One,What is PEEK wire?
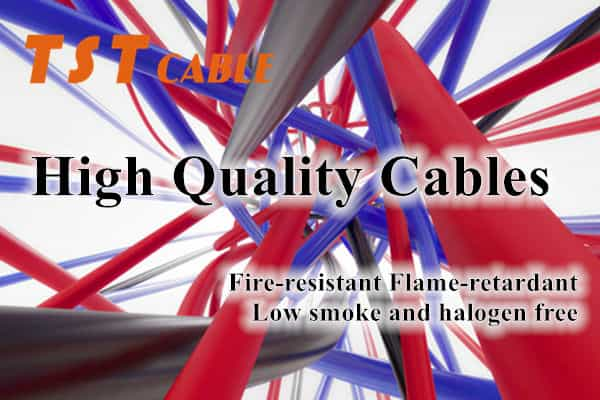
General wire and cable is insulated and sheathed with plastic and rubber, these materials are conventional engineering materials, with abundant sources to meet the mass production, and relatively low cost. But for some special industries such as petrochemical, iron and steel, aerospace, shipbuilding, military, locomotive, nuclear power plants and other heat and high temperature and radiation-related industries, need to be able to withstand a certain higher temperature or radiation wire and cable, ordinary wire and cable obviously can not be used, need to be able to withstand high temperatures, radiation-resistant wire and cable in order to ensure that the safe operation of its power and signal.
Polyether ether ketone (PEEK) is a fully aromatic semi-crystalline thermoplastic polymers, due to the macromolecular chain containing rigid benzene ring, soft ether bond and improve the intermolecular forces of carbonyl, structural regularity, and thus has a unique performance, is a special polymer materials, known as the tip of the pyramid of the plastics industry. It has high heat-resistant grade, radiation resistance, chemical resistance, high impact strength, good abrasion resistance and fatigue resistance, flame retardant, excellent electrical properties, etc., can meet the special conditions of the cable’s demanding requirements.
Second, the characteristics of polyether ether ketone
Polyether ether ketone melting point of 334 ° C, glass transition temperature (Tg) of 143 ° C, the maximum possible crystallinity of about 48%, usually 20% to 30%, it is in the amorphous state of the density of 1.265 g/cm3, and in the maximum degree of crystallization of the density of 1.32 g/cm3. PEEK has the following outstanding properties:
(1) extremely high heat resistance. Can be used at 250 ℃ for a long time, the instantaneous use of temperature up to 300 ℃, at 400 ℃ for a short period of time almost does not decompose. Compared with other high temperature resistant plastics such as polyimide (PEI), polyphenylene sulfide (PPS), polytetrafluoroethylene (PTFE), polyphenylene ether (PPO), the upper limit of the use temperature is nearly 50 ℃ higher.
(2) excellent mechanical properties and dimensional stability, PEEK can maintain high strength at high temperatures, 200 ℃ bending strength is still up to 24 MPa, 250 ℃ bending strength and compression strength of up to 12 ~ 13 MPa, especially suitable for the manufacture of high temperature can be continuous work of the components. high rigidity, dimensional stability and coefficient of linear expansion of PEEK is very close to the metal aluminum. In addition, PEEK also has good creep resistance, can be used in the period of time to withstand great stress, not due to the extension of time and produce significant extension.
(3) Excellent chemical resistance. Even at high temperatures PEEK is also very resistant to most chemicals, corrosion resistance is similar to nickel steel. In general the only thing that can dissolve PEEK is concentrated sulfuric acid.
(4) good resistance to hydrolysis. Can resist chemical damage produced by water or high-pressure water vapor. At high temperatures and high pressure conditions, PEEK can work continuously in the water environment and still maintain good mechanical properties. Such as in 100 ℃ of water immersion for 200 days, the strength remains almost unchanged.
(5) good flame retardant properties. UL 94 V-0 level, self-extinguishing, smoke and toxic gases released in the flame conditions less.
(6) Good electrical properties. In a wide range of frequencies and temperatures, PEEK can keep the electrical properties unchanged.
(7) radiation resistance, PEEK has a very stable chemical structure, in the high dose of ionizing radiation PEEK parts can also work normally.
(8) good toughness. Fatigue resistance to alternating stress is the most outstanding of all plastics, comparable to alloy materials.
(9) Excellent friction and wear resistance. Can maintain high wear resistance and low coefficient of friction at 250℃.
(10) Good processing performance. Easy to extrude and injection molding, and high molding efficiency.
The above ten characteristics, determines the PEEK can be used to produce cables with special properties.
Third, the application of polyether ether ketone in the locomotive thin-walled wire
Due to the rapid development of China’s railway construction, the product types of railroad rolling stock wires and cables and their performance have also developed greatly. Similar to car wires, the application of high temperature resistant thin-walled insulated wires will be more and more for the sake of safety and space saving. At present, the main reference standards for domestic rolling stock thin-walled wires are: EN 50306-1 to 4: 2002, thin-walled railway rolling stock flame-retardant cables; NF F 63-808: 1992 thin-walled insulated and sheathed halogen-free wires and cables; GB 12528-2008, railroad rolling stock cables (wires). However, at present, there are almost no cable material manufacturers in China who can provide thin-walled insulating materials to meet the above standards. Because, for the NF F 63-808: 1992 requirements of the thin-walled wire, that is, halogen-free flame retardant, but also requires the strength of 30Mpa or more, so the current domestic application of non-halogen-free flame retardant polyolefin can not meet the above requirements of the strength, but also can not meet the standard requirements of the abrasion resistance test. Some manufacturers use flame retardant engineering plastics to produce thin-walled wires, which can meet the requirements of flame retardant, tensile strength and abrasion resistance, but the flame retardant insulation resistance is difficult to meet the requirements. For EN 50306-1 to 4: 2002 standard line, although there is no cable tensile strength has not done high requirements, but the general cable manufacturers will do their own corporate standards for cable strength. So low smoke halogen-free flame retardant polyolefin is also more difficult to achieve.
For polyether ether ketone, tensile strength at room temperature up to 100Mpa, and its own halogen-free flame-retardant materials, but also has excellent abrasion resistance and hydrolysis resistance, so the thin-walled wire with polyether ether ketone locomotive is indeed a more suitable material, but the polyether ether ketone has a low elongation at break, the real application, it is best to be able to be modified in this regard, or co-extruded with other materials for the double layer. At present, there are a small number of domestic cable plant to use imported polyether ether ketone to produce thin-walled wire locomotives.
Fourth, polyether ether ketone in the nuclear power plant cable applications
Nuclear power plant with 1E class cable according to the nuclear power plant electrical system equipment safety category is divided into three categories: K1, K2, K3. safety category K1, K2, K3 class has the following definition:
Class K1 electric actuator. Installed within the nuclear reactor containment and still capable of performing their specified functions under normal environmental conditions and below SL2 (Safe Stopping of Reactor Ground Shock) loads and during or after an accident.
K2 type electric actuators. Installed in the containment of the nuclear reactor, they can still perform their specified functions under normal environmental conditions and under SL2 (Safe-Lockout Ground Shock) loads.
Class K3 electric actuators. Installed outside the containment of the nuclear reactor, they can still perform their specified functions under normal environmental conditions and under SL2 (safety stop ground vibration) loads.
Nuclear power plant cables
The operating environments of the three types of cables differ greatly, among which the Kl type has the harshest operating environment and the most demanding performance requirements for cables. For K1 category cables, the raw materials must be low-smoke, halogen-free, flame-retardant, with superior mechanical and physical properties, electrical properties and other characteristics. At the same time, the raw materials must first be able to pass the equivalent of 50 years of operation LOCA when the radiation exposure test, simulated LOCA test and thermal aging evaluation test. Therefore, the selected materials must meet the requirements of Class 1E environment of nuclear power plants.
The most prominent feature of polyether ether ketone is good radiation resistance, in addition, has excellent electrical properties, physical and mechanical properties, flame retardant properties, chemical resistance, so polyether ether ketone can be used as a very good material 1E class K1 cable insulation materials.
Fifth, polyether ether ketone in the cable applications facing problems
Polyether ether ketone as a new type of special materials, has excellent performance, but at present it is not widely used in the cable, or even can be said to be very little. Mainly due to the following reasons:
1, the price problem
Price is the primary problem of polyether ether ketone application. The current market price of polyether ether ketone is very high, some imported materials prices up to 1200 yuan / kg, the price of domestic materials to 500 yuan / kg or more. Cable manufacturers see the price of most of the deterrent, turn to other materials, not to use polyether ether ketone.TST CABLES focus on PEEK cable research and development for many years, PEEK cable cost-effective, the same price, our quality will be higher, you are welcome to send an e-mail at any time to come to the inquiry.
2、Equipment problems
Because the processing temperature of polyether ether ketone is very high, the extrusion temperature to reach 350 ℃ or more, so the general extruder can not meet the requirements, you need to use the extruder with a cast copper heater, and the screw temperature resistance needs to be improved. For most of the cable factory and cable material factory, do not have such equipment, which in turn limits the application of polyether ether ketone.
3, process problems
Due to the current use of polyether ether ketone cable plant is very small, so many users also know less about its extrusion process. Polyetheretherketone for semi-crystalline polymers, extruded cables, if the insulation material crystallinity is different, then many of its properties will also have a greater difference. Therefore, the processing technology of polyether ether ketone also needs to be felt and familiarized with.
TST CABLES – the world’s leading supplier of PEEK cables
Details determine success or failure, in the wide world of high-temperature cable applications, TST CABLES PEEK cables, combining high-temperature resistance, water resistance, flame retardant and fire retardant, chemical resistance, high strength and low friction characteristics, set a new benchmark in the high-temperature cable industry. From the spacecraft flying in space to the deep sea exploration of cutting-edge equipment, from the rigorous scene of precision medical care to the minutiae of intelligent manufacturing, TST CABLES PEEK cables with its extraordinary toughness, comfortable to deal with the challenges of each harsh environment. If you have any needs or questions about nuclear cables, PEEK cables, please feel free to email us and get free samples.
Also available in:
English