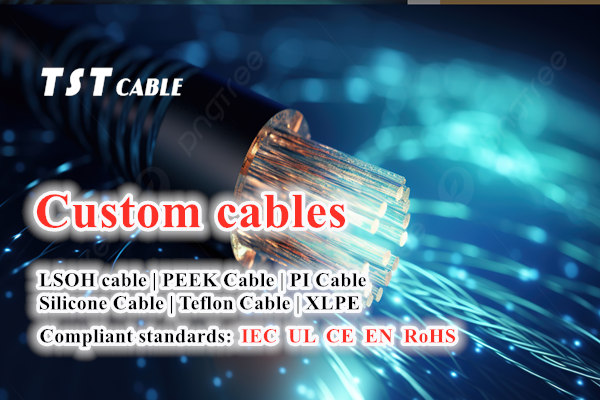
Heat-resistant flexible cables are cables specially designed to work in high-temperature environments. They are highly flexible and durable and are suitable for applications that require frequent bending and movement. This type of cable is used in multiple industries, such as aerospace, automotive manufacturing, chemicals, energy, metallurgy, and various industrial automation systems.
The following are some key features and design elements of heat-resistant flexible cables:
Heat-resistant flexible cable insulation materials
High-temperature resistant insulation materials: This type of cable uses materials that can maintain insulation properties under high temperature conditions. Common ones include silicone rubber cables, fluoroplastic cables (such as PTFE), polyimide cables (PI), polyetheretherketone cables (PEEK), etc. These materials have good chemical stability, electrical properties and mechanical strength.
Flame retardant properties of heat-resistant flexible cables
Flame retardant and low smoke halogen-free: In order to improve safety performance, heat-resistant flexible cables usually have flame retardant properties, which can slow down the spread of fire even in fire, and release less smoke and toxic gases when burning, which is conducive to personnel evacuation and reducing property losses.
Heat-resistant flexible cable conductor materials
High-quality conductors: Metals with good electrical conductivity such as copper or tinned copper are used as conductors to ensure efficient and stable current transmission. In some cases, special alloy conductors may also be used to enhance heat resistance and corrosion resistance.
Heat-resistant flexible cable sheath materials
High-temperature and wear-resistant sheaths: The outer sheath material also needs to have high-temperature resistance, and should also be wear-resistant, chemical-resistant and oil-resistant to protect the internal structure from the external environment. Commonly used materials include modified polyamide, polyurethane (PU), etc.
Heat-resistant flexible cable design and structure
Reinforced structure: In order to improve the mechanical strength and service life of the cable, steel wire ropes, fiber braids or armor layers may be added to the cable to enhance its ability to resist stretching and extrusion.
Shielding: For applications that require protection from electromagnetic interference (EMI) or radio frequency interference (RFI), the cable will contain a shielding layer, usually a metal braid or metal foil.
Performance characteristics of heat-resistant flexible cables
High flexibility: The cable design allows use in tight spaces or environments with frequent bending without compromising its electrical performance or physical integrity.
High operating temperature: It can withstand temperatures ranging from 100°C to 250°C or even higher, depending on the selected material.
Long life: It has a long service life even under harsh working conditions.
Application areas of heat-resistant flexible cables
Industrial automation: robot arms, servo motor connections, sensor lines, etc.
Transportation: internal wiring of airplanes, trains, and ships.
Energy industry: high-temperature environments such as wind power plants, oil and gas drilling platforms, and nuclear reactors.
Construction industry: wiring of safety and fire protection systems in high-rise buildings and subway tunnels.
Working temperature range of heat-resistant flexible cable
The working temperature range of heat-resistant flexible cable varies depending on the material, but it can generally be divided into the following grades:
Standard grade: The working temperature range of general cables such as PVC-insulated cables is between -20°C and +70°C.
High temperature grade: Cables using materials such as silicone rubber, fluoroplastics (such as PTFE, FEP, PFA), polyimide (PI), polyetheretherketone (PEEK), etc. can have an operating temperature range from -50°C to +180°C or higher, such as some silicone rubber cables can reach +200°C to +250°C.
Ultra-high temperature grade: Some special cables, such as cables using composite materials such as mica tape and ceramic fiber, can work for a short time at extreme temperatures of +600°C to +1000°C.
Bending radius of heat-resistant flexible cable
The design of heat-resistant flexible cables focuses on bending performance to adapt to occasions with frequent bending. The bending radius usually follows the following principles:
Minimum bending radius: Cable manufacturers will give a minimum bending radius value, which is usually a certain multiple of the cable outer diameter (OD), such as 5 times, 6 times or 10 times OD. This ensures that the cable will not damage the internal conductor and insulation layer when bending.
Electrical performance of heat-resistant flexible cable
Electrical performance is an important indicator of cable quality, including:
Resistance: At a given temperature, the resistance of the cable should meet the relevant standards.
Insulation resistance: Indicates the resistance value of the insulation material of the cable under normal operating voltage, which should be high enough to avoid leakage.
Capacitance: The capacitance value of the cable per unit length affects the signal transmission quality and power loss.
Shielding efficiency: For cables with a shielding layer, its ability to suppress electromagnetic interference (EMI) and radio frequency interference (RFI) is a key parameter.
Flame retardant grade of heat-resistant flexible cable
The flame retardant grade reflects the performance of the cable in the event of a fire, which is mainly divided into the following categories:
Flame retardant class A: The cable can extinguish itself after the flame is removed, and produces less smoke and toxic gases.
Flame retardant class B: Similar to class A, but produces slightly higher amounts of smoke and toxicity when burning.
Halogen-free flame retardant: The cable does not produce harmful gases such as hydrogen halides when burning, and is particularly suitable for densely populated areas.
Fire-resistant cable: Even in a fire, the cable can maintain the integrity of the circuit for a specified time, and is suitable for emergency power supply and fire protection systems.
Testing and certification of heat-resistant flexible cables
Heat-resistant flexible cables are subject to strict quality control and testing during the production process to ensure that their performance meets international standards and industry specifications. Common test items include:
Temperature resistance test: Verify the insulation performance and overall structural stability of the cable under specified high temperature conditions.
Bending test: Evaluate the durability and electrical continuity of the cable under repeated bending conditions.
Flame retardant test: Check the burning behavior of the cable under the action of a fire source to ensure that it meets the requirements of flame retardancy and low smoke halogen-free.
Electrical performance test: Measure the resistance, capacitance, inductance and other parameters of the cable to ensure that it meets specific electrical performance indicators.
Mechanical performance test: Including tensile strength, bending radius, abrasion resistance, etc., to ensure the mechanical durability of the cable in actual applications.
Heat-resistant flexible cable installation and maintenance
Proper installation and regular maintenance are the key to ensure the long-term reliable operation of heat-resistant flexible cables. During installation, follow the manufacturer’s instructions and be careful to avoid excessive bending or twisting of the cable to prevent damage to the internal structure. During maintenance, regularly check the appearance and connection points of the cable to promptly detect and deal with any potential wear or damage to extend the service life of the cable.
Emerging technologies and development trends of heat-resistant flexible cables
With the advancement of technology, heat-resistant flexible cables are also constantly innovating to adapt to more complex and changing application scenarios. For example, smart cables integrate sensors that can monitor the temperature, stress and other status information of the cable in real time to achieve remote monitoring and predictive maintenance. In addition, the application trend of environmentally friendly materials is becoming more and more obvious, and low-smoke, halogen-free, and recyclable cable materials have been developed to reduce the impact on the environment.
Cooperate with cable manufacturer TST cables to customize high-quality heat-resistant flexible cables
Leading industry innovation, TST CABLES focuses on high-performance heat-resistant flexible cable solutions. When your device is surrounded by high temperatures and is as hot as an oven, ordinary cables have long retreated, while TST CABLES’s heat-resistant flexible cables remain as calm as ever and continue to complete the impossible task! TST CABLES heat-resistant flexible cables play an indispensable role in many industries with their excellent heat resistance, flexibility and durability. With the continuous innovation of TST CABLES technology, heat-resistant flexible cables will be more efficient, safe and environmentally friendly in the future, providing more reliable support for modern industry and infrastructure.
TST CABLES reminds users that when purchasing and using heat-resistant flexible cables of different materials, you should fully consider the application requirements, select the appropriate product specifications, and follow the correct installation and maintenance guidelines to ensure the long-term stable operation of the cables.
If your industry has needs or questions for high-quality customized heat-resistant flexible cables (silicone rubber/PTFE/PI/PEEK heat-resistant flexible cables), please feel free to contact us by email at any time, and you can also get free samples.
Also available in:
English