Introduction of submarine cable
Submarine cable is a cable wrapped with insulating material and laid on the seabed for telecommunication transmission. Submarine cables are divided into submarine communication cables and submarine power cables. Modern submarine cable is the use of optical fiber as a material, the transmission of telephone and Internet signals. 1850, people in Calais (France) and Dover (England) between the world’s first submarine cable, in August 1858 by Cyrus West Field founded a private British company in Ireland (Europe) and Newfoundland (North America) between the completion of the first intercontinental submarine communications cable. Cable. The first submarine cable in China was completed in 1888. There were two cables, one between Chuanshidao in Fuzhou and Huwei (Danshui) in Taiwan, 177 nautical miles long, and the other from Anping in Tainan to Penghu, 53 nautical miles long.
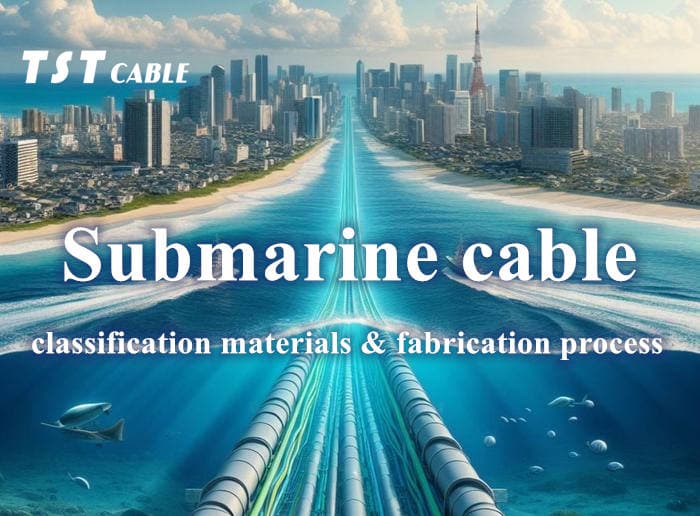
Submarine cable is divided into submarine communication cable and submarine power cable. Submarine communication cable is mainly used for communication business, expensive, but high degree of confidentiality. Submarine power cables are mainly used for underwater transmission of high-power electrical energy, and the role of underground power cables are the same, only the application of the occasion and the laying of different ways. As the submarine cable project is recognized by the world as a complex and difficult large-scale projects, from environmental detection, marine physical investigation, as well as cable design, manufacturing and installation, are the application of complex technologies, and thus the submarine cable manufacturers in the world for the few, mainly Norway, Denmark, Japan, Canada, the United States, Britain, France, Italy and other countries, these countries in addition to manufacturing also provide laying technology.
At present, 220kv photoelectric composite submarine cable to break the foreign monopoly pattern, began to not need to rely entirely on imports. 2015, the first 220kv (currently the highest level of global submarine cable voltage) cables began to ship, means that China is also able to research and development of high-voltage cables, no longer rely on foreign imports.
Submarine cable production materials
The core of a submarine cable is made of high-purity optical fiber as fine as a hair, which guides light along the path of the fiber through internal reflection. Submarine cables must be able to withstand the enormous pressure of 8 kilometers underwater, equivalent to the weight of an elephant on a human thumb, NEC’s deep-sea cables are made of lightweight polyethylene, and the entire cable is only 17 millimeters thick.
Submarine Cable Fabrication Process
In the making of submarine cables, optical fibers are first embedded in a jelly-like compound that protects the cable from damage even when it comes into contact with seawater. The fiber optic cable is then packed into a steel tube to prevent the pressure of the water from damaging it. Next, it is wrapped in steel wire, which is extremely strong overall, and sleeved in copper tubing, which is finally covered with a protective layer of polyethylene material. Near the coast of the continental shelf, submarine cables are often laid using lightweight cables with stronger steel wires and covered with a bituminous coating to protect them from seawater corrosion.
Submarine cable applications
Submarine communication cables are mainly used for long-distance communication networks, usually used for long-distance between islands, cross-sea military facilities and other important occasions. Submarine power cable laying distance compared to communication cable is much shorter, mainly used between land islands, across rivers or harbors, from the land to connect drilling platforms or drilling platforms connected to each other. In general, the application of submarine cables to transmit electricity is undoubtedly more expensive than the same length of overhead cables, but it is often more economical than using small and isolated power stations for regional power generation, the application of more benefits in offshore areas. In countries with many islands and rivers, such cables are more widely used.
Submarine ship cable product classification
1. Impregnated paper wrapped cable
Applicable to the lines of not more than 45kV AC and not more than 400kV DC. At present, it is only installed in the water depth of 500m or less.
2.Self-capacitating oil-filled cable
Suitable for up to 750kV DC or AC power lines. As the cable is oil-filled, so it can be laid in the water depth of up to 500m of the sea without difficulty.
3. Extruded insulation (cross-linked polyethylene insulation, ethylene propylene rubber insulation) cable
Suitable for AC voltage up to 200kV. Ethylene Propylene Rubber is better than polyethylene to prevent dendritic phenomenon and local leakage, so that the submarine cable can function more effectively.
4. “Hydraulic” Tube Cables
Suitable for kilometer-long cable systems because of the mechanical constraints of pulling extremely long cables into the pipe.
5. Inflatable (pressure-assisted) cables
The use of impregnated paper packets of inflatable cables than oil-filled cables are more suitable for longer submarine cable network, but due to the need to operate in deep water using high air pressure, so increasing the design of the cable and its accessories, generally limited to the water depth of 300m or less.
6. Marine engineering – low smoke halogen-free marine armored cable
Suitable for all kinds of river and sea vessels, offshore oil platforms and offshore buildings with low-smoke halogen-free flame-retardant characteristics requirements of power, lighting and general control devices, rated voltage 0.6/1KV and below in the transmission and distribution lines.
With the world’s vigorous exploitation of marine resources, further development of marine engineering equipment has become one of the Made in China 2025 project. The rapid development of marine engineering, with the matching special cable demand is also increasing, at the same time on the performance of TSTCABLES also put forward higher requirements, such as various types of drilling equipment, oil platforms, submarine cables, marine armored cables, such as power, control and instrumentation cables used in the project, its significant technical characteristics are high mechanical strength, oil resistance, mud, weathering and UV resistance, high temperature resistance, low temperature resistance, low smoke and non-halogen, bundle burning/fire performance. If you have needs or questions about offshore cables, please feel free to contact us at TSTCABLES.
Also available in:
English