This article mainly introduces the structural design and manufacturing process of TST CABLES super-large cross-section shielded flexible cable.
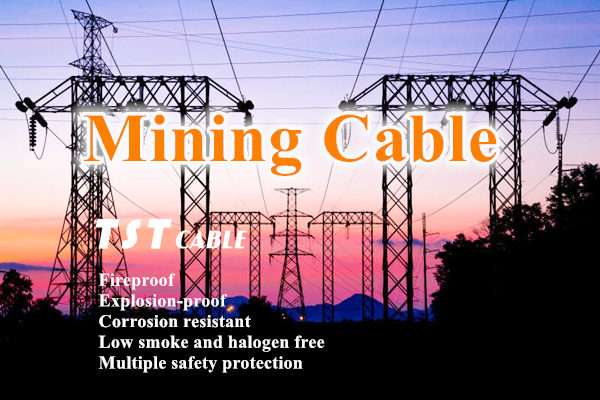
Super-large cross-section cables refer to special cables whose conductor cross-sectional area is much larger than that of conventional cables. They are mainly used in applications where large currents are transmitted or high voltages are carried. Due to their special size and performance requirements, these cables require special technical treatment during design, manufacturing and installation. The following is some key information about super-large cross-section cables:
The cross-section of a cable refers to the area of the conductor cross-section in the cable. There are three commonly used representations internationally: my country’s CWG, American AWG and British SWG. Generally speaking, when the grid voltage is 220V, a 1mm2 copper conductor cable can carry a working power of 1~1.5kW. For example, a cable with a cross-section of 50mm2 can be selected for a working power of 40kW.
Features of super-large cross-section shielded cables
1. High current carrying capacity: super-large cross-section cables can carry larger currents and are suitable for applications where high power transmission is required.
2. Low resistance: A larger conductor cross-sectional area can reduce the resistance of the cable and reduce energy loss.
3. Good heat dissipation performance: A larger cross-sectional area helps improve the heat dissipation performance of the cable, ensuring safe operation under high load conditions.
4. Mechanical strength: Multi-strand twisting is usually used to enhance the mechanical strength and flexibility of the cable.
5. Durability: In order to cope with complex working environments, super-large cross-section cables usually have higher durability and service life.
Application areas of super-large cross-section shielded cables
Super-large cross-section cables are widely used in the following fields:
1. Power transmission: used for high-voltage transmission lines to ensure efficient transmission of power.
2. Industrial equipment: suitable for the connection of large motors, transformers and other equipment, as well as power supply for high-power equipment inside factories.
3. Rail transit: used for traction power supply in urban rail transit systems, such as subways and high-speed railways.
4. Wind farms: connect wind turbines to the power grid to ensure effective transmission of power.
5. Shipbuilding and marine engineering: used for power transmission in large ships, offshore drilling platforms and other facilities.
6. Data centers: provide stable power support for high-density server clusters in data centers.
Design and manufacturing of ultra-large cross-section shielded cables
1. Conductor material: Copper or silver-plated copper is usually used as the conductor material to improve conductivity and corrosion resistance.
2. Insulation layer: Use materials with high insulation performance, such as cross-linked polyethylene cable (XLPE), polyvinyl chloride cable (PVC) or ethylene propylene rubber cable (EPR) to ensure the safe operation of the cable under high voltage conditions.
3. Sheath layer: Use wear-resistant and weather-resistant materials, such as polyvinyl chloride cable (PVC), polyethylene cable (PE) or polyurethane cable (PU) to protect the cable from the external environment.
4. Shielding layer: In applications where electromagnetic interference needs to be reduced, the cable will be equipped with a metal shielding layer to improve electromagnetic compatibility.
Installation and maintenance of ultra-large cross-section shielded cables
1. Installation tools: The installation of ultra-large cross-section cables requires professional tools and equipment, such as large-tonnage stripping machines, crimping pliers, etc.
2. Joint treatment: The joints need special treatment to ensure the electrical performance and mechanical strength of the connection.
3. Laying path: It is necessary to plan a reasonable laying path to ensure that the cable is not mechanically damaged and facilitate later maintenance.
Selection Guide for Super Large Section Shielded Cable
When selecting super large section cables, the following factors need to be considered:
– Current demand: Select the appropriate cross-sectional size according to the actual current demand.
– Environmental conditions: Consider the use environment of the cable and select suitable insulation and sheath materials.
– Safety standards: Ensure that the cable meets relevant national standards and industry standards.
– Cost-effectiveness: Comprehensively consider the price and service life of the cable and select the most cost-effective solution.
Case Background of Super Large Section Shielded Cable
In recent years, major malignant accidents in coal mines have occurred repeatedly, and coal mine safety has been listed as a national safety production priority. Therefore, the quality of coal mine cables has received more and more attention. Super large section mobile metal shielded soft cables for coal mines are developed and researched in response to market requirements. In 2016, a coal mining company in Shanxi Province consulted with multiple manufacturers without success and negotiated with our factory to manufacture coal mine cables with a long length, a voltage level of 3.6/6 kV, and a super high power for connection between transformers and underground electrical appliances. According to the power of the electrical appliance, a cable with a cross-section of 185 cm is required. We set the cable model specification as: MYPTJ-3.6/6 kV 3×185+3×70/3+2×25+1×2.5, and signed an order contract after the user agreed. This cable has three major characteristics: first, the cable cross-section is very large, with an outer diameter of 80~89 mm; second, the cable structure is complex and the number of cores is large; third, the length is long and the weight is heavy, which exceeds the production capacity of existing equipment. At present, domestic cable factories are still unable to produce this type of cable products. If they rely on imports, the price will be too high. Therefore, our factory decided to trial-produce this product to meet the needs of the market. At the same time, it can also expand the domestic cable varieties and prepare for entering the international market.
Analysis of the structure design and materials of super-large cross-section shielded cable
2.1 Cable structure design and analysis
Figure 1 Structure of super-large cross-section mobile metal shielded soft cable for coal mines
According to the ordered cable model specifications, the corresponding cable structure was designed (see Figure 1) and analyzed as follows:
(1) Conductor. The conductor is made of soft copper wire, and its performance should meet the requirements of the fifth type of soft conductor in GB/T3956-1997. The surface should be smooth, free of oil, sharp protrusions or other defects that damage the insulation.
(2) Conductor shielding. In order to prevent the tip discharge phenomenon caused by the uneven surface and uneven roundness of the conductor, and because the cross-section of the power line core is too large, in order to prevent the power line core conductor from loosening when extruding the insulation layer and shielding layer, the conductor shielding adopts a combined shielding form of first wrapping the semi-conductive cloth tape and then extruding the semi-conductive shielding layer.
(3) Insulation layer. According to the rated voltage of the cable, ethylene propylene rubber suitable for high voltage level is selected as the insulation material of the cable, and the insulation thickness of the cable and the insulation resistance at 20. C are determined with reference to the MT 818.6-1999 standard to ensure that the finished cable can withstand the 11 kV power frequency voltage test for 5 minutes without cable breakdown.
(4) Insulation shielding layer. The cable conductor shielding layer and the insulation shielding layer play the role of uniform electric field, adsorbing free impurities, and shielding external electric field. During the design process, after considering the above factors, the insulation shielding layer of the power core is designed as a shielding form that combines a wrapped semi-conductive cloth tape and a metal/fiber braided shield. The metal braided layer can also serve as a ground wire.
(5) Auxiliary core. It consists of the following:
1) Auxiliary ground wire. The cable adopts the form of metal braiding as a ground wire. If the total cross-section of the metal braided layer does not meet the requirements of the cable ground wire cross-section, an auxiliary ground wire is allowed. Therefore, an auxiliary bare copper wire with a cross-sectional area of 10 mm is added to increase the cross-section of the ground wire.
2) Control core. The control core is insulated by tinned conductor and then wrapped with polyester film tape to increase the relative slip between the cores.
3) Monitoring core. After the monitoring core is extruded with an insulation layer, it is wrapped with a layer of polyester film tape to prevent the copper wire from piercing the insulation during braiding; to prevent external signal interference, the insulation shielding adopts metal/fiber braiding, and the braiding coverage should reach 88.
(6) Sheath. According to the use environment and conditions, in order to make the cable have excellent mechanical properties and flame retardant properties, the cable adopts a combined sheath structure of red flame retardant chloroprene inner sheath and polyurethane outer sheath.
2.2 Cable core arrangement
In the arrangement of the cable core, the auxiliary ground wire is located at the center of the cable core, and the two control cores and one monitoring core are placed in the gaps of the three power cores. Such a cable structure is reasonable and stable, and the electric field distribution is uniform. Six filling strips are added in the gaps of the three power cores. The use of filling strips can not only make the cable core round and improve the appearance of the cable, but also save the amount of sheath glue, thereby reducing product costs and improving economic benefits.
2.3 Selection of main materials
(1) Insulation layer. According to the cable voltage level and the requirements of relevant standards for cable insulation resistance, materials with a volume resistance of not less than 1O13~1O14Ω·m must be selected, and 9O must be considered at the same time. C conductor long-term working temperature, the material is required to have excellent heat aging resistance. Therefore, EPDM insulation rubber with excellent electrical properties is selected, and its performance should comply with the provisions of GB/T7594.
(2) Sheath. Coal mine cables have high requirements on the mechanical properties and flame retardant properties of the sheath. It not only requires the cable sheath to have flame retardant, wear resistance, anti-smashing and tear resistance, but also requires the cable to have excellent bending performance. There are many materials that can be used as mining cable sheaths, such as chlorosulfonated polyethylene, chlorinated polyethylene and chloroprene rubber, as well as polyurethane, which has been used for a short time. Through a comprehensive comparison of the properties of these four materials (see Table 1), combined with the requirements of existing processes for material extrusion, in line with the purpose of boldly using new materials, a combined sheath form of chloroprene rubber as the inner sheath and polyurethane as the outer sheath was selected.
Process manufacturing and quality assurance of key processes of ultra-large cross-section shielded cables
The cable structure is complex and the actual production and manufacturing process is relatively cumbersome. Therefore, special attention should be paid to the quality control of key processes. In relevant papers, the quality control of each process has been discussed in detail. Here, we will only briefly explain the key issues and will not elaborate on the others:
(1) Wrapping the conductor with semi-conductive tape can not only play the role of conductor shielding, but also prevent the conductor from loosening. However, it is difficult to extrude the semi-conductive shielding layer of the conductor after wrapping. Therefore, the wrapping tape is required to be flat and wrinkle-free. When extruding the semi-conductive shielding layer, the distance between the mold core and the mold sleeve should be adjusted to reduce the radial pressure and ensure the continuity of the semi-conductive shielding layer.
(2) The quality of cabling will directly affect the quality of the cable. Due to the complex structure and large number of cores of the cable, the difficulty of cabling is increased. During the cabling process, the tension of the pay-off drum is required to be uniform, the wrapping tape is continuous, flat and tight, and the overlap rate is 15 to 25, so that the cable core is round and the occurrence of quality defects such as serpentine, loose strands and skipped strands of the cable core is eliminated.
Ultra-large cross-section cables play an important role in modern power systems and industrial applications with their excellent performance and wide applicability. Through careful design and manufacturing, these cables can provide reliable power transmission solutions under various extreme conditions. Choosing the right extra-large cross-section cable can not only improve the efficiency and safety of the system, but also bring long-term economic benefits to the enterprise. If your industry and equipment require extra-large cross-section cables, you are welcome to contact TST CABLES cable engineers (email: lixiangchao@testeck.com) at any time to communicate your needs and get free samples.
Also available in:
English