
Fire Resistant EN45545-2
Stable on -60℃ ~ 280℃
- Customized Design Production
Small MOQ
Short Lead Time
- Long Time Guarantee
- Home
- /
- Polyimide Cable Wire Polyimide...
The pyramid of polymer materials: Application of polyimide (PI) extruded cables
Manufacturer TST CABLES reveals the characteristics, advantages and applications of the top polymer material polyimide extruded PI cable.
In the early morning of December 8, 2018, the Chang’e-4 probe was launched from the Xichang Satellite Launch Center. This time, Chang’e-4 successfully brought the national flag to the back of the moon, marking the space with the “Chinese logo”. It is reported that the national flag of the probe is not made of common chemical fiber fabrics, silk, cotton and other textiles. It is well known that the space environment is very special. There is no atmosphere on the surface of the moon. It is in a vacuum state. When exposed to sunlight, the maximum temperature of the moon’s surface during the day can reach 123°C. At night, outside the lunar module, the temperature on the moon will drop sharply to minus 233°C.
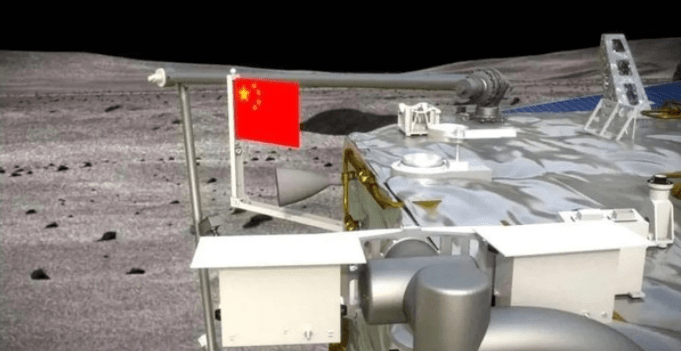
Ordinary materials cannot withstand such an extreme temperature difference. In addition, the ultraviolet rays produced by the sun are very strong, and there is also radiation from cosmic rays and high-energy particles, which have a strong destructive effect on materials.
The flag flying on the moon is made of PI organic polymer film material, which is completely different from the common flag. It can withstand the harsh lunar surface environment and does not fade or deform. What are the special advantages of PI material that makes it unique among polymer materials? Friends who are interested in PI material can learn more about it with TST CABLES.
Introduction to Polyimide (PI)
Recently, all countries have listed the research, development and utilization of PI as one of the development priorities of new chemical materials in the 21st century. PI has great application prospects as a structural material or a functional material due to its outstanding characteristics in performance and synthesis.
Polyimide (PI) is known as the top material of the pyramid of polymer materials, and is also known as a “problem solver”. Some industry insiders even believe that “without PI, there would be no microelectronics technology today.”
Polyimide (PI) is an aromatic heterocyclic polymer compound with an imide chain link in its molecular structure. It is one of the most heat-resistant varieties of engineering plastics. PI has very excellent performance and is widely used in complex application scenarios such as aerospace, mechanical chemical industry, national defense and military industry. PI has the highest flame retardant rating (UL-94), good electrical insulation performance, mechanical properties, chemical stability, aging resistance, radiation resistance, and low dielectric loss. These properties will not change significantly in a wide temperature range (-269℃~400℃), so it is widely used in flexible screens, rail transportation, aerospace, fire retardant, photoresist, electronic packaging, fan blades, automobiles, weapons and equipment and many other fields.
Market prospects of polyimide (PI)
According to relevant statistics, the global aviation manufacturing industry market size continues to grow, and the current global market size has exceeded one trillion US dollars.
The scale of China’s commercial aerospace market has grown year by year. From 2015 to 2020, the output value has exceeded one trillion yuan from 376.42 billion yuan, with an average annual growth rate of 22%. It is expected that the market size will reach 233.82 billion yuan in 2024. Relevant institutions predict that the global commercial aviation equipment market size will grow by 3.7% in the next five years, and by 2027, the global aviation equipment market size will reach 117.69 billion US dollars.
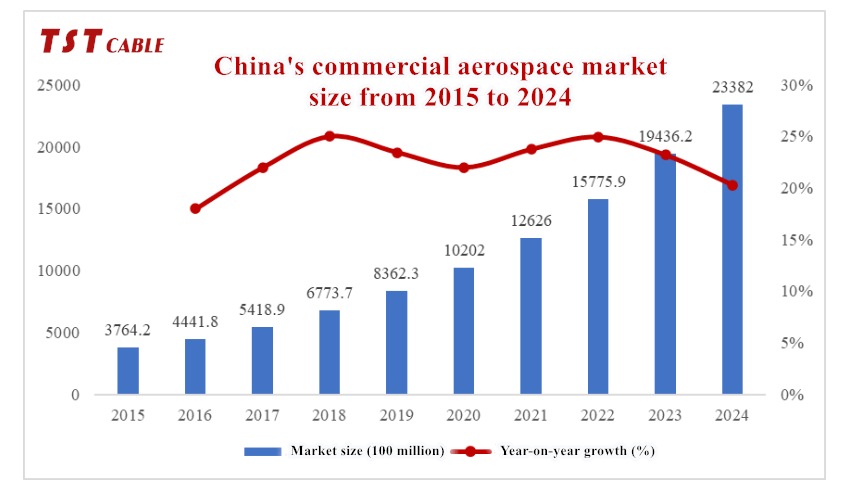
Polyimide (PI) Cable Overview
Definition: Polyimide cable refers to a cable that uses polyimide as an insulating material.
Features: It has excellent high temperature resistance, good electrical properties and chemical stability, and is suitable for high temperature environments and special application fields.
Standards: Common polyimide cable standards include UL1330, UL1331, etc. These standards specify the electrical properties, mechanical properties and combustion properties of the cable.
Polyimide (PI) material classification and application
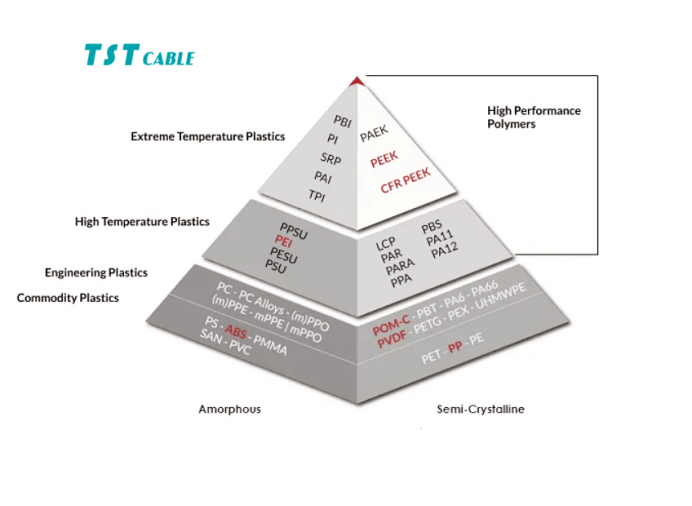
Polyimide (PI) materials can be applied to many fields due to their excellent performance, and can also be divided into many types, including engineering plastics, fibers, photosensitive PI, foam materials, coatings, adhesives, films, aerogels, composite materials, etc.
Among many polymers, polyimide (PI) is the only polymer with a wide range of applications and shows outstanding performance in every application field.
In addition, with the gradual maturity of the carbon fiber industry, the demand for carbon fiber reinforced composite materials has increased significantly. The combination of polyimide and carbon fiber, as one of the most excellent composite material combinations, has obvious advantages in seizing the high-end market.
Polyimide (PI) covers almost all types of polymer materials, including high-performance films, engineering plastics, foam plastics, chemical fibers, adhesives, resin matrices, insulating materials, functional materials, composite materials, etc.
Based on this, TST CABLES specially organizes the characteristics of polyimide materials and related application directions in various fields, and will introduce polyimide cables in detail from multiple angles.
PI electromagnetic flat wire (extrusion type)
“PI magnet wire flat wire” usually refers to a special PI wire used for winding electrical equipment such as motors and transformers. Here, “PI” stands for “Polyimide”, which is a high-performance thermosetting plastic known for its excellent heat resistance and electrical insulation properties. Magnet wire refers to the wire used to wind the coils in motors, transformers and other electromagnetic devices, and flat wire refers to the cross-sectional shape of this wire being flat rather than the traditional round shape.
Flat magnet wire has several advantages over round wire:
1. High space utilization: Flat wires can be arranged closely, reducing the gaps between coils, thereby improving the effective space utilization of motors or transformers.
2. Good heat dissipation performance: Since flat wires have a large contact area, they help improve heat dissipation efficiency.
3. Uniform current density: Flat wires can make current distribution more uniform, reduce the impact of skin effect, and thus improve efficiency.
8 advantages of polyimide (PI) extruded cables
1. High temperature resistance: Polyimide cables can work stably in high temperature environments, with a maximum operating temperature of 250°C to 265°C.
2. Chemical stability: It has good tolerance to a variety of chemicals and is suitable for chemical industrial environments.
3. Low smoke and halogen-free: The amount of smoke produced during combustion is low and does not contain halogen compounds, which is friendly to human health and the environment.
4. Flame retardant: It has good flame retardant properties and is suitable for applications that require flame retardant properties.
5. Flexibility: Even under low temperature conditions, polyimide cables can still maintain good flexibility and are easy to bend and install.
6. Scratch resistance: Polyimide extruded wire has better scratch resistance than polyimide wrapped wire, which can effectively prevent damage to the outer skin of the wire and extend the service life of the wire.
7. Super strong adhesion: Polyimide extruded wire has super strong insulation adhesion due to its special process advantages. This not only has a strong stability for signal transmission, but also does not cause “shrinkage” at the joint, ensuring the safe operation of the equipment.
8. Low dielectric loss: For some medical devices that need to transmit high-frequency signals, low dielectric loss is very important. Polyimide extrusion wire has a lower dielectric constant and lower dielectric loss, which ensures the accuracy and stability of signal transmission and reduces signal attenuation and interference.
Comparison of scratch resistance test between new extruded PI cable and wrapped PI cable
TST CABLES R&D engineers conducted scratch resistance tests on extruded PI wire and wrapped PI wire in the laboratory under the same conditions. The data are as follows:
Category | Conductor diameter mm | Finished product outer diameter mm | Insulation thickness mm | Scratch resistance (10N) |
PI CABLE Wrapping wire | 0.5 | 0.97 | 0.235 | 178 |
PI CABLE Extrusion wire | 0.4 | 0.6 | 0.1 | 5100 |
From the above scratch resistance results, it can be clearly seen that the surface of the extruded polyimide cable is very smooth and has high scratch resistance. The experimental results show that the extruded PI cable has a longer service life than the wrapped PI cable, is wear-resistant, scratch-resistant, tensile-resistant, and has more stable electrical properties.
Comparison of withstand voltage test data of new extruded PI cable and wrapped polyimide cable
Polyimide (PI) extruded cable application areasz
Category | Conductor diameter mm | Finished product outer diameter mm | Insulation thickness mm | Withstand voltageKv | Insulation resistanceMΩ/Km |
PI CABLE Wrapping wire | 0.5 | 0.97 | 0.235 | 10 | 2332 |
PI CABLE Extrusion wire | 0.4 | 0.6 | 0.1 | 12 | 10800 |
From the above experimental data, it can be seen that when the insulation thickness is more than doubled, the withstand voltage of the extruded cable will still be much higher; the insulation resistance value is also several times higher. It can be seen that the withstand voltage of the extruded PI cable is stronger and more stable than that of the wrapped PI cable.
With the continuous advancement of material science, polyimide materials that can be used for injection molding have been born. On this basis, TST CABLES cable engineers have developed polyimide insulated cables that can be extruded and produced after repeated process tests and improvements.
The advent of TST CABLES extruded polyimide cables overcomes the fatal defects of wrapped polyimide film cables, improves the continuity and airtightness of polyimide insulation, improves the electrical performance and mechanical strength of the product, and improves its chemical corrosion resistance.
Aerospace:
Application: Polyimide cables are widely used in wires and cables inside aircraft and spacecraft.
Advantages: Excellent high temperature resistance and chemical stability, suitable for environments with extreme temperature changes.
Automobile manufacturing:
Application: Polyimide cables are used for wires and cables in automobile engine compartments, such as sensor connecting wires.
Advantages: Good high temperature resistance and chemical resistance, able to work stably under extreme conditions.
Medical equipment:
Application: Polyimide cables are used for wires and cables in medical equipment, such as monitoring equipment and therapeutic instruments.
Advantages: Low smoke and halogen-free characteristics, suitable for medical environments that require high safety.
Laboratory equipment:
Application: Polyimide cables are used for wires and cables in laboratory equipment, such as high temperature experimental furnaces.
Advantages: Excellent high temperature resistance and chemical stability, suitable for experimental environments that require precise control.
Industrial automation:
Application: Polyimide cables are widely used for signal transmission and power supply of industrial automation equipment.
Advantages: Excellent high temperature resistance and chemical stability, suitable for harsh environments.
Heating equipment:
Application: Polyimide cables are used for wires and cables in high temperature environments such as heating equipment and ovens.
Advantages: Good high temperature resistance and flexibility, suitable for applications requiring frequent bending.
Polyimide (PI) extruded cable technical parameters
PI cable material has excellent thermal stability and can be used for a long time in the temperature range of -269~260℃. The short-term use temperature reaches 400~450℃, and the decomposition temperature is generally around 500℃. It has good mechanical properties. The tensile strength of isophenyl PI film reaches 250MPa, and the tensile strength of biphenyl PI film reaches 530MPa. It has a low thermal expansion coefficient, which is generally (2~3)×10-5/℃; the biphenyl type can reach 10-6/℃. It has good dielectric properties, and its dielectric constant is generally around 3.4, the dielectric strength is 100~300kV/mm, the volume resistivity is 1017Ω·cm, and the dielectric loss is 10-3.
Combustion performance of polyimide (PI) cable:
Flame retardant grade: According to different standards, polyimide cables may have different flame retardant grades, such as VW-1, FT1, etc.
Burning test: vertical burning test, horizontal burning test, etc.
Polyimide (PI) cable standards and tests
UL1330: Applicable to wires and cables in high temperature environments, with a maximum operating temperature of up to 250°C.
UL1331: Applicable to wires and cables in high temperature environments, with a maximum operating temperature of up to 265°C.
Other certifications: CE, TUV, CSA, etc.
Polyimide (PI) cable test items
Electrical performance test: including conductor resistance test, withstand voltage test, insulation resistance test, etc.
Burning performance test: including vertical burning test, horizontal burning test, etc., to ensure that the cable has good flame retardant performance.
Physical performance test: including tensile test before and after aging, tensile test, etc., to evaluate the mechanical strength and durability of the cable.
Environmental adaptability test: including high and low temperature resistance test, chemical corrosion resistance test, etc., to ensure the performance and safety of the cable under different environmental conditions.
The above introduction is some of the characteristics and applications of conventional ordinary polyimide (PI) cables. After thousands of material selections, research and development, and testing, TST CABLES has innovated on the basis of ordinary PI materials and developed a new type of extruded polyimide (PI) cable, whose key performance exceeds that of ordinary polyimide (PI) cables by nearly twenty times. The following is a comparison of the test performance of extruded polyimide (PI) cables and ordinary wrapped polyimide (PI) cables. For users who pursue high-quality polyimide (PI) cable performance, this is a great advancement and transcendence in cable technology. In this era full of opportunities, only by constantly innovating, daring to try, and breaking boundaries can we continue to grow.
TST CABLES High-Performance Extruded Polyimide (PI) Cable - Extremely Heat-Resistant, Excellent Performance
TST CABLES extruded polyimide cable has unique advantages among many cable products due to its unique process advantages. In particular, its remarkable surface smoothness, compared with traditional wrapped polyimide cable, extruded polyimide cable has better surface smoothness, wear resistance and electrical performance.
While pursuing excellent performance, we are well aware of the importance of power safety. Extruded polyimide cable is designed for harsh environments to ensure that every inch of cable can withstand the test of time and environment. Whether in busy industrial automation control systems or in the aerospace field with extreme temperature changes, TST CABLES extruded polyimide cable can provide stable electrical connections, allowing every task of mechanical equipment to be completed smoothly.
TST CABLES’s PI cable is made of high-quality polyimide material, which not only has excellent high temperature resistance and chemical stability, but also can resist the erosion of a variety of chemicals, ensuring excellent performance in complex environments. From sophisticated manufacturing processes to strict quality control, every step is designed to bring you safe, reliable and efficient electrical connection solutions.
Related by TST:
TST cables low smoke halogen free cable: “invisible guardian” in fire
In a smoke-filled environment, 80% of casualties are not caused...
Read MoreCharacteristics and Applications of LSZH Multi core Charging Cables
Low Smoke Zero Halogen (LSZH) multi-core charging cables are designed...
Read More600℃ High Temperature Resistant Cable Selection Guide for Aviation cable
In the fields of aviation and aerospace, the importance of...
Read MoreComparison between rail transit cables and other cables
With the development of high-speed railways and urban rail transit,...
Read MoreAdd Your Heading Text Here
Also available in:
Arabic
English
German
Indonesian
Japanese
Russian
Spanish
Thai
Vietnamese
Portuguese (Brazil)