
- Fire Rsistant EN45545
- Stable on -200ºC ~ +260ºC
- Customized Design Production
Small MOQ
Short Lead Time
- Long Time Guarantee
- Home
- /
- Peek Cable Peek Wire...
PEEK cable|PEEK wire|PEEK Insulated Wire
PEEK cable, also known as polyetheretherketone (PEEK for short), is a fully aromatic semi-crystalline thermoplastic polymer. Due to the rigid benzene ring, soft ether bond and carbonyl group that enhances the intermolecular force in the macromolecular chain, the structure is regular, so it has unique properties. It is a special polymer material and is known as the tip of the pyramid of the plastic industry. It is a cable that uses polyetheretherketone as the insulation material or sheath material. It has the advantages of high heat resistance, radiation resistance, chemical corrosion resistance, high impact strength, good wear resistance and fatigue resistance, flame retardancy, excellent electrical properties, etc., and can meet the stringent requirements for cables under special conditions.
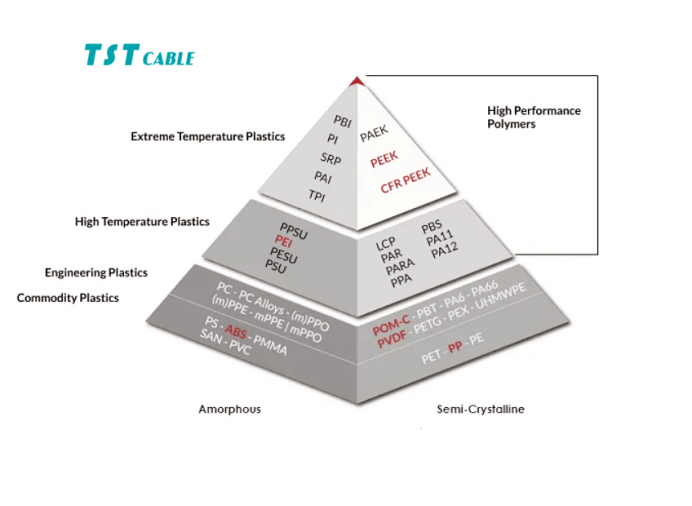
PEEK cable structure design
- Conductor: Tinned copper or bare copper is usually used as the conductor to improve conductivity and corrosion resistance.
- Insulation layer: PEEK is used as the insulation material to provide good electrical and mechanical protection.
- Sheath layer (optional): If needed, a sheath can be added outside to improve protection performance.
PEEK cable core advantages
- Best radiation resistant material
- Best performing low smoke, halogen free material with wide temperature range (-200ºC to +260ºC)
- Excellent resistance to water, fire, smoke and chemicals
- Flexibility: withstands frequent flexing and vibration.
Basic characteristics of PEEK cable
- High temperature resistance: PEEK insulation has excellent heat resistance and can work continuously at temperatures up to 260°C.
- Flame retardancy: PEEK material is not easy to burn and meets the UL 94 V-0 flame retardant rating, which can effectively prevent the spread of fire. It can remain stable even in high temperature environments.
- Chemical resistance: PEEK has excellent chemical corrosion resistance and is suitable for a variety of harsh environments.
- Mechanical strength: PEEK material has high strength and abrasion resistance, ensuring that the cable is still strong and durable under complex conditions.
- Electrical insulation: PEEK provides good electrical insulation performance, ensuring the stability and accuracy of signal transmission.
- Biocompatibility: PEEK material is harmless to the human body and is suitable for medical devices and implants.
- Lightweight: The lightweight characteristics of PEEK material reduce the overall weight of the cable.
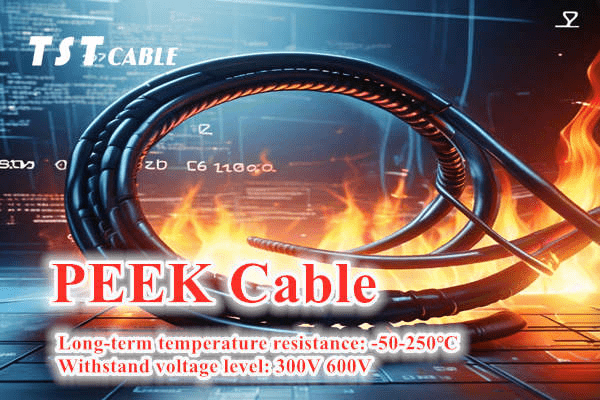
PEEK wire and cable application areas
- Aerospace: Ultra-high temperature wires for aircraft and spacecraft.
- Oil industry: As winding wires and connecting wires for submersible pump motors, maintaining performance at extreme temperatures.
- Wind power plants/atomic power plants: Winding coils for wind farms and nuclear island drive mechanisms, which can be used for a long time under irradiation conditions.
- Shipbuilding industry: Seawater resistance and lightweight design make it widely used in ships.
- High-speed traction locomotives: Suitable for high-speed trains and other transportation equipment.
- Automotive manufacturing: PEEK materials are suitable for automotive electronic systems due to their strength, durability and heat resistance.
- Oil and gas: Used for antenna sleeves, valve seats, electrical connectors, etc., capable of handling extreme temperatures and high pressure environments.
- Military industry, semiconductors and electronics: PEEK is used as an electrical insulating material and mechanical component for semiconductor production and electronic equipment.
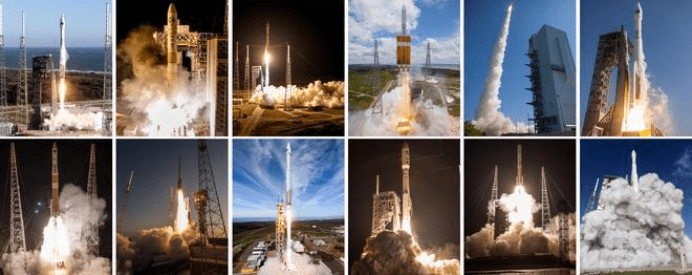
PEEK wires come in two forms: PEEK insulated wires/PEEK high-bonding wires
TST CABLES’ PEEK wire products are available in two forms: PEEK insulated wire (round cable/flat cable) and PEEK high bond wire, which are ideal for motors, generators, transformers, solenoids and other electromechanical devices where superior performance in harsh environments is critical.
PEEK insulated wire
PEEK insulated wire was developed for challenging environments such as the oil and gas, aerospace, and electrical industries. PEEK insulated wire has excellent abrasion resistance and is able to withstand strong pressures and corrosive fluids. For some applications, little or no varnish is required and slot liners may not be required. PEEK insulated wire is best suited for applications that do not require hairpin windings, such as solenoids.
PEEK insulated wire is available in insulation thicknesses ranging from 0.001 inches (0.025 mm) to 0.080 inches (2.032 mm) and American Wire Gauge (AWG) sizes from #3 to #40.
PEEK High Bond Wire (PEEK HB Wire)
PEEK High Bond Wire refers to wires that use PEEK as the insulation layer and have a special process or adhesive added during the manufacturing process to enhance the bond between the conductor and the insulation layer inside the wire.
PEEK Wire High Bond (PEEK HB Wire) performs better than our standard PEEK insulated wire. As a single layer solution, PEEK Wire HB allows motor designers to optimize insulation thickness and improve PDIV performance of magnet wire, guiding the next generation of motor designs in harsh environments. As a single layer, 100% PEEK solution, PEEK Wire HB is ideal for applications that require tight bend radius, such as axial flux motors with hairpin windings. TST CABLES patented extrusion technology allows the PEEK coating to achieve excellent bonding and adhesion to the underlying conductor, allowing the wire to be bent and wound while reducing the risk of delamination.
PEEK HB wire is available with insulation thickness ranging from 0.001 in. (0.025 mm) to 0.015 in. (0.381 mm) and American Wire Gauge (AWG) sizes from #8 to #26.
PEEK Wire and Cable Standards and Tests
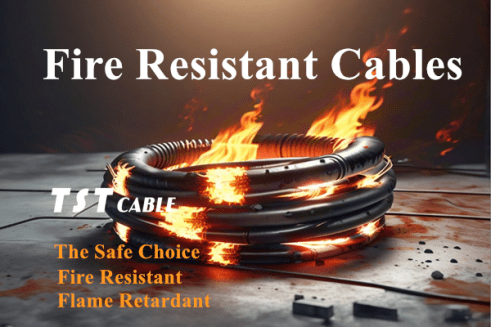
- UL 758: Standard for flexible wires for household and commercial appliances. Although PEEK cables are mainly used in industrial and special applications, they still need to comply with relevant standards.
- EN45545-2, UL 1581: Test the flame retardant properties of cables. PEEK cables must meet the corresponding flame retardant grade requirements.
- IEC 60332: International Electrotechnical Commission’s cable flame retardant standard. PEEK cables may need to meet some of the test requirements.
- ASTM D4288: Used to test the thermal stability of PEEK materials.
- ASTM D638: Used to test the tensile properties of PEEK materials.
PEEK wire and cable test methods
- Temperature resistance test: Test the performance of the cable in a high temperature environment.
- Flame retardant test: Test the reaction of the cable under a fire source, including the burning speed and flame propagation distance.
- Mechanical performance test: Test the tensile strength, bending performance, etc. of the cable.
- Electrical performance test: Test the electrical properties of the cable such as resistance and dielectric strength.
Why choose our PEEK cables?
- Technological innovation: Using the latest PEEK materials and technologies to ensure the cable has excellent performance.
- Quality assurance: Produced in strict accordance with mainstream international standards such as UL/EN/GB, each batch of cables undergoes strict quality inspection.
- Widely applicable: Suitable for a variety of industries and applications to meet the needs of different environments.
- Customer service: Provide full range of technical support and after-sales service to ensure customer satisfaction.
Cooperate with TST CABLES to customize high-quality PEEK cables
Since its establishment in 2003, TST CABLES has been focusing on the design, development, manufacturing and sales of customized cables and harnesses for extreme environments and demanding applications. It produces 250℃ silver-plated/nickel-plated copper conductor PEEK insulated wires and is good at combining high-performance materials to customize new cable solutions. PEEK materials, PI materials, fluorine materials, and silicone materials are one of our main areas of expertise. Our products have passed ISO9001-2016, VDE, 3C, UL, and CE certifications. They are usually the core materials of our customized cable solutions. You can find the products you need in our standard product library. Industry application areas include:
- Aviation cable
- Railway cable
- Nuclear power cable
- Wind power cable
- Oil and gas cable
- Automotive wiring harness
- Medical cable
- Construction cable
- Marine cable
- Industrial cable
In addition to the above industries, PEEK is also widely used in the following types of cables:
Standard coaxial cable/customizable coaxial cable/signal cable/control cable/power cable/lighting cable
Single core cable/multi-core cable/shielded cable/unshielded cable/armored cable/PEEK flat cable/flexible power cable
Sensor cable/watertight cable/low noise cable/CCS cable/triple-layer insulation cable/motor flat wire cable, etc.
What is the difference between LSZH cable and LSF cable?
Some cables are marked as LSF (low smoke), which is different from LSZH.
It only covers part of the equation, because LSF cables may still contain halogens in their materials.
For example, low-smoke PVC cable is LSF, but not LSZH.
These cables still have the threat of halogen gas when burned.
Typically, LSF cables contain additives to help them achieve low smoke and low halogen, but they are not zero halogen.
LSZH cables generally follow stricter standards than LSF cables.
The halogen acids emitted by LSF cables far exceed the limits specified for LSZH cables.
Low Smoke Halogen Free Cable Materials
LSZH cable materials are essentially of two types: thermoplastic LSZH cables and thermoset LSZH cables.
Thermoplastic LSZH materials can be formed by heating multiple times, while thermoset LSZH cable materials can only be formed once.
Therefore, they are not recyclable.
Although PVC is the most common thermoplastic, it is not an LSZH cable because it contains chlorine.
On the other hand, ethylene propylene rubber cable (EPR) and cross-linked propylene cable (XLPE) are LSZH cables.
These two materials are very common in cables along with PVC.
It is worth noting that LSZH cable thermoset materials may not be as flame retardant as chlorinated thermoset materials.
This is a trade-off when using LSZH cables, as their thermal range may be slightly lower than halogen cables.
That said, cross-linked materials, such as XLPE cables, have a higher thermal range.
The LSZH cable material you choose also depends on other factors, such as the rated voltage of the conductor, environmental conditions, and the requirements of the specific application. The material must meet the specified requirements and tests.
Contact Us
Related by TST:
TST cables low smoke halogen free cable: “invisible guardian” in fire
In a smoke-filled environment, 80% of casualties are not caused...
Read MoreCharacteristics and Applications of LSZH Multi core Charging Cables
Low Smoke Zero Halogen (LSZH) multi-core charging cables are designed...
Read More600℃ High Temperature Resistant Cable Selection Guide for Aviation cable
In the fields of aviation and aerospace, the importance of...
Read MoreComparison between rail transit cables and other cables
With the development of high-speed railways and urban rail transit,...
Read MoreAdd Your Heading Text Here
Also available in:
Arabic
English
German
Indonesian
Japanese
Russian
Spanish
Thai
Vietnamese
Portuguese (Brazil)