Wires and cables are a large category of electrical products used to transmit electricity, transmit information and realize electromagnetic energy conversion. If a large number of unqualified products are found during the spot check, these inferior products will bury many safety hazards for the normal operation of the power system. The unqualified quality of wires and cables may be caused by a variety of factors, which not only affect their performance and life, but may also lead to safety accidents. Cable supplier TST CABLES analyzes some common reasons for unqualified wires and cables and corresponding precautions for everyone:
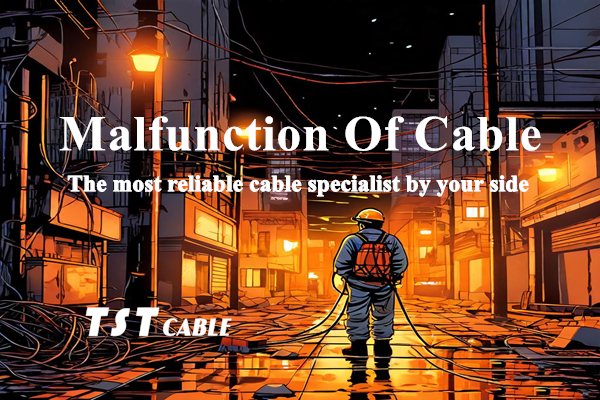
Reasons for unqualified
1. Material quality problems:
Impure conductor material: Low-quality or doped copper, aluminum and other conductor materials are used, resulting in poor conductivity and increased resistance.
Poor insulation layer material: The use of non-standard plastics or rubber as insulating materials reduces the temperature resistance and mechanical strength.
2. Production process defects:
Dimension deviation: Key dimensions such as cable diameter and conductor cross-sectional area do not meet national standard requirements, affecting current carrying capacity and safety.
Poor twisting: Multiple strands of wires are loosely or unevenly twisted, which can easily cause local overheating or breakage.
Missing or insufficient shielding layer: For cables that need to be shielded, if the shielding layer is defective, it cannot effectively resist electromagnetic interference (EMI).
3. Poor environmental adaptability:
Insufficient weather resistance: Cables used outdoors fail to pass tests such as UV protection, waterproofing and moisture resistance, and are prone to aging and cracking.
Weak resistance to chemical corrosion: Cables used in environments with acids, alkalis or other corrosive substances will be quickly damaged if they do not have the corresponding corrosion resistance.
4. Unclear or incorrect identification:
Inconsistent label information: Important information such as product model, specifications, and manufacturer are incorrectly or unclearly marked, misleading users.
Forged certification marks: Some counterfeit and shoddy products even forge international certification marks such as CE and UL to deceive consumers.
5. Improper packaging and transportation:
Physical damage: Due to insufficient packaging or rough handling, the cable surface is scratched and the sheath is damaged.
Poor storage conditions: Long-term exposure to high temperature, humidity or direct sunlight accelerates the aging process of the cable.
Notes
Choose formal channels for purchase: give priority to well-known brands and suppliers with good reputation, and avoid purchasing unlicensed, uncertified, and unsaleable products from small workshops.
Check product certification: ensure that the purchased cables have the necessary quality certifications, such as ISO 9001, CCC, EN, UL, CE, RoHS, etc., and verify the authenticity of the certificates.
Carefully check the appearance: carefully observe whether the cable sheath has obvious defects, such as cracks, bubbles, uneven colors, etc. when receiving the goods; at the same time, measure whether the actual size meets the regulations.
Request a test report: require a product inspection report issued by a third-party authority, especially for cables involving special applications (such as fire and waterproof grades).
Pay attention to the production date: try to choose cables produced recently to reduce the risk of performance degradation due to long storage time.
Follow the installation guide: strictly follow the installation instructions provided by the manufacturer to ensure that the wiring path is planned reasonably, the joints are properly handled, and the grounding protection is in place.
Regular maintenance inspection: even if you choose a high-quality cable, you should inspect it regularly during use to detect and solve potential problems in a timely manner.
Things users should pay attention to when purchasing wires and cables
First, observe the appearance of the wires. The insulation (sheath) layer of qualified products is soft, tough, and stretchable, and the surface is tight, smooth, and has no roughness. If the plastic wrapping the wire is easy to peel off, there is a problem of insufficient plastic strength.
Second, observe the cross-section of the wire. The copper core surface of qualified products should have a metallic luster, and the blackened copper surface indicates that it has been oxidized.
Finally, pay attention to the quality certificate when purchasing wires. If the wire quality is qualified, then the quality of the wire should also be inspected and there will not be too many problems.
In order to improve the safety of the circuits in your home, TST CABLES recommends that you use low-smoke halogen-free flame-retardant cables as home wires. High-purity oxygen-free copper is always used as the core to prevent overload, and environmentally friendly materials are used as insulation, which greatly reduces the risk of leakage short circuit. Using it as a ground wire brings multiple protection to your family. Only cables that meet national standards can truly protect our lives. Don’t be lucky. Once an accident happens, it will be too late to regret it!
In order to ensure the safe and reliable operation of wires and cables, we must start from the source, strictly control the quality of products and the reputation of suppliers when purchasing. At the same time, correct installation and maintenance are also key links to extend the service life of cables and ensure the stability of electrical systems. If you have questions about a specific brand or model of cable, it is recommended to consult TST CABLES professionals for more information and apply for free samples.