The development of rail transportation benefits people’s livelihood, and power cables as the artery of rail vehicle operation, playing the role of “power source”. Railway cable is mainly used in motor, transformer, converter, inverter and other parts.
In order to meet the locomotive safe and fast operation, the quality and efficiency of its power cables must also be guaranteed. The cables used are required to be low smoke-free (low) halogen, flame retardant, fire-resistant, oil-resistant, UV-resistant, moisture-resistant, waterproof, mildew-proof, rodent-proof, etc., and the southern region also requires anti-termite.
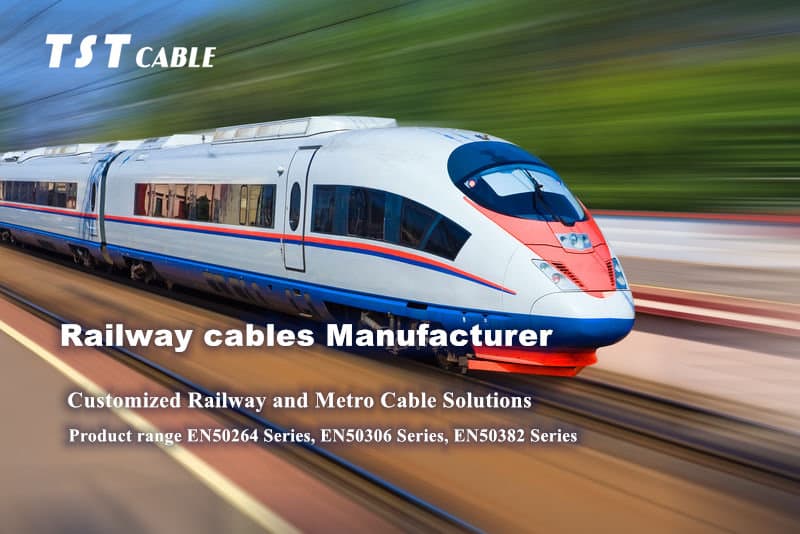
1.The executive standard of power cable for railroad locomotive
1.GB/T12528-2008
Rated voltage, does not meet the current technical requirements of the railroad, the new model is no longer used.
2.TJ/CL 254 Technical Conditions for Passenger Vehicles (Certification )
Based on TB/T184, promote the use of EN50264 and EN50306 European standard, and rated voltage, structural dimensions, technical requirements and test methods are all in accordance with the European standard, the product model using the European standard model, product performance can not be achieved in the use of TJ/CL 254 model.
3.TJ/CL 313 Provisional technical conditions for locomotives (certification)
EU standards EN50382, EN50264, EN5036 prevail, increased high-temperature power cable EN50382, Japanese product models and data cables.
4. Iron standard series TB/T1484.1-2017
Difference with the European standard series:
1. TB/T1484.1-2017 test requirements are based on the test requirements of the European standard;
2. The rated voltage of the iron standard is unified according to the rated voltage of the European standard, i.e. :300V, 600V, 1800V, 3600V;
3. There is no high-temperature power cable products in the iron standard, and there is EN50382 high-temperature ( 120C or 150°C ) silicone rubber power cable ( for traction system ) in the European standard.
2. Locomotive power cable main performance test items
1. Conductor resistance. Ensure that the normal load capacity and overload load capacity.
2. High voltage test. Ensure that the normal work in the use of shock voltage.
3. Dielectric strength. The ultimate strength of the cable to withstand electricity, (maximum voltage at breakdown).
4. Insulation resistance. The intrinsic electrical characteristics of the insulating material in the cable.
5. DC stability. Cable in the high humidity and heat conditions of the work of the stable state.
6. Surface leakage current discharge. High voltage, the cable surface resistance to corona creepage ability.
7. Cable integrity (spark) control. Detection of insulation defects in the cable manufacturing process.
8. Insulation or sheath tensile strength and elongation.
Insulation and sheath material itself mechanical properties, the performance of external factors, working conditions.
9. Thermal aging.
Insulation and sheath materials in a certain time and thermal conditions will occur under the aging reaction, can be based on the performance of the cable type selection, to confirm the material’s ability to resist aging.
10. Ozone resistance.
In the high electric field to the local air will produce free, that is, it will produce ozone, ozone is a strong oxidant, cross-linked cable under normal circumstances can withstand ozone.
11. Chemical resistance to oil, acid and alkali.
Cable surface with grease, chemical dirt will directly or indirectly affect the performance of the cable, especially locomotive medium-voltage cable, insulation and mechanical properties will change.
12. Thermal extension.
Check the degree of crosslinking of the molecular structure of the insulation and sheath materials to ensure that the properties are met. Locomotive power cables are cross-linked cables. (Cross-linking: the linear molecular structure into a mesh molecular structure.)
3. Railway locomotive power cable selection
Locomotive power cable is mainly used for transmitting large current power signals, such as transmitting the driving current of the motor or transmitting the power supply current of the vehicle, etc. It is generally a single-core cable. In the selection of more attention to the cable cross-section and cable heat resistance.
★EN50382-2
Cable structure
1. Conductor: Tinned copper conductor category 5 or 6 structure
2. Insulation: Silicone rubber insulating material
3. Sheath: Silicone rubber sheath material
Product Characteristics
Operating temperature: -50~120℃, -50~150℃,
Rated voltage: 1.8/3.0kV, 3.6/6.0kV
Fire rating: meet EN45545-2 R15/R16 HL3
Dielectric strength: >8MPa
Elongation at break: 200%
Cable bending radius: 6D(D cable O.D.)
Color: Black
★EN50264-2-1
Cable structure
1. Conductor: Soft tinned annealed copper wire type 5 construction
2. Insulation: Standard low-smoke halogen-free elastic compound
3. Sheath: Standard low smoke halogen free elastomeric compound.
Product Characteristics
Temperature resistance: -40~90°C
Voltage rating: 0.6/1.0kV, 1.8/3.0kV, 3.6/6.0kV
Fire rating: meet EN45545-2 R15/R16 HL3
Dielectric strength: >10Mpa
Elongation at break: >125%
Cable bending radius: 4D(D cable O.D.)
Color: black
TSTCABLES specializes in rail transportation cable applications and solutions, and has obtained EN50264, EN50382, EN50306, EN45545 and TB/T1484.3 and CRCC certificates.
Also available in:
English