Fire-resistant power cables are cables specially designed to maintain normal operation for a certain period of time under fire conditions. Such cables can continue to work under high-temperature flame conditions to ensure that the functions of key circuits (such as fire protection systems, emergency lighting, alarm systems, etc.) are not interrupted, and buy valuable time for personnel evacuation and fire fighting operations. The following is some important information about fire-resistant power cables summarized by TST cable.
Characteristics of Fire-Resistant Power Cables
- Fire resistance:
Fire-resistant cables are able to maintain circuit continuity in a flame environment. According to different standards, fire resistance tests usually require cables to continue to supply power for a period of time (ranging from 30 minutes to several hours) at a specific temperature (such as 750°C to 950°C or higher). - Low Smoke Zero Halogen (LSZH) Features:
Many fire-resistant cables are made of low-smoke zero-halogen materials, which means that the amount of smoke produced during combustion is small and does not contain corrosive and toxic gases, which is conducive to the safe evacuation of personnel and reduces damage to equipment. - Mechanical strength and flexibility:
Despite their excellent fire resistance, these cables still need to have sufficient mechanical strength to withstand the tensile stress during installation and be flexible enough to be laid. - Stable electrical performance:
In addition to fire resistance, they also need to ensure good electrical insulation performance and not degrade due to environmental changes during long-term use.
Fire-resistant power cable materials and structures
Conductor: High-purity copper or silver-plated copper is generally used as the conductor material to improve conductivity and high temperature resistance.
Insulation layer: Mica tape or other high-temperature resistant insulating materials may be used to wrap the conductor.
Sheath material: Commonly used sheath materials include ceramic silicone rubber, mineral insulation materials, etc., which can form a protective shell at high temperatures to prevent further flame invasion.
Reinforcement layer: Some designs will add glass fiber braid or other forms of reinforcement layer to improve the overall structural strength.
Fire-resistant power cable standards and certification
Different countries and regions have different standards and certification requirements for fire-resistant cables. Common international standards include but are not limited to:
IEC 60331: specifies the test methods and performance requirements for fire-resistant cables under flame conditions.
BS 6387: British standard, which proposes more stringent classification levels for fire-resistant cables, including simple fire resistance (Class C), fire resistance plus water spray (Class W), and fire resistance plus mechanical impact (Class Z).
GB/T 19216: Chinese national standard, which defines the technical conditions and test procedures for fire-resistant cables.
Application areas of fire-resistant power cables
Public buildings: emergency escape indicator lights, fire pump power cords, etc. in places such as shopping malls, theaters, and hospitals.
Transportation hubs: emergency lighting and communication lines in subway stations, railway stations, airports, etc.
Industrial facilities: safety monitoring systems and automatic control systems in hazardous areas such as chemical plants and refineries.
Residential buildings: an indispensable part of high-rise buildings to protect the lives and property of residents.
Design details of fire-resistant power cables
- Multi-layer protection structure: Fire-resistant cables usually use multi-layer protection structure to enhance their stability under fire conditions. In addition to the internal conductor and insulation layer, one or more layers of mica tape or other high-temperature resistant materials may be included as an additional fire barrier.
- Ceramic polymer: Some advanced fire-resistant cables use ceramic polymer as the sheath material. This material undergoes chemical changes when exposed to high temperatures, forming a hard ceramic-like protective layer that effectively blocks flame invasion and maintains circuit continuity.
- Metal shielding layer: In some cases, a metal shielding layer may be added to fire-resistant cables to improve electromagnetic compatibility and mechanical strength. This helps reduce the impact of external electromagnetic interference on signal transmission and increases the overall durability of the cable.
- Waterproof and moisture-proof design: Although the main focus is on fire resistance, many fire-resistant cables also take into account the need for waterproofing and moisture-proofing, especially cables used underground or in humid environments. These cables usually have additional waterproof layers or use special sealing technology.
Precautions for installing fire-resistant power cables
- Follow the manufacturer’s guidelines:
During the installation process, the installation guidelines provided by the manufacturer should be strictly followed to ensure that the cables are not damaged by improper operation. For example, avoid excessive bending or stretching of the cables to avoid damaging the internal structure. - Correctly select the path:
A suitable laying path should be selected to avoid potential heat sources and other dangerous areas. At the same time, considering the need for safe evacuation in the event of a fire, try to keep the cables away from crowded passages. - Proper support and fixation:
Use appropriate brackets and clamps to support and fix the cables to prevent them from sagging due to gravity or being damaged by external impact. - Joint processing:
For places where connections are required, specially designed fire-resistant joint boxes or other reliable connection methods should be used to ensure that the joints also have good fire resistance.
Maintenance and management of fire-resistant power cables
- Regular inspection:
Even fire-resistant cables need to be inspected regularly, especially those exposed to the outside or areas that are often at risk of physical damage. The inspection content includes whether the appearance is damaged and whether the joints are firm. - Cleaning and maintenance: Keep the cable surface clean and tidy to avoid dust accumulation that affects the heat dissipation effect. For cables installed outdoors or in harsh environments, special attention should be paid to anti-corrosion measures.
- Recording and tracking: Establish a detailed maintenance file to record the results of each inspection and any maintenance activities. This is very important for tracking the status trend of the cable and can help to detect potential problems in time.
- Emergency preparedness: Develop an emergency plan to take quick action in emergencies such as fires, such as cutting off power or starting backup systems to minimize losses.
Selecting the right fire-resistant power cable is essential to ensure the safety of life and property in a building. In actual applications, products that meet the corresponding fire resistance rating should be selected according to specific needs and local regulations, and regular inspections and maintenance should be paid attention to ensure that they are always in good condition.
Through the above in-depth design considerations, correct installation methods and effective maintenance strategies, the advantages of fire-resistant power cables can be maximized to ensure the continuous operation of critical systems, thereby protecting personnel safety and property from damage. Whether in new projects or renovation and upgrading of existing facilities, the rational selection and proper management of fire-resistant cables are crucial links. If you need fire resistant cables, welcome to send email to TST cable and you can get free samples.
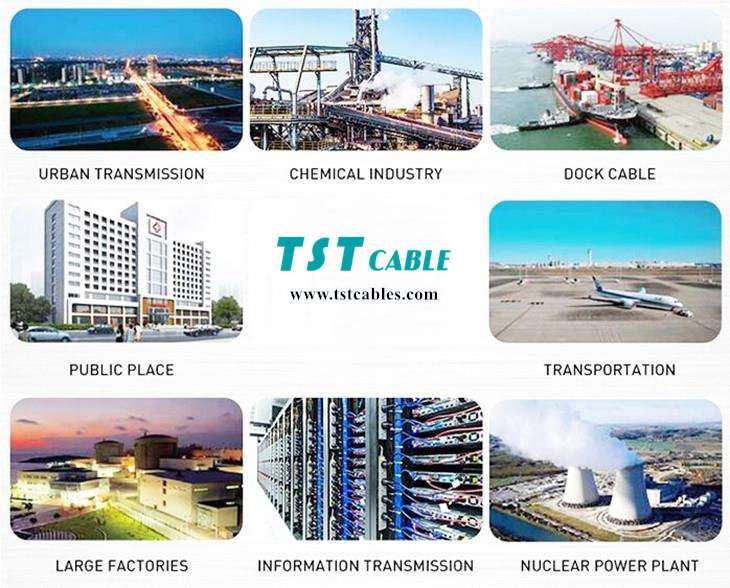
Also available in:
English