable shielding layer
15KV and above power cables generally have conductor shielding layer and insulation shielding layer.
6kV and above power cables, generally have conductor shielding layer and insulation shielding layer. The shielding layer shields the electromagnetic fields generated by the current in the cable to protect the surrounding components. When there is a breakage in the cable, the leakage current will flow down the shielding layer into the grounding grid, thus providing a protective function.
Power cable protective layer
The role of the protective layer is to protect the power cable from external impurities and moisture intrusion, as well as to prevent direct damage to the power cable from external forces. The protective layer is divided into the inner and outer protective layer, which is used to protect the insulation layer. The quality of the protective layer is directly related to the service life of the cable. The concentric layer located between the armor layer and the metal sheath is the protective layer. The filler of the high voltage power cable is also the protective layer.
Fifth, the advantages of power cables
- Occupies less land. Generally buried in the soil or laid in the room, trench, tunnel, small insulation distance between the lines, without the tower, occupying less, basically does not occupy space on the ground.
- High reliability. Subject to climatic conditions and the surrounding environment has little impact, stable transmission performance, high reliability.
- With ultra-high voltage, high-capacity development of more favorable conditions, such as low temperature, superconducting power cables.
- Large distribution capacitance.
- Less maintenance workload.
- The possibility of electric shock is small.
Sixth, the technical characteristics of power cables
1) can withstand high and even very high working voltage for a long time, should have very good electrical insulation properties.
2) can transmit a very large current (nine hundred or even thousands of amps), and therefore will be used to hide the cross-sectional area of hundreds or even thousands of square millimeters of conductive core.
3) power cable adopts a variety of combinations of protective layer structure, can adapt to a variety of laying methods and use of the environment (underground, underwater trench pipe, tunnels, shafts).
In fact, power cables rely on high-voltage insulation technology, large colonization transmission technology, as well as structural balance, protective layer structure, etc. are representative of these aspects of the academic level of electrical engineering disciplines.
Seven, power cable features
- cross-linked polyethylene insulated cable has excellent dielectric properties, but corona resistance, free discharge performance is poor.
- polyethylene insulated cable process performance, easy to process, poor heat resistance, heat deformation, easy to delay combustion, easy to crack.
- PVC insulated cables are chemically stable, non-combustible, and the material source is sufficient.
- Power cable insulation performance is higher oil-impregnated paper insulated cable.
Eight, power cable requirements
(1) can withstand the grid voltage. Including operating voltage, fault overvoltage and atmospheric and operational overvoltage.
(2) can transmit the power that needs to be transmitted. Including normal and fault conditions of the current.
(3) Can meet the installation and laying, use of the mechanical strength and curvature required, and durable and reliable; (4) rich source of materials, economic, simple technology, low cost.
Nine, the power cable model description
- The first letter of Hanyu Pinyin in capital letters represents the insulation type, conductor materials, inner sheath materials and structural features. For example, Z on behalf of paper (zhi); L on behalf of aluminum (lv); Q on behalf of lead (qian); F on behalf of the split-phase (fen); ZR on behalf of flame retardant (zuran); NH on behalf of fire-resistant (naihuo).
- The composition of the outer armor layer is indicated by a number with two digits. No number represents no armor layer, no outer being layer. The first digit represents the armor, the second digit represents the outer being, such as thick steel wire armored fiber outer being expressed as 41.
- Cable model according to the arrangement of the cable structure is generally sequential order: insulation materials; conductor materials; inner sheath; outer sheath.
- Cable products with models, rated voltage and specifications. The method is in the model and then add the description of the rated voltage, the number of cores and nominal cross-sectional area.
Detailed description of the model number of power cables
(1) Category: H – municipal communications cable
HP – wiring cable
HJ–Local Cable
(2) Insulation: Y – polyethylene insulation
YF – foam polyolefin insulation
YP–Foam/solid skin polyolefin insulation
(3) Inner Sheath: A – plastic coated aluminum tape bonded shielded polyethylene sheath
S–Aluminum, steel double-layer metal tape shielded polyethylene sheath
V–Polyvinyl chloride sheath
(4) Characteristics: T — petroleum paste filling
G–High frequency isolation
C–Self-supporting
(5) Sheathing: 23 – double-layer corrosion-resistant steel tape wrapped around the pin mounted polyethylene outer layer
33 – single-layer fine steel wire armored polyethylene cover layer
43 – single layer of coarse steel wire armored polyethylene cover layer
53 – Single-layer wrinkled steel tape wrapped longitudinally armored polyethylene cover layer
553–Double-layer wrinkled longitudinally wrapped polyethylene cover layer with steel tape
(2) BV copper core PVC insulated wire;
BLV Aluminum core PVC insulated wire;
BVV copper core PVC insulated PVC sheathed wire;
BLVV Aluminum core PVC insulated PVC sheathed wire;
BVR Copper-core polyvinyl chloride insulated flexible wire;
RV Copper-core PVC insulated installation flexible cables;
RVB Copper coated PVC insulated flat connecting wire flexible cables;
BVS Stranded flexible cord with PVC insulation on copper core;
RVV copper core polyvinyl chloride insulated polyvinyl chloride sheathed flexible cables;
BYR Polyethylene insulated flexible cords;
BYVR polyethylene insulated polyvinyl chloride sheathed flexible cords;
RY Polyethylene insulated flexible cords;
RYV polyethylene insulated polyvinyl chloride sheathed flexible wire; RYV polyethylene insulated polyvinyl chloride sheathed flexible wire
3)WD: halogen-free and low smoke type
ZR: flame retardant
NH: Fire-resistant
DH: Fire-resistant type
Power cable current-carrying capacity
- The current-carrying capacity of power cables mainly depends on the maximum permissible temperature and the temperature of the surrounding environment of the cable, the structure of each part of the cable and material properties and other factors. So that the stabilized temperature of the conductor to reach the maximum allowable extortion temperature of the cable mother of the current-carrying capacity, known as the permissible current-carrying capacity or safety current-carrying capacity.
- Cross-linked polyethylene insulated cable conductor long-term allowable operating temperature of 90 ℃. Natural rubber insulated cable voltage class 6kW, the long-term allowable working temperature of the cable conductor is 65 ℃. Polyethylene insulated cable voltage level of 10k state, the cable conductor of the long-term allowable operating temperature of 70 ℃. Polyethylene insulated cable voltage class 6k, the cable conductor of the long-term allowable L work temperature of 65 ℃.
Ten, the common types of power cables
(1) V, VLV are copper-core, aluminum-core PVC-insulated PVC-sheathed power cables;
(2) V22, LV22 are copper-core, aluminum-core PVC-insulated double steel belt armored PVC sheathed power cables;
(3) Y22 is copper core cross-linked polyethylene insulated double steel belt armored PVC sheathed power cable;
(4) KT for polyvinyl chloride insulation polyethylene sheathed control cable.
Eleven, the common faults of power cables
Short-circuit faults: two-phase short circuit and three-phase short circuit, mostly for the manufacturing process left behind by the hidden problems.
Grounding faults: cable a core or a number of core to ground breakdown, the insulation resistance is lower than 10kΩ called low-resistance grounding, higher than 10kΩ called high-resistance grounding. Mainly due to cable corrosion, lead cracks, insulation dry, joints, process and materials.
Broken linear fault: cable a core or several cores completely broken or not completely broken. The cable is subject to mechanical damage, the influence of terrain changes or the occurrence of over-short circuit, can cause broken line situation.
Mixed faults: more than two of the above faults.
Power cable failure causes and countermeasures
External damage: in the cable storage, transportation, laying and operation process may be subjected to external damage, in particular, has been running directly buried cable, in the ground construction of other projects vulnerable to damage. These accidents often account for 50% of the cable accident. In order to avoid such accidents, in addition to strengthening the cable storage, transportation, laying and other aspects of the quality of work, it is more important to strictly enforce the earth moving system.
Protective layer corrosion: underground stray current of electrochemical corrosion or non-neutral soil chemical corrosion so that the protective layer failure, loss of insulation protection. The solution is, in the stray current intensive area of the installation of drainage equipment; when the cable line on the local soil contains damage to the cable lead package of chemical substances, the cable should be installed in the tube, and neutral soil for cable liner and cover, but also in the cable coated with asphalt.
Over-voltage, overload operation: improper selection of cable voltage, in operation, suddenly high pressure into or long-term overload, may make the cable insulation strength is damaged, the cable breakdown. This needs to be strengthened by inspection, improve the operating conditions to solve the problem in a timely manner.
Outdoor terminal head immersion: due to poor construction, insulation rubber is not filled, so that the terminal head immersion, and ultimately the explosion. Therefore, it is necessary to strictly implement the construction process regulations, careful acceptance; strengthen the inspection and timely maintenance. Leakage of oil from the terminal head destroys the sealing structure, causing the loss of impregnant drying at the end of the cable, increasing the thermal resistance, accelerating the aging of the insulation, and easily absorbing moisture, resulting in thermal breakdown. When oil leakage is found in the terminal head, inspection should be strengthened, and in serious cases, the power should be shut down and redone.
Power plants, substations and industrial and mining enterprises are a large number of power cables, once the cable fire and explosion, will cause serious fire and blackout accidents, in addition, the cable combustion produces a large amount of smoke and poisonous gas, not only pollute the environment, but also endanger the safety of human life. For this reason, attention should be paid to the power cable fire.
Twelve, power cable fire causes
Power cable insulation is composed of paper, oil, hemp, rubber, plastic, asphalt and other combustible substances, therefore, the cable has the possibility of fire and explosion. Causes of cable fire and explosion are:
(1) insulation damage caused by short-circuit failure. Power cable protection lead skin in the laying of the cable was damaged or in operation cable insulation by mechanical damage, caused by the cable phase or between the lead skin insulation breakdown, the arc generated so that the insulation material and the cable outside the protective layer of material combustion fire.
(2) Cable overload operation for a long time. Prolonged overload operation, the operating temperature of the cable insulation material exceeds the maximum permissible temperature of normal heating, so that the cable insulation aging and drying, this insulation aging and drying phenomenon, usually occurs in the entire cable line. As the cable insulation aging dry, so that the insulating material to lose or reduce the insulating properties and mechanical properties, and thus prone to breakdown fire burning, and even along the entire length of the cable at the same time in a number of combustion fires.
(3) oil-immersed cable due to the difference in height occurs flow, oil leakage. When the oil-immersed cable laying height difference is large, may occur when the cable flow oil phenomenon. The result of the flow, so that the upper part of the cable due to the loss of oil and dry, the thermal resistance of this part of the cable increases, so that the paper insulation is scorched and premature breakdown. In addition, as the upper part of the oil downward flow, in the upper cable head to make space and generate negative pressure, so that the cable is easy to absorb moisture and make the end of the moisture. The lower part of the cable due to the accumulation of oil and generate a lot of static pressure, prompting the cable head oil leakage. Cable moisture and oil leakage have increased the chance of fire failure.
(4) Intermediate joint box insulation breakdown. Cable joint box intermediate joints due to crimping is not tight, welding is not secure or improper choice of joint materials, running joint oxidation, heat, glue flow; in the middle of the cable joints, filling in the intermediate joint box insulating agent quality does not meet the requirements of the filling insulating agent, the box within the memory of the air holes and cable box sealing is poor, damaged and leaking into the moisture, the above factors can cause insulation breakdown, forming a short circuit, so that the cable explosion fire. The above factors can all cause insulation breakdown, forming a short circuit, making the cable explode and catch fire.
(5) Cable head burning. Due to the moisture on the surface of the cable head accumulation of dirt, cable head ceramic casing rupture and lead wire phase distance is too small, resulting in flashover fire, causing the cable head surface insulation and lead wire insulation burning.
(6) External fire and heat sources lead to cable fires. Such as the spread of fire in the oil system, the spread of the oil circuit breaker explosion fire, boiler pulverizing system or coal system coal dust spontaneous combustion, high temperature steam pipe baking, chemical corrosion of acids and alkalis, welding sparks and other fires, can make the cable fire.
Thirteen, power cable fighting methods
Once the cable fire, the following methods should be used to extinguish:
(1) cut off the fire cable power supply. Cable fire burning, regardless of the cause, should immediately cut off the power supply, and then, according to the path and characteristics of the cable through the careful inspection, to find out the fault point of the cable, at the same time, should quickly organize personnel to fight.
(2) cable trench fire non-fault cable power cut off. When the cable fire in the cable trench burning, if the cable with the trench and laying side by side with the obvious possibility of fire, the cable should be cut off the power supply. If the cable is arranged in layers, the first fire cable above the heated cable power cut off, and then with the fire cable side-by-side cable power cut off, and finally the fire cable below the cable power cut off.
(3) Close the cable trench fire door or block the ends of the cable trench. When the cable fire in the cable trench, in order to avoid air circulation, in order to facilitate the rapid extinguishing of the fire, the cable trench fire doors should be closed or blocked at both ends, using asphyxiation to extinguish the fire.
(4) do a good job of extinguishing cable fire personal protection. As the cable fire will produce a large amount of smoke and combustion of toxic gases, extinguish the cable fire, extinguishers should wear gas masks. In order to prevent personal electric shock in the process of fighting, fighting personnel should also wear rubber gloves and wear insulated boots, if a phase of high-voltage cables found to be grounded, fighting personnel should comply with: indoor shall not enter the fault from the point of 4m or less, outdoor shall not enter the fault from the point of 8m or less, so as to avoid step voltage and contact voltage injuries. Rescue of injured personnel is not limited to this, but should take protective measures.
(5) fire extinguishing equipment used to fight cable fires. Extinguish cable fire should be used to extinguish fire extinguishing machine, such as dry powder fire extinguisher, “1211” fire extinguisher, carbon dioxide fire extinguisher, etc.; can also use dry sand or loess cover; if the water to extinguish the fire, it is best to use a spray gun; if the fire is fierce, it is impossible to extinguish in other ways, to be cut off after the power supply, you can fill the cable trench with water and use water to seal the fault fire. The fault will be sealed to extinguish the fire.
(6) fighting cable fire, prohibit the use of hands to directly touch the cable steel armor and move the cable.
Fourteen, power cable fire prevention measures
In order to prevent the occurrence of cable fire accidents, the following precautions should be taken:
(1) selection to meet the thermal stability requirements of the cable. Selected cables, under normal circumstances, to meet the long-term rated load heat requirements, in the case of short-circuit, to meet the short-term thermal stability, to avoid overheating cable fire.
(2) Prevent overloading. When the cable is running with load, it generally does not exceed the rated load operation, and if it is overloaded, the overload operation time of the cable should be strictly controlled to avoid overloading and overheating of the cable fire.
(3) comply with the relevant provisions of the cable laying. Cable laying should be as far as possible from the heat source, to avoid parallel or cross arrangement with the steam pipe, if parallel or cross, should maintain the specified distance, and take thermal insulation measures, prohibit the cable parallel laying of the whole line in the hot pipe on the top or bottom; in some pipeline tunnels or ditches, generally avoid laying cables, such as need to be laid, should be taken to insulate the heat measures; overhead laying of cables, in particular, plastic, rubber cables, there should be prevented Heat pipes and other thermal insulation measures; cable laying, cable, cable and heat pipes and other pipelines, cables and roads, railroads, buildings, etc., parallel or cross the distance between the regulations should be met; in addition, the cable laying should be left with a waveform margin, in order to prevent the cable from stopping the operation of the contraction of the contraction of the winter cable to produce excessive tension and damage to the cable insulation. Cable turning should ensure that the minimum radius of curvature to prevent excessive bending and damage to cable insulation; cable tunnel should be avoided in the joints, because the cable joints is the weakest insulation in the cable, the joints are prone to short-circuit failure of the cable, when the tunnel must be installed in the middle of the joints, fire-resistant bulkheads should be used to separate it from the other cables. The above cable laying regulations to prevent overheating of the cable, insulation damage fire are effective.
(4) regular inspection. Power cables should be regular inspection tours, regular measurement of air temperature and cable temperature in the cable trench, in particular, should do a good job of large-capacity power cables and cable connector box temperature records. Timely detection and treatment of defects through inspection.
(5) tightly closed cable holes, holes and fire doors and partition walls. In order to prevent cable fire, must be all through the wall, floor, shaft, cable trench and into the control room, cable mezzanine, control cabinets, instrumentation cabinets, switch cabinets, etc. cable holes for tight closure (closed tight, flat, beautiful, do not damage the cable). Longer cable tunnels and their bifurcation should be set up fire partition walls and fire doors. Under normal circumstances, the cable tunnels or holes on the door should be closed, so that, once the cable fire, you can isolate or limit the scope of combustion to prevent the spread of fire.
(6) stripped non-directly buried cable exterior jute outer layer. Directly buried cable appearance has a layer of soaked in asphalt and other jute protective layer, the direct burial of the cable in the ground has a protective effect, when the direct burial of the cable into the cable trench, tunnel, shaft, the appearance of soaked in asphalt and other jute protective layer should be stripped to reduce the risk of fire expansion. At the same time, the cover above the cable trench should be covered, and the cover is complete, strong, welding slag is not easy to fall into, reducing the possibility of a cable fire.
(7) Keep the cable tunnel clean and properly ventilated. Cable tunnels or trenches should be kept clean, not allowed to pile up garbage and debris, tunnels and trenches of water and oil should be removed in a timely manner; in the case of normal operation, cable tunnels and trenches should be properly ventilated.
(8) Keep the cable tunnel or trench with good lighting. Cable layer, cable tunnels or trench lighting is often kept in good condition, and the need to go up and down the tunnels and trench mouth with a special ladder, in order to facilitate the operation of the inspection and cable fire fighting.
(9) Prevent fire from entering the cable trench. When conducting open-flame operations near the cable, measures should be taken to prevent fire from entering the trench.
(10) Regular maintenance and testing. According to the regulations and cable operation of the actual situation, the cable should be regularly overhauled and tested, in order to deal with defects and find latent faults in a timely manner, to ensure the safe operation of the cable and to avoid the occurrence of cable fires. When entering the cable tunnel or trench for maintenance, test work, should comply with the “electrical safety regulations” of the relevant provisions.
Fifteen, the difference between power cables and control cables
The difference in scope of application
Power cables are used in urban power grids or power stations and other places, while the control cable for industrial and mining enterprises, energy and transportation sectors.
Difference in role
Control cables from the power distribution point of the power system to transmit power directly to a variety of electrical equipment and appliances of the power connection line, and power cables are mainly used in the generation, distribution, transmission, transformation, power supply lines in the transmission of strong electrical energy, through the current is large, power cables are used in the power system backbone for the transmission and distribution of large functions of electrical energy.
Difference in core color
Control cable insulation core color is generally black printed white, and power cables are generally low voltage color.
Difference in implementation standards
Control cable standard is 9330, power cable standard is GB12706. cross-section of the difference between power cables for the primary load wire, the current-carrying capacity with the increase in power and increase, wire application cross-section must be increased with the increase in current and increase, so the specifications of the power cable is generally larger, up to 500 square feet (conventional manufacturers can produce the range), and then the larger cross-section of the general can be done by the manufacturers are relatively few, and the control cable for the secondary command wire, the control cable is generally black printed letters, and power cable low voltage generally split. Control cable for the secondary command wire, controlled by the contactor and other devices running current-carrying, load current is very small, the conductor cross-section is very small, so the cross-section of the control cable is generally smaller, the maximum is generally not more than 10 square.
The difference in cross-section
Power cable for the primary load conductor current-carrying capacity increases with the increase in power, the conductor application cross-section must also be increased with the increase in current and increase, so the specifications of the power cable is generally larger, up to 500 square feet (conventional manufacturers can produce the range), and then larger cross-section of the general can be done by the manufacturers are relatively few, and the control cable for the secondary command conductor
The control cable is the secondary command conductor, the control is the contactor and other devices to carry current operation, load current is very small, the conductor cross-section is very small, so the cross-section of the control cable is generally smaller, the maximum is generally not more than 10 square feet.
The difference between the wire skin
Power cables require that the sheath has sufficient compressive strength, tensile strength, temperature resistance, corrosion resistance. Control cable requirements are relatively low. The same specifications of industrial electrical power cables and control cables in the production of power cables, power cable insulation and jacket thickness than the control cable thick.
The difference between the number of cable cores
Power cable wire core number is less, there are single-core, two-core, 3-core 4-core (three-phase four-wire system), 5-core (three-phase five-wire system), according to the requirements of the power grid up to the general 5-core. Control cables for transmission of control signals, more cores, from 2 to 61 cores, or even more. Control cables also use a variety of core structure, shielding and other measures to obtain satisfactory electromagnetic compatibility.
Difference in rated voltage
The rated voltage of power cables is generally 0.6/1kV and above, control cables are mainly 450/750V.
Sixteen, the difference between power cables and communication cables
Communication cables and power cables are used to transmit signals and energy wires, but in the use of the environment, transmission characteristics, equipment requirements are different.
Power cables are used to transmit high-power current, with high electrical characteristics, widely used in power systems, mines, construction sites and other occasions. Power cables generally use a multi-core design to facilitate the transmission of three-phase current, and the diameter of the conductor, material and other very strict requirements to ensure the transmission effect and safety.
Communication cables
Communication cables are used for data transmission, communication connections, etc. The signals to be transmitted are mainly high-frequency electrical signals. Communication cables use many special designs to meet the requirements of high speed, low BER, good anti-jamming and so on. As communication cables transmit weak signals, they often require an outer shield to minimize interference, and the internal conductor will be a thinner single strand or twisted wire for more sensitive signal transmission.
Structural differences between power cables and communication cables
Power cable adopts four-layer structure such as conductor-insulation layer-armor layer-outer sheath to fully protect personal and equipment safety; while communication cable adopts four-layer structure such as insulation layer-copper foil shielding layer-insulation layer-outer sheath to meet the requirements of high speed rate, low BER, good anti-interference and so on.
Power cables and communication cables have different fields of application
Communication cables are mainly used in data centers, broadcasting, telecommunications, computers, monitoring and many other areas of demand for signal transmission, while power cables are mainly used in the power transmission industry, mines, construction sites and other fields.
Seventeen, the difference between power cables and signal cables
Power cables and signal cables are two main types of cables, the difference between them lies in the nature of the electrical signals they transmit and the transmission distance.
First of all, power cables are mainly used to transmit high voltage and high power electrical energy to supply power equipment and home use. They transmit either AC or DC electrical energy, and their voltage is usually above 1 kilovolt and their current is also very high. The conductors of power cables are usually made of copper or aluminum, and their insulating materials need to have high electrical insulation and high temperature resistance to withstand high voltage and high current operation. In addition, power cables usually require an additional grounding shield to protect against electromagnetic interference and outside noise.
In contrast, signal cables transmit low-voltage, low-power electrical signals and are primarily used to transmit data, voice, video or other low-power electronic signals. The conductor of a signal cable is usually made of copper or silver, and its insulating material needs to have high electrical insulation and low dielectric constant to ensure the speed and quality of signal transmission. The transmission distance of signal cable is relatively short, usually within tens of meters, but some special signal cables can transmit signals for hundreds of meters.
In terms of application, power cables are used in electric power systems, including transmission and substation stations, distribution lines, and power supply for residential and commercial buildings. Signal cables, on the other hand, are mainly used in communication, audio and video equipment, medical equipment, automotive electronics and industrial automation. They are characterized by fast transmission speed, stable signal quality and strong anti-interference ability.
In general, power cables and signal cables have different designs and applications in terms of conductor materials, insulation materials, voltage, current, transmission distance, additional shielding, etc. These differences are to meet their different transmission needs and environmental requirements. In practice, it is very important to choose the right type of cable to ensure the quality and safety of power and signal transmission.
Eighteen, the application of new power cable technology
- Superconducting cable technology:
Superconducting cables utilize the characteristics of superconducting materials to transmit power at extremely low temperatures, with the advantages of low loss and high transmission efficiency. This technology has great potential in large-capacity power transmission and urban underground cable wiring, which can improve the stability and efficiency of the power grid.
2.Intelligent cable technology:
Combined with the Internet of Things and artificial intelligence technology, smart cable can realize real-time monitoring and remote management of cable operation status, temperature, humidity and other parameters. Through data analysis and prediction algorithms, hidden faults can be found in time and preventive maintenance can be carried out to improve the reliability and safety of the power grid.
- Environmentally friendly cable materials:
With the increased awareness of environmental protection, the research and development and application of green cable materials are increasingly being emphasized. For example, renewable materials, low-halogen materials, etc., can not only reduce the pollution of the environment, but also help reduce cable manufacturing costs and energy consumption.
- Flexible cable technology:
With the rapid development of electric vehicles, smart homes and other fields, the demand for flexible cables is increasing. Flexible cables are resistant to bending, easy to install, suitable for complex environments and narrow space wiring needs, the future of new energy vehicle charging facilities, smart home systems and other aspects will be widely used.
Nineteen, the future development trend of power cables
- Intelligent and digital:
Power cables will be more intelligent and digital, to achieve remote monitoring of the grid, fault diagnosis and intelligent management, to improve the grid’s response speed and operational efficiency.
- High-performance materials:
Future cable materials will pay more attention to high temperature, abrasion resistance, corrosion resistance and other properties to adapt to complex environments and high load operation requirements.
- High-density cabling technology:
With the acceleration of urbanization and the increase in building density, the future cable wiring will pay more attention to high-density, low-space occupancy design to improve the overall layout of the grid efficiency and flexibility.
4.Sustainable development:
The future of the power cable industry will pay more attention to sustainable development, promote the development and application of green low-smoke halogen-free flame retardant cable materials, reduce resource consumption and environmental pollution.
Power cable industry is in a stage of rapid development and transformation, the continuous emergence of new technologies and future development trends will be clear for the safe and stable operation of the power system and sustainable development of energy to provide important support.
TST Cables, the world’s leading power cable manufacturer
Power Wire Manufacturer TSTCables , high-quality materials, exquisite craftsmanship, for your power system, safe and stable power transmission preferred, excellent conductivity and strong insulation protection, to ensure efficient and stable transmission of electricity. Whether it’s for household electricity, industrial power supply or large-scale infrastructure construction, our power cables can meet all your needs. If you have any needs or questions about power cables, please feel free to contact us by email~
Also available in:
English