xlpe Power cables are a very important part of the power system for transmitting and distributing electrical energy. They undertake the important task of transmitting electrical energy from power stations to substations and then distributing it from substations to end users in the power network. Below, TST CABLES introduces the performance, advantages, structure, standards, installation and maintenance, and technological development trends of power cables in detail.
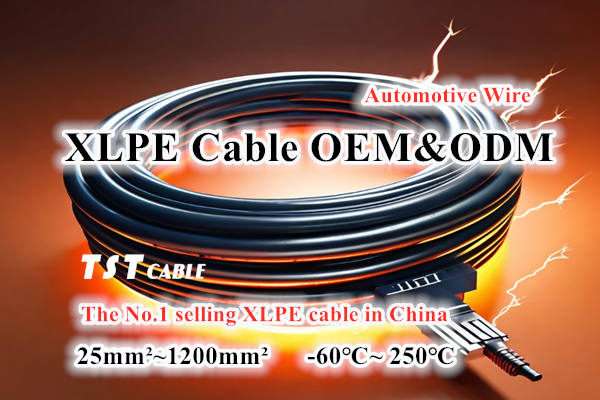
What is power cable
Power cables are composed of one or more insulated conductors wrapped in an outer sheath for transmitting electrical energy. Power cables are designed and manufactured to meet the needs of high-voltage and high-current transmission while ensuring safety and efficiency.
Power cable construction
Power cable conductor
·Material: The conductor of a power cable is usually made of copper or aluminum. Copper conductors have better conductivity, while aluminum conductors are less expensive.
·Cross-sectional area: The cross-sectional area of the conductor is determined according to the size of the transmitted current, usually in square millimeters (mm²).
Power cable insulation layer
·Material: The insulation layer of a power cable usually uses materials such as polyvinyl chloride (PVC), cross-linked polyethylene (XLPE) or ethylene propylene rubber (EPR).
·Thickness: The thickness of the insulation layer is determined according to the voltage level and the environment in which the cable is used.
Power cable sheath
·Material: The outer sheath usually uses PVC or polyethylene (PE) to protect the cable from mechanical damage and environmental factors.
·Type: The sheath may also include special properties such as flame retardant, oil resistant, and UV resistant.
Power cable shielding layer
·Material: In order to reduce electromagnetic interference, some power cables will add a metal shielding layer between the insulation layer and the sheath.
·Function: The shielding layer helps to improve the electrical performance of the cable and protect the cable from the influence of external electromagnetic fields.
Performance characteristics of power cables
Electrical performance
·Resistance: The resistance of the conductor affects the power loss and heating of the cable.
·Capacitance: The capacitance of the cable affects the stability of the power system.
·Insulation resistance: It reflects the quality of the insulation layer and is an important indicator to measure the insulation performance of the cable.
·Shielding effect: The shielding layer can effectively reduce electromagnetic interference.
Mechanical properties
·Tensile strength: The amount of tension that the cable can withstand.
·Bending radius: The minimum bending radius allowed to avoid damaging the cable.
Environmental adaptability
·Temperature range: The temperature range in which the cable can work.
·Chemical resistance: The ability to withstand chemical substances.
·Weather resistance: Cables used in outdoor environments need to have good weather resistance.
Classification of power cables
Power cables can be divided into the following types according to their applications and performance characteristics:
Low voltage power cables
·Voltage level: Generally refers to cables with a rated voltage below 1kV.
·Construction: PVC or rubber is usually used as the insulation layer.
·Application: Suitable for distribution systems inside buildings, home and commercial electricity.
Medium voltage power cables
·Voltage level: Cables with rated voltages between 1kV and 35kV.
·Construction: Cross-linked polyethylene (XLPE cable) is often used as the insulation layer to improve the electrical performance and heat resistance of the cable.
·Application: Used in industrial and commercial facilities, substations, and medium voltage distribution networks.
High voltage power cables
·Voltage level: Cables with a rated voltage of more than 35kV.
·Construction: High-performance insulation materials such as XLPE cable or ethylene propylene rubber (EPR) are used, and multiple shielding layers may be included to reduce electromagnetic interference.
·Application: Used for long-distance transmission lines and trunk lines of large power systems.
Special types of power cables
Submarine power cables
·Purpose: Used for power transmission across water, such as cross-sea transmission lines.
·Features: Good waterproof and corrosion resistance, able to withstand deep-sea pressure.
Mining power cables
·Purpose: Suitable for mines and underground working environments.
·Features: Oil, abrasion and chemical corrosion resistance, as well as good flexibility.
Flame-retardant power cables
·Purpose: Used in places with high fire safety requirements, such as high-rise buildings, subway tunnels, etc.
·Features: Flame-retardant materials are used to delay the spread of fire in the event of a fire.
Power cable usage scenarios
·Transmission lines: Used to transmit electricity over long distances, connecting power stations and substations.
·Distribution networks: Used to distribute electricity from substations to individual users.
·Industrial facilities: Used for power transmission and distribution within factories.
·Civil buildings: used for power wiring inside buildings.
·Special applications: such as submarine cables, mining cables, etc.
Electrical properties of power cables
·Resistance: The resistance of the conductor affects the loss and heat generation of the cable.
·Capacitance: The capacitance of the cable affects the stability of the power system.
·Insulation resistance: The resistivity of the insulation layer determines the insulation performance of the cable.
·Shielding effect: The shielding layer can reduce electromagnetic interference.
Power cable safety standards and certifications
Power cables must comply with relevant electrical and safety standards to ensure their quality and safety. Common standards and certifications include:
·IEC (International Electrotechnical Commission) International Electrotechnical Commission standards.
·UL (Underwriters Laboratories) American Underwriters Laboratory Certification.
·CE (Conformité Européenne) European Union safety certification.
·RoHS (Restriction of Hazardous Substances) Restriction of Hazardous Substances Directive.
Precautions for power cable installation
·Bending radius: The minimum bending radius must be observed during installation to avoid damage to the cable.
· Grounding: Ensure that the grounding end of the cable is properly installed to improve safety.
· Environmental factors: Consider factors such as temperature, humidity, and chemical corrosion in the installation environment.
· Regular inspection: Regularly perform electrical performance tests and appearance inspections on the cable.
Power cable maintenance
· Regular inspection: Regularly perform electrical performance tests and appearance inspections on the cable.
· Cleaning and maintenance: Keep the cable surface clean to avoid dust and debris that may cause aging of the insulation layer.
· Storage conditions: Properly store unused cables to avoid adverse conditions such as direct sunlight and moisture.
Power cable selection recommendations
· Voltage level: Select the appropriate cable type according to the voltage level to be transmitted.
· Use environment: Consider the environmental conditions where the cable will be installed and select appropriate materials and construction.
· Electrical performance: Ensure that the cable meets the required electrical performance indicators, such as resistance, capacitance, etc.
· Safety standards: Ensure that the cable meets relevant electrical and safety standards, such as IEC, UL, CE, etc.
Power cables play a vital role in power systems, and correct selection and installation are essential to ensure the safety and efficiency of power systems. When choosing power cables, you should consider the specific needs of the application, the electrical performance of the cable, the mechanical properties, and the environmental adaptability. If you need to choose a power cable for a specific application, be sure to consult professional cable supplier TST CABLES for the best advice.
Cooperate with cable manufacturer TST CABLES to customize high-quality power cables
TST cables custom cables strictly follow the International Electrotechnical Commission (IEC) standards, including but not limited to IEC 60227, IEC 60502, etc., to ensure that each cable has excellent electrical performance, meets global specific standards, and guarantees high quality.
Comply with EU EN standards to ensure the compliance and high quality of cables in the European market. Design and test according to US UL standards to meet the high standards of the North American market. Follow Chinese GB standards, such as GB/T 42740-2023, to ensure that products meet domestic market needs. Compliance with cable industry standards is essential to ensure the quality and safety of cable products. Cable manufacturers, installers, and users should comply with relevant standards to ensure that cable systems can operate safely and reliably. As technology advances, these standards will continue to be updated and developed to adapt to new needs and technical challenges.
If you have needs for customized industrial cables, power cables, control cables, etc., and need further technical support or cable solutions, you can visit the TST CABLES official website or feel free to send an email to the professional cable engineer of TST cable manufacturer (email: lixiangchao@testeck.com, please state your country, your industry, and your needs in the email, we can also provide you with free samples).
Also available in:
English