Introduction to Marine Cables
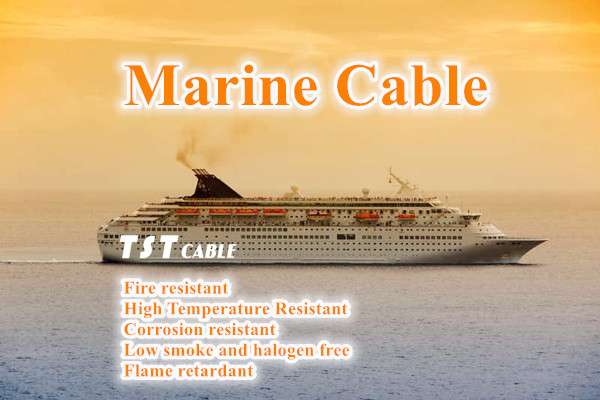
Submarine cables(Marine Cables Application of Cables for Offshore Ship Equipment) are cables wrapped in insulating materials, laid on the seabed, and used for telecommunication transmission. Submarine cables are divided into submarine communication cables and submarine power cables. Modern submarine cables use optical fiber as materials to transmit telephone and Internet signals.
Submarine cables are divided into submarine communication cables and submarine power cables. Submarine communication cables are mainly used for communication services, which are expensive but highly confidential. Submarine power cables are mainly used to transmit high-power electrical energy underwater, which is equivalent to the role of underground power cables, except that the application occasions and laying methods are different. Since submarine cable projects are recognized by countries around the world as complex and difficult large-scale projects, complex technologies are applied from environmental detection, marine physical surveys, to cable design, manufacturing and installation. Therefore, there are only a few submarine cable manufacturers in the world, mainly Norway, Denmark, Japan, Canada, the United States, Britain, France, Italy and other countries. In addition to manufacturing, these countries also provide laying technology.
Material for making marine cables
The core of the submarine optical cable is made of high-purity optical fiber as thin as hair, which guides light along the path of the optical fiber through internal reflection. Submarine cables must be able to withstand the tremendous pressure of 8 kilometers underwater, which is equivalent to the weight of an elephant on a human thumb. NEC’s deep-sea cables are made of lightweight polyethylene, and the entire cable is only 17 mm thick.
Marine cable manufacturing process
In the production of submarine optical cables, the optical fibers are first embedded in a jelly-like compound to protect the cable from damage even when it comes into contact with seawater. The cable is then placed in a steel pipe to prevent it from being damaged by the pressure of water. Next, it is wrapped in a steel wire with extremely high overall strength, and then in a copper tube, and finally covered with a protective layer of polyethylene material. On the coast near the continental shelf, submarine cables are usually laid with lightweight cables and stronger steel wires, and covered with asphalt coatings to prevent seawater corrosion.
Marine cable capacity
Submarine cables can carry up to 80Tbps of data, which is equivalent to transmitting 4.7GB of capacity in one second.
Marine cable product use
Submarine communication cables are mainly used for long-distance communication networks, usually between distant islands, cross-sea military facilities and other important occasions. The laying distance of submarine power cables is much shorter than that of communication cables. They are mainly used between land and islands, across rivers or harbors, connecting drilling platforms from land or connecting drilling platforms to each other. In general, the use of submarine cables to transmit electricity is undoubtedly more expensive than overhead cables of the same length, but it is often more economical than using small and isolated power stations for regional power generation, and it has more benefits in offshore areas. In countries with many islands and rivers, this type of cable is widely used.
Classification of marine cables
Since the development of submarine cables, various explorations and attempts have been made in structural design, mainly including the following types:
1. Impregnated paper-wrapped cable. Applicable to lines with AC not exceeding 45kV and DC not exceeding 400kV. Currently, it is only installed in waters with a depth of less than 500m.
2. Oil-filled cable. The air gap in the cable is eliminated by supplementing the impregnating agent. When the cable temperature rises, the impregnant expands, the pressure inside the cable increases, and the impregnant flows into the oil supply tank; when the cable cools, the impregnant shrinks, the pressure inside the cable decreases, and the impregnant in the oil supply tank flows into the cable again, preventing the generation of air gaps, so it can be used for 110 kV and above lines. It can be laid in water depths up to 500m.
3. Inflatable (pressure-assisted) cable. Inflatable cables using impregnated paper packages are more suitable for longer submarine cable networks than oil-filled cables, but because they must be operated under high air pressure in deep water, the difficulty of designing cables and their accessories is increased, and they are generally limited to water depths of less than 300m.
4. “Oil pressure” pipe cable. It is only suitable for cable systems of several kilometers in length, because there are great mechanical limitations to pulling extremely long cables into the pipeline.
5. Extruded insulation (cross-linked polyethylene insulation, ethylene propylene rubber insulation) cable. It is suitable for AC voltages up to 200kV. Ethylene propylene rubber can prevent tree branches and local leakage better than polyethylene, making submarine cables more effective.
Types and application scope of marine cables
Impregnated paper-wrapped cables are mainly used in AC lines less than 45kV and DC lines less than 400kV. The water depth of less than 500 is the current restricted installation water area; self-contained oil-filled cables are used in AC lines or DC lines up to 750kV. Because this type of cable is an oil-filled cable, it can be laid in sea areas with a water depth of up to 500m without difficulty. There are also extruded insulated cables and inflatable cables. Inflatable cables are also called pressure-assisted cables. They are inflatable cables using impregnated paper wraps. They are more suitable for relatively long submarine cable networks than oil-filled cables. Because they need to use high air pressure to operate in deep water, this undoubtedly increases the difficulty of designing accessories and cables, so they are now limited to use in sea areas with a water depth of less than 300m.
History of the development of marine cables
In 1850, the world’s first submarine cable was laid between Calais (France) and Dover (UK). In August 1858, a British private company founded by Cyrus Westfield completed the laying of the first intercontinental submarine communication cable between Ireland (Europe) and Newfoundland (North America).
Compared with land cables, submarine cables have many advantages: first, laying does not require digging tunnels or supporting with brackets, so the investment is small and the construction speed is fast; second, except for the landing area, most cables are on the seabed of a certain test, which is not damaged by natural environment such as wind and waves and interference from human production activities. Therefore, the cable is safe and stable, with strong anti-interference ability and good confidentiality performance.
In 1876, after Bell invented the telephone, new content was added to the submarine cable, and the pace of large-scale laying of submarine cables in various countries accelerated. The global submarine communication cable was completed in 1902.
In 1960, the world’s first laser came out, and people began to use the characteristics of laser transmission in optical fibers to transmit information.
32 countries and regions in the world have established the most modern global communication network through submarine optical cables, which can carry out 300,000 telephone calls or data transmission at the same time.
Submarine optical cables have also developed rapidly in China. The China-Japan submarine optical cable system built in 1993 can open 7,560 telephone circuits. In 1997, another FLAG optical cable was built in Nanhui, Shanghai, connecting 20 countries around the world and opening 120,000 telephone circuits. my country has begun to build two optical cables, China-US and Asia-Europe, and the total communication capacity will soar to 1.32 million lines.
Marine cable manufacturing method
The entire manufacturing process of submarine power cables is basically the same as that of general power cables, but there are some special requirements for the mechanical strength and anti-corrosion of the cables, and the cable length is required to be extended as much as possible. The following briefly describes the manufacturing process of impregnated paper cables and extruded insulated cables. Impregnated paper cables are first wrapped with insulating paper around the core, and then vacuum dried and oiled. After the conductor core is completed, it is wrapped with lead sheaths, and a continuous extrusion process is required at this time. Extrusion of extremely long cable cores is a very important step and must be carried out day and night. The conductor core of the oil-filled cable passes from the storage cylinder to the lead press through a siphon conveyor pipe, which is filled with degassing oil and flows in the opposite direction to the conductor core to isolate the conductor core from contact with the air. After the conductor core is wrapped with lead sheath, it needs to be coiled on a rotating platform (if the cable is oil-filled or air-filled, an appropriate amount of metal reinforcement can be added separately), and then the cable is wrapped with a polyethylene sheath (extrusion of polyethylene sheath is also a continuous operation), and finally wrapped with a two-layer armor of galvanized steel wire and covered with oil and hemp impregnation. In the final production process, the lead sheath and metal belt must be grounded through the polyethylene sheath at an appropriate stage. Most of the production processes of cross-linked polyethylene cables and EPDM insulated submarine cables are generally similar to the manufacturing process of paper-insulated lead-sheathed cables, except for the extrusion and vulcanization of the synthetic rubber insulation layer, but no lead sheath is used.
Marine cable laying methods
The laying of submarine cables mainly includes three stages: cable route survey and cleaning, submarine cable laying and burial protection. When laying cables, the water entry angle and laying tension of the cables should be controlled by controlling the navigation speed of the laying ship and the cable release speed to avoid damage to the cables due to too small bending radius or too large tension. Among them, when laying in the shoal section (Nanling side), the cable laying ship stops at 4.5 kilometers away from the coast, and the cable placed on the buoy is towed ashore by the tractor on the shore. After the cable is on shore, the buoy is removed and the cable sinks to the seabed. When laying in the deep sea section, the cable laying ship releases the cable, and uses underwater monitors and underwater remote control vehicles to continuously monitor and adjust, control the forward speed, direction and speed of the laying ship, and lay the cable, so as to bypass uneven places and rocks to avoid damage to the cable.
In the final stage of construction, the main thing is to bury the submarine cable deeply to reduce the impact of the complex marine environment on the submarine cable and ensure safe operation. In sandy and silty areas, high-pressure water is used to create a trench about 2 meters deep, and the cable is buried in it, and the sand and soil next to it cover it; in coral reefs and clay areas, a 0.6-1.2-meter-deep trench is cut with a cutting machine, and the cable is buried in the trench, and naturally backfilled to form protection; in hard rock areas, the cable needs to be covered with cement covers and other hard objects for protection.
Development prospects of marine cables
Submarine cables are products that implement the export quality licensing system. Manufacturers must obtain export quality licenses issued by the national entry-exit inspection and quarantine department in accordance with regulations before they can produce export products.
At present, there is no direct communication optical cable connection between the mainland of my country and Taiwan Island. Generally, information is exchanged through the submarine optical cable of the United States. The global Internet in the world is realized through submarine communication optical cables. The “Pacific Highway” submarine optical cable system currently being prepared will reach a length of 25,000 kilometers, connecting China, the United States, Japan, South Korea and many other Pacific countries.
In 1866, the transatlantic submarine cable was successfully laid, realizing transatlantic telegraph communication between the European and American continents. Today, with the development of social economy and science and technology, there are more and more types of submarine pipelines. According to their uses, submarine pipelines can be simply divided into oil pipelines, gas pipelines, water pipelines, etc.; submarine cables mainly include communication optical cables, power transmission cables, communication cables, etc.
Explore the infinite possibilities of the deep sea and start by choosing our marine cables. Designed for extreme submarine environments, our cable products combine the latest technological innovations with environmental protection concepts to ensure excellent performance and long-term reliability. TST CABLES is made of high-strength, corrosion-resistant materials to ensure efficient transmission of data and power even in the harshest marine conditions. The unique shielding technology effectively resists external electromagnetic interference and provides a stable and error-free data stream to meet the needs of modern marine observation networks, offshore wind farms, oil and gas exploration and other fields.
In addition, TST CABLES pays attention to environmental protection. All cables meet international environmental standards, are low-smoke, halogen-free and flame-retardant, and reduce the impact on marine ecology. The flexible design makes installation and maintenance easier and significantly reduces operating costs. Choose TST CABLES customized marine cables and join hands to open up a new world of marine resource development and utilization. If your equipment requires marine and ship cables, please email us immediately to get more quotes and samples!
Also available in:
English