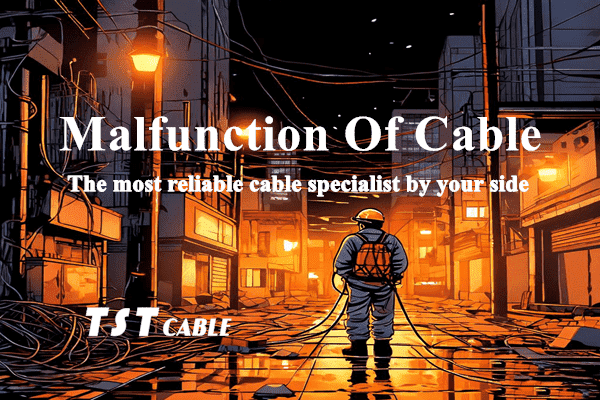
In order to ensure the quality and safety performance of wire and cable, cable manufacturers should be strictly in accordance with the relevant standards and regulations for production, testing and packaging processing. At the same time, enterprises in the purchase and use of wire and cable should also pay attention to product identification, mechanical properties, insulation thickness, conductor resistance and other key indicators to ensure the safety of electricity.
First, wire and cable common problems:
- Mechanical properties: mainly in the wire tensile force and bending force is not enough. If the mechanical properties of wire and cable do not meet the standards, may have an impact on the actual use of power cables, and may shorten their service life.
- Product identification problems: many manufacturers in the packaging and processing of wire and cable, may not be in accordance with the standard requirements of scientific settings product identification, resulting in product identification of the wrong specifications or the use of the scope is not clear, causing inconvenience to the user, and may cause potential safety hazards.
- Loss of weight problem: If the loss of weight test results of the wire and cable do not meet the relevant standards, it will lead to more likely than the quality of the wire and cable up to the standard of aging, resulting in more serious quality problems. Loss of weight problems may be due to the quality of the test cycle is long, manufacturers omit part of the test link or raw material quality is not qualified and other reasons.
- Insulation layer problem: wire and cable outer layer usually have insulation layer, insulation layer quality problems generally appear in the thickness of whether to meet the standard. If the thickness of the insulation layer is insufficient, it will lead to the wire can not be sufficient protection, thus reducing the use of safety.
- Conductor resistance problem: the wire conductor resistance setting has a clear standard requirements, resistance is the determination of the wire transmission properties of the key indicators. When the resistance measurement is not up to standard, it will lead to obstacles in the transmission of electrical energy.
- Structural problems: These include insulation thicknesses below the minimum value specified in the standard or average thicknesses below the nominal value, which may lead to the risk of cable breakdown during use.
- Cross-linking problems: If the cross-linking degree is not up to standard, the cable’s heat resistance may not be qualified to meet the requirements of the operating temperature, which leads to a significant reduction in electrical performance.
- Appearance problems: such as uneven cable thickness and bamboo shape, these problems may lead to uneven heating of the cable, thus affecting the life of the insulation. In addition, the cable may also be scratched by foreign objects during transportation or laying, so be sure to check whether the cable insulation is intact before use.
Second, how to determine whether the quality of wire and cable is qualified?
High-temperature cable manufacturer TST CABLES suggests that you can consider the following aspects:
Appearance check:
Observe whether the surface of the insulation layer of the wire and cable is smooth, with or without bubbles, impurities or cracks.
Check whether the copper core is glossy, with or without scorched or blackened phenomenon.
Check whether the thickness of the sheath is uniform and whether the color is bright.
Material Selection:
Conductor material:
Pure copper is the commonly used conductor material in wire and cable, which is widely used because of its excellent conductivity and ductility.
Insulation material:
Polyethylene (PE): has good electrical properties and heat resistance, suitable for high temperature environment and submarine cables and other occasions.
Cross-linked polyethylene (XLPE): excellent heat resistance and electrical properties, widely used in high-voltage power transmission and distribution systems.
Silicone rubber: high temperature resistance and good weather resistance, suitable for power equipment and lines in high and low temperature environments.
Other auxiliary materials:
In addition to conductors and insulation materials, high-quality cables may also contain auxiliary materials such as sheaths, fillers, shields, etc., to enhance the mechanical strength, moisture and water resistance and electromagnetic shielding of the cable.
Feel & Sound:
Feel the softness and elasticity of the wire by repeatedly bending it, and high-quality wires should feel soft and elastic.
Electrical performance testing:
Measure the resistivity of the conductor, the resistivity of qualified products should meet the relevant standards, such as greater than or equal to 0.5mΩ-km.
Insulation resistance test and voltage resistance test to ensure the electrical safety of wire and cable in use.
Mechanical performance test:
Conduct tensile test to check the toughness and strength of the wire.
Evaluate the mechanical properties of the wire by bending test and impact test.
Combustion Performance Test:
Observe the performance of wires and cables when burning, such as whether they ignite easily and whether they burn with dense smoke or produce harmful gases.
Check whether the wire has flame retardant properties, i.e. whether it can self-extinguish after leaving the source of ignition.
Check product markings and supporting documents:
Check whether there are clear product markings on the wires and cables, including information on the manufacturer, specification model and voltage level.
Ask the supplier to provide relevant quality certification documents and test reports.
After-sales service and brand reputation:
Choose suppliers with well-known brands and good after-sales service to ensure that problems with wire and cable can be solved in time.
To determine whether the quality of wire and cable is qualified, we need to consider the appearance, feel, electrical properties, mechanical properties, combustion properties and product marking and other aspects. At the same time, the choice of reputable brands and suppliers is also an important factor to ensure the quality of wire and cable.
The above is the common quality problems of wire and cable, and how to determine the quality of wire and cable is qualified some suggestions, in order to ensure the safety of your equipment wire and cable must be used with qualified products, such as the use of TST CABLES!
TST CABLES is a focus on high-temperature wire and cable production and sales manufacturers, the main production: high and low voltage cross-linked power cables, mineral fire cables, high temperature cables, control cables, overhead conductors, flame retardant, fire-resistant cables, low smoke halogen-free cables, pre-fabricated branch cables, shielded cables, high-temperature cables, environmental protection cables and a variety of special cable products, the company has imported production equipment and testing equipment, as well as strong technical force, with strong new product development capabilities, welcome to consult and cooperate.
Also available in:
English