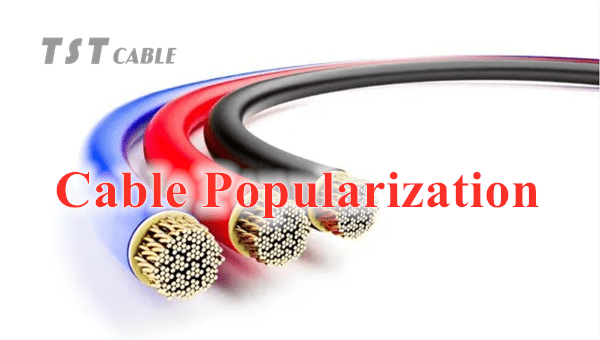
First, the main steps of the production process of Teflon high temperature wire:
Preparation of raw materials: first of all, you need to prepare Teflon resin, filler, stabilizer and other raw materials. These materials need to be accurately weighed and dosed to ensure that the proportion of materials in each batch of production is accurate.
Mixing: Put the dosed raw materials into the mixing machine for mixing and blending. The purpose of this step is to make the various raw materials fully mixed to ensure that the quality of the finished product is uniform and stable.
Extrusion: The mixed material is fed into the extruder, which heats it to a molten state and then extrudes it through the die. The pressure, temperature and speed of the extruder need to be adjusted according to the specific requirements of the product to ensure that the appearance and size of the Teflon wires meet the standards.
Drawing: After extrusion molding, Teflon wires need to be drawn. This step is to improve the strength and insulation properties of the wire. Through drawing, the cross-sectional area of the wire is reduced, the wire diameter is finer, and the tensile strength of the wire is also increased.
Insulation treatment: After drawing, Teflon wires need to be insulated to protect the conductors of the wire from electrical contact with the outside environment. Commonly used insulating materials include polyethylene and polyvinyl chloride, etc. Insulation treatment is carried out through the dip-coating method or wrapping method to ensure the uniformity and sealing of the insulation layer.
Heat Treatment: After the insulation treatment is completed, Teflon wires also need to be heat treated. This step is to improve the wire’s high-temperature resistance by heating it to a certain temperature and keeping it there for a certain period of time to make the internal structure of the wire more stable.
Printing marking: After heat treatment, Teflon wires will be printed with marking, including the model, specification, manufacturer and other information of the wires, which is convenient for users to recognize and distinguish between different specifications and models of wires.
Stripping: After the printing of the logo is completed, it needs to be stripped to expose the conductor of the wire to facilitate wiring and connection. Stripping can be done by mechanical or chemical stripping to ensure that the conductor is exposed without damaging the conductor.
Winding: After the stripping process is complete, the Teflon wire is wound into coils or reels for ease of carrying and use.
Inspection: The last step is to conduct a strict inspection of Teflon wire to ensure that its quality meets the standards.
Second, the molding method of Teflon high temperature wire cable:
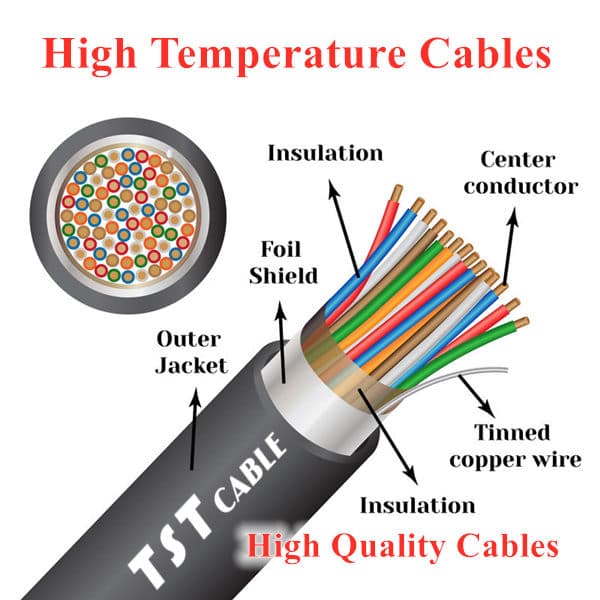
- Molding method: In this method, Teflon material is put into the mold and pressed under high temperature and pressure to form the desired shape. This method is suitable for the manufacture of cable components with complex shapes or where precise dimensions are required.
- Pushing method: Teflon material is pushed into a mold of a specific shape by using pressure to form it. This method is suitable for manufacturing long or tubular products.
- Skin bladder method: In this method, an expandable skin bladder (or similar flexible container) is used to wrap the Teflon material and pressurize it to fit the shape of the mold. The bladder method is suitable for manufacturing complex shapes and keeps the inside of the product smooth.
- Spraying method: Teflon coating is sprayed onto the surface of the cable to form a protective layer. This method is mainly used to enhance the insulation and corrosion resistance of cables.
- Braiding method: Teflon fibers are used to braid around the core of the cable to form a protective layer. This method enhances the mechanical strength and abrasion resistance of the cable.
- Winding method: Teflon tape or wire is wound around the core of the cable to form one or more protective layers. This method is simple and easy to use and is suitable for mass production.
- Rolling method: Teflon material is pressed by rollers to make it close to the cable core. This method can improve production efficiency and product quality.
- Extrusion method: the Teflon material is extruded into the required shape through an extruder and then wrapped around the cable core. This is a common method for manufacturing Teflon high-temperature wire cables with high efficiency and low cost.
- Bonding method: Teflon materials are bonded together with other materials using adhesives to form a composite structure of the cable. This method is suitable for cables that require multi-layer structures or combinations of different materials.
- Welding method: In some specific cases, welding techniques can be used to join Teflon materials with other components. This method requires high-precision operating techniques and is usually used in the manufacture of cables with special requirements.
- Heat-setting method: During the manufacturing process, the Teflon material is heated and kept in a certain shape, and then cooled and shaped. This method can improve the shape stability and mechanical strength of the cable.
- Machining method: For Teflon high temperature wire cable that has been molded, it can be further processed using machining methods (such as cutting, grinding, etc.) to meet specific size and shape requirements.
- Hot extrusion process method: when the temperature of the barrel inside the extruder reaches 350℃~390℃, F46 polyphenylene sulfide is added to the bin, and using the thrust of the screw rotation, it is evenly and continuously covered on the conductive wire core through the molding die, and then shaped after refrigeration.
- Upward push process method: the powdered PTFE plastic pre-stress tensioned into a cylinder, into the barrel, using the piston rod thrust, through the molding die uniformly and continuously covered in the conductive wire core, and then 380 ℃ high temperature calcination, after refrigeration and shaping.
- Wrap-around process method: use the PTFE plastic film tape cut into a certain pitch to wrap around the core of the wire, and then calcinated and shaped.
Teflon high temperature wire cable molding method is very much, different industries, equipment, environmental requirements of different ways used:
Teflon high temperature wire manufacturers TST CABLES reminds enterprises that it should be noted that not all of the above methods are applicable to all types of Teflon high temperature wire cable manufacturing, the specific choice of which method depends on the specific requirements of the product and the complexity of the manufacturing process. At the same time, different molding methods may require different equipment and process parameters, so careful selection and adjustment is required in actual operation. In addition, although Teflon materials have excellent high-temperature resistance, care should be taken to control the temperature and time during the manufacturing process to avoid damage to the material properties or safety accidents. Meanwhile, for molding methods involving adhesives, welding and other process steps, attention also needs to be paid to material selection and compatibility to ensure the quality and performance of the final product.
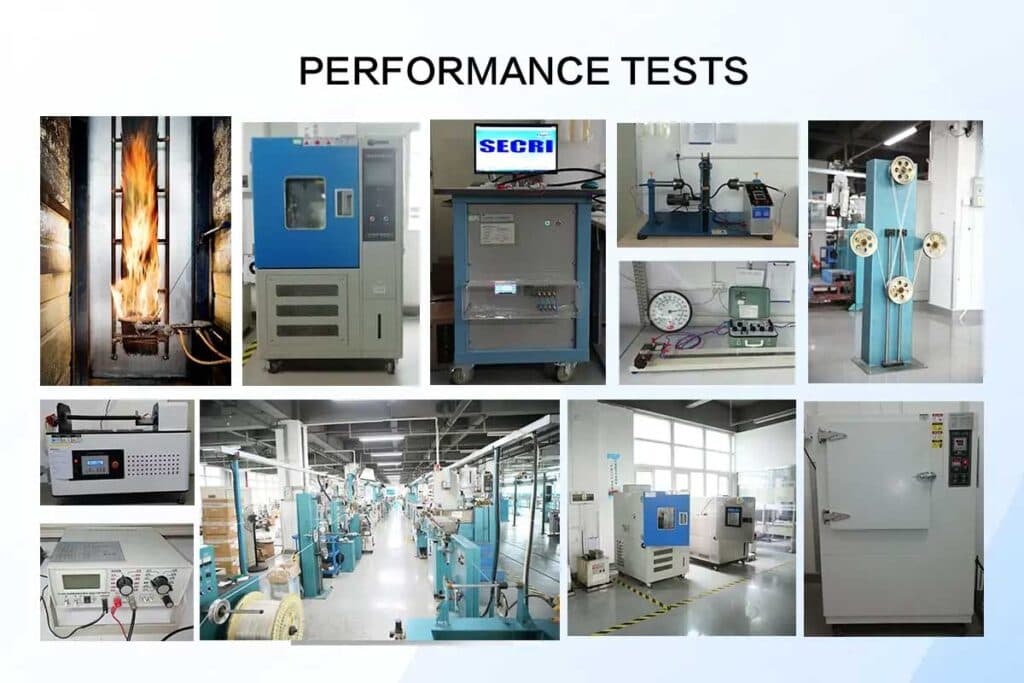
TST CABLES
The above is TST CABLES for Teflon high-temperature wire production process and molding methods of the summary, I hope that after reading can help you. TST CABLES is a focus on high-temperature wire (silicone, Teflon, PEEK) special cables and other products, engaged in the field of the cable industry has been more than 20 years of practical experience in the production of high-temperature cable production, processing, sales as a whole, has a more advanced global production technology and experience in the production of high-temperature cables. More global advanced production technology and experienced team of engineers, products have a high reputation in the industry. Can be customized according to the special needs of different customers, a variety of special high-temperature cables, welcome to consult the purchase and related questions and answers about cable products.
TST CABLES–Specializing in high temperature resistant cable applications and solutions
Fluoroplastic Cables|Polyimide (PI) Cables|Polyetheretherketone (PEEK) Cables|Silicone Rubber Cables
Rail way | Aviation | Marine | Nuclear | Oil & Gas | Wind Power industry applications
For more information on Teflon high temperature wire, waterproof Cables,Silicone Cables,low-smoke, halogen-free, flame-retardant, high-temperature-resistant cables or to customize cables for your machinery or system, visit https://www.tstcables.com/product/
or send an e-mail to:lixiangchao@testeck.com
Also available in:
English