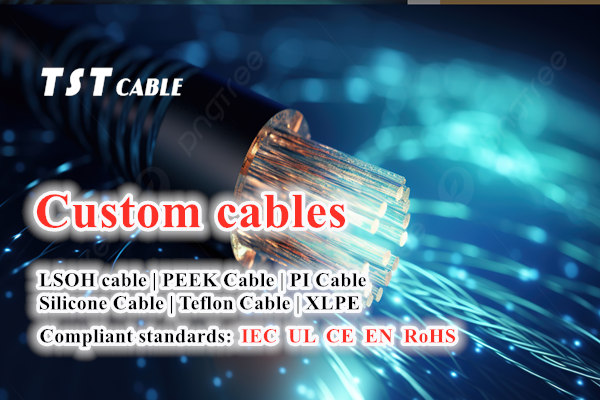
Introduction to Low Voltage Cables
Low-voltage cables are conductors designed for the transmission of electrical or signal currents and voltages, with operating voltages usually between 0.01kV and 1kV (inclusive), and are widely used in power distribution and control circuits in homes, commercial buildings, industrial facilities and other locations. Low-voltage cables play a vital role in the power system, especially as part of the distribution network, responsible for delivering power from the main switchboard or transformer to individual power-using devices.
Low-voltage cable is used to transmit power or signal current, signal voltage is covered with insulation, protective layer, shielding layer and other conductors. According to the voltage points can be high-voltage cables and low-voltage cables. Low-voltage cable lines and low-voltage overhead lines, low-voltage overhead insulated lines compared to the higher cost, laying and maintenance is more difficult, but because it has a reliable operation, does not set up poles, does not occupy the ground, does not impede the appearance of the outside world by the influence of the smaller and so on, and in the low-voltage power distribution system is widely used.
Low-voltage cable structure
Generally consists of three parts: core, insulation and protective layer. The core is used to conduct current, and is generally made of strands of copper wire or aluminum wire. Low-voltage cables are single-core, double-core, three-core, four-core and other types. Dual-core cable for single-phase lines, three-core and four-core cable for three-phase three-wire lines and three-phase four-wire lines, single-core cables can be applied to single-phase lines or three-phase lines as needed. Commonly used low-voltage cable core cross-sectional area of 10, 16, 25, 35, 50, 70, 95, 120, 150, 185, 240 mm and so on.
Low-voltage cable structure
Core: the central part of the low-voltage cable is the conductive core, usually composed of multi-stranded stranded copper or aluminum wire, copper wire for its good conductivity and corrosion resistance and more often used. The multi-stranded design improves the flexibility and current-carrying capacity of the cable.
Insulation: The core is surrounded by an insulating layer, usually made of PVC (polyvinyl chloride), PE (polyethylene), rubber or a special composite material, which prevents the leakage of current and protects the core from the external environment, while keeping the potential inside the cable isolated.
Protective Layer: In addition to the insulation, some types of LV cables have an additional protective layer, such as a PVC jacket or metal armor, to increase the mechanical strength of the cable, to prevent physical damage, and to provide resistance to corrosion in certain environments.
Shield (optional): For signal cables that need to be anti-interference, a metal braid or foil layer will be added as a shield to reduce electromagnetic interference and ensure clear signal transmission.
Low-voltage cable features
Low-voltage cables are widely used in low-voltage power distribution systems because they are reliable in operation, do not erect poles, do not occupy the ground, are not an eyesore, and are less affected by the outside world.
Low-voltage cable insulation
Insulating materials in cables that have the specific function of withstanding voltage. Insulation is divided into two kinds of core insulation and tape insulation: the insulation on the core is called core insulation; multi-core cable insulation core together and then add the insulation is called tape insulation. Band insulation and the protective layer to form a reliable insulation to ground. Insulation is usually made of oil-impregnated paper, plastic, rubber and so on.
(1) Paper insulated cable is impregnated by the cable paper as the insulating layer of the cable, always called paper insulated cable. According to the case of paper impregnation can be divided into: ① oil-impregnated paper-insulated cable; ② dry insulated cable; ③ non-drip cable.
(2) insulation layer made of thermoplastic extruded cross-linked cable, always called plastic cable, widely used. Plastic cables can be divided into PVC cables, polyethylene cables and cross-linked polyethylene cables and other three. With natural styrene butadiene rubber, butyl rubber and ethylene-propylene rubber and other materials for the insulation layer of the cable is called rubber cable. Voltage level of 1 kV of low-voltage cables can be used paper-insulated cables and plastic cables, more plastic cables; voltage level of 0.5 kV of low-voltage cables more rubber cables.
Low-voltage cable protective layer
Cable outside of one or more layers of metal or non-metallic materials covering layer. The protective layer is used to protect the insulation layer in the transportation, laying and use process, from external damage and moisture intrusion.
(1) paper insulated cable protective layer. Paper-insulated cable protective layer is divided into two parts, the inner and outer protective layer. Inner sheath directly extruded on the insulation layer, in addition to protecting the insulation from moisture, but also to prevent the role of insulation oil outflow, and has a certain degree of mechanical strength. The inner protective layer has a lead package, aluminum package and polyvinyl chloride package three kinds. The outer sheath is to protect the inner sheath, in order to increase the cable to withstand mechanical external forces and corrosion resistance. The outer sheath includes the inner liner layer, metal armor layer and outer being layer. The inner liner layer protects the metal sheath from being damaged by the metal armor layer, which can be attached to anti-corrosion measures; the metal armor layer can withstand mechanical external forces.
(2) Plastic cable protection. Usually in the plastic insulation outside the polyvinyl chloride sheath.
(3) rubber cable protective layer. Rubber cable protective layer is divided into the inner and outer sheath. Inner sheath has a polyvinyl chloride sheath, neoprene rubber sheath (non-flammable rubber) and lead package of three kinds; outer sheath is divided into steel armor, rubber sheath and plastic sheath three kinds.
Low-voltage cable classification
According to the voltage level
According to the voltage level can be divided into medium and low-voltage power cables (35 kV and below), high-voltage cables (110 kV and above), ultra-high-voltage cables (275-800 kV) and ultra-high-voltage cables (1000 kV and above). In addition, they can be divided into AC cables and DC cables according to the current system.
According to the insulation material
- oil-impregnated paper-insulated power cables to oil-impregnated paper as the insulation of power cables. Its application history is the longest. It is safe, reliable, long service life, low price. The main drawback is that the laying of the drop restrictions. Since the development of non-drip paper-immersed insulation, to solve the problem of fallout restrictions, so that oil-impregnated paper-insulated cables to continue to be widely used.
- Plastic insulated power cables Insulation layer of extruded plastic power cables. Commonly used plastics are polyvinyl chloride, polyethylene, cross-linked polyethylene. Plastic cable structure is simple, easy to manufacture and process, light weight, easy to lay and install, not subject to the restrictions of laying the fall. Therefore, it is widely used for low and medium voltage cables, and there is a trend to replace the viscous impregnated oil paper cable. The disadvantage is the existence of dendritic breakdown phenomenon, which limits its use at higher voltages.
- Rubber insulated power cables Insulation layer of rubber plus a variety of agents, after sufficient mixing and extrusion package in the conductive core, after vulcanization and temperature. It is soft, flexible, suitable for frequent movement, laying of small bending radius occasions.
Commonly used for insulation rubber material has natural rubber – butyl rubber mixture, ethylene propylene rubber, butyl rubber, etc..
According to the voltage level
- Low-voltage cable: suitable for fixed laying in AC 50Hz, rated voltage 3kv and below on the transmission and distribution lines for the transmission of electrical energy.
- Medium and low voltage cables: (generally refers to 35KV and below): PVC insulated cables, polyethylene insulated cables, cross-linked polyethylene insulated cables and so on.
- High-voltage cables: (generally 110KV and above): polyethylene cables and cross-linked polyethylene insulated cables.
- Ultra-high voltage cables: (275-800KV).
- Extra-high-voltage cables: (1000KV and above).
Low-voltage cable advantages
Low-voltage power cable itself can be relied upon, stealth and other characteristics, suitable for laying in a variety of places; and is not easy to suffer from the external weather and other elements of the impact of the use of strong performance, reducing the cost of construction and maintenance costs of electric power installation projects.
Low-voltage cable line
Low-voltage lines using cables. Cable by the core, insulation, protective layer. There are many types of cables, low-voltage cable lines are mainly used for low-voltage power cables.
Low-voltage cable lines commonly used laying methods are: ① directly buried; ② laid in the cable trench; ③ laid along the wall; ④ laid in cable tunnels and so on. Low-voltage power cable models are mainly based on the use of environmental conditions and laying methods for selection. Low-voltage cable lines and low-voltage overhead lines, low-voltage overhead insulated lines compared to the higher cost, laying and maintenance is more difficult, but because it has a reliable operation, does not set up poles, does not occupy the ground, does not impede the appearance of the outside world by the influence of the smaller and so on, and the low-voltage power distribution system is widely used. Low-voltage cable lines are mainly used for power supply reliability (see power supply quality) requires high corrosive gases and flammable, explosive, etc. should not be erected low-voltage overhead lines or low-voltage overhead insulated lines.
Low-voltage cable model specifications
YQ:Light rubber cable;
YZ: medium-sized rubber cable;
YC: heavy duty rubber cable;
VDZAN-YJY23:low voltage halogen-free armored cable;
ND-YJY:cross-linked polyethylene insulated halogen-free low-smoke flame-retardant polyolefin sheathed power cable;
YV:cross-linked polyethylene insulated polyvinyl chloride sheathed power cable;
V:PVC insulated PVC sheathed copper core.
Power cables in the general environment, you can choose aluminum-core cables, in places with special requirements, choose copper-core cables, buried in the ground, to choose the armored cables, no mechanical damage to the site, you can choose the plastic sheathed cables, when the buried soil is corrosive, to choose corrosion-resistant cables.
Low-voltage cable technical standards
“The technical standards for low-voltage power cables include conditions of use, performance parameters, technical requirements, testing, packaging, transportation, storage and so on. Applicable to AC discharge voltage 11 and below polyethylene, PVC, cross-linked polyethylene insulated low-voltage wire and cable. Regulation references include IkV and the following wire and cable conditions of use, performance parameters, technical requirements, testing, packaging, transportation, storage and so on. The latest version applies to this regulation.
Low-voltage cable use
Low-voltage cable is used for transmission and distribution of electrical energy cables, commonly used in urban underground power grid, power station lead lines, industrial and mining enterprises, internal power supply and underwater transmission lines across the river and the sea.
- in general environment and place is suitable to use aluminum core cable, but in the vibration of intense and special buildings and special requirements of the place, should be used copper core cable; 2. buried cable, generally used with the outer shell of the armored cable. In places where no mechanical damage is possible, also, plastic sheathed cables and lead (aluminum) clad cables with outer sheath can be used;
- In the chemical corrosion or stray current corrosion in the soil, should try not to use buried cable. If it must be buried should be used when the anticorrosive type cable;
- Laying in the pipe or row of cables in the pipe, the general use of plastic sheathed cable, can also be used * armored cable;
- in the cable trench or cable tunnel laying of cables, should not be used with flammable or flame retardant outer layer. The general use of * armored cable, plastic sheathed cable and lead (aluminum) covered cable;
- When the cable is laid in places with large height differences, it is appropriate to use plastic insulated cables, non-drip cables and dry insulated cables.
Commonly used low-voltage cable
- copper conductor power cables: the current domestic low-voltage power cables are stranded together for the core into a cable, this structure of the cable anti-interference capability is poor, lightning performance is also poor, the cable’s three-phase impedance imbalance and zero-sequence impedance is large, it is difficult to make the line to protect the appliance reliably action. Jiangsu Baosheng Cable Factory developed a rated voltage of 1kv and the following copper, aluminum PVC copper core conductor power cables to solve the above problems.
2 cross-linked polyethylene insulated power cables: referred to as XLPE cable, it is the use of chemical or physical methods to make the cable insulation material polyethylene plastic molecules from the linear structure into a three-dimensional mesh structure, that is, the original thermoplastic polyethylene into a thermosetting crosslinked polyethylene plastic, which significantly improves the cable’s heat resistance and service life, but still maintains its excellent electrical properties.
- PVC insulated PVC sheathed power cables: PVC insulated PVC sheathed power cables long-term operating temperature does not exceed 70 ℃, the maximum temperature of the cable conductor does not exceed 160 ℃. The longest duration of the short circuit does not exceed 5s, the minimum temperature of construction and laying shall not be less than 0 ℃.
Low-voltage cable maintenance
Low-voltage power cables need to be serviced even after a long time of use. Otherwise, if it causes electrical energy leakage, a big accident may occur. In fact, the daily overhaul of this cable product is also very simple, because all of our products are made under a specific model. When we are testing, all of us just need to follow the same model for overhauling. In the police school, we have to pay attention to check the insulation of the outer layer of the cable of the product. If there is any damage or oxidization, it should also be dealt with in time to avoid major accidents. If necessary, check the joints of the power cable according to the low-voltage power cable product model, and reinforce them in time if they are loose.
Low-voltage power cable can withstand the impact of some mechanical external forces to a large extent, because it has very good flexibility and bending characteristics, so even if it is frequently moved and twisted in the process of use, its quality will not be affected. Because he works in a special place, but also because of some environmental factors, we have higher requirements for her overall softness and bending properties. When we install low-voltage power cables, we first need to pay attention to not let it be scratched by some sharp substances. Because once scratched, it may shorten his overall service life.
Low-voltage cable faults
The first type of fault: the whole cable is burned off or individual phases are burned off, such faults cause serious damage to the cable at the point of failure.
The second type of fault: all phases of the cable are short-circuited, again, this type of fault caused by the cable at the point of failure damage is also very serious.
The third type of fault: the cable is shorted only one phase, the point of failure damage is light but the surface is obvious.
The fourth type of fault: cable internal short circuit, the appearance of traces can not be seen, such faults are generally caused by the quality of the cable.
Enterprises, units and some small and medium-sized cities, county-level power supply bureaus, low-voltage cable fault resolution is their primary concern. At the same time, the total number of low-voltage cables is much larger than the number of high-voltage cables, but there is currently no one on the market for low-voltage cable fault characteristics and the development of fault testers, the so-called low-voltage cable fault testers are still “flash method” based on the “high-voltage impact,” which is just a “high-voltage impact “The power of the equipment is reduced.
Fault solution
The following is the solution to low-voltage cable faults
The first step: first use the distance meter to measure the distance. In fact, the first to determine whether the cable fault is high resistance or low resistance or grounding, according to this condition using different testing methods. If it is a grounding fault, it is directly with the rangefinder’s low-voltage pulse method to measure the distance; if it is a high-resistance fault should be used to measure the distance of the high-voltage impact discharge method, high-voltage impact discharge method to measure the distance of many auxiliary equipment: such as high-voltage pulse capacitance, discharge ball, current-limiting resistors, inductive coils, as well as signal sampling device, etc., the operation of both trouble and insecurity, with a certain degree of risk, more What is even more annoying is to analyze the sampling waveform, the tester’s knowledge requirements are relatively high.
Step 2: Find the path (if the path is clear this step can be omitted). In finding the path, to add a signal to the cable (path signal generator), and then use the receiver to receive the signal, along the path of the signal once, the path of the cable is determined. However, the range of this path should be roughly between 1-2 meters, not particularly accurate.
Step 3: Accurately locate the cable based on the measured distance. It is based on the sound generated by the firing discharge, and when the largest sound is heard from the earphones of the pinpointing instrument, the location of the fault point is found. However, because it is listening to the sound, so, affected by the environmental noise, it is quite time-consuming to find, sometimes until the night. When encountered cross-linked cable, it is even more time-consuming, because, cross-linked cable is generally internal discharge, the sound is very small, almost inaudible, and finally only DD.
Therefore, this method can be used to solve most of the oil infiltrated paper as insulation materials for power cable faults, for the emergence of cross-linked materials and polyethylene materials as insulation materials for cable faults in recent years, the test effect is not too ideal, the reason is that the fire discharge produced by the sound is often very small (no damage to the cable sheath, only the cable internal discharge), encountered in this case, it is only with other methods to Solve the problem.
Although there are such shortcomings, but the “flash method” principle designed into the cable fault tester for a long time for the enterprise to solve a lot of cable faults. With the rapid development of various industries, the use of cables is more and more extensive, the types of cables are also increasing, so that cable failures continue to occur is a necessity. Various industries on the level of the cable used, the use of the environment, wiring and distribution of the way, the insulation requirements are different, different cable cable fault characteristics are also very different, the reason is that the cable failure factors have many aspects, can be at present people due to the habit of the previous, always want to solve all the cable faults in a way, so the market is still to” flash method” as the principle. Flash method” as the principle of designing the cable fault tester dominates the market.
High-voltage cable and low-voltage cable faults have many differences, high-voltage cable faults are mainly running faults, and most of the high-resistance faults, and high-resistance faults are divided into two major types of leakage and flashing; while the low-voltage cable faults are only open-circuit, short-circuit and circuit-breaking three cases (of course, high-voltage cables, including these three cases).
Low-voltage cable and high-voltage cable difference
I. Different voltage levels
In China’s power industry, the common voltage levels are 220V, 380V, 1kV, 10kV, 350kV, 110kV, 220kV, 500kV and so on. Generally considered 220V, 380V for low voltage, mainly for household electricity; 35kV or more for high voltage, mainly for power transmission; in between, medium voltage.
II. Cable structure is different
High-voltage cable layers, from the inside out, including: conductor, insulation, inner sheath, filler (armor), outer insulation; low-voltage cable from the inside out, respectively: conductor, insulation, steel, sheath (many low-voltage cables do not have steel).
High-voltage cable and low-voltage The main difference is that the high-voltage cable than the low-voltage cable more semiconductor layer and shielding. Therefore, high-voltage cables are much thicker than low-voltage cable insulation, and the structure is complex, the process requirements are also high.
Three. Different uses
High-voltage cable is mainly used in the power sector for power transmission, substation voltage level change. We commonly used voltage levels are below 220KV, long-distance transmission of electricity voltage levels are ultra-high voltage, are designated by the power sector specialized power workers construction, specialized maintenance.
Low-voltage cable for voltage 450V/750V below the electrical equipment, the use of a wide range of classifications are also many. General industrial plastic insulated cables for fixed laying; mobile rubber low voltage insulated cables; building installation is mainly used for power supply circuit, the trunk branch, branch road laying, but also for elevator installation of special flat elevator cable.
IV. Production process
Low-voltage cable using ordinary PVC and cross-linked polyethylene can be produced, low-voltage cables have ordinary and cross-linked two kinds. Medium and high voltage cables are only cross-linked cables, 6kV-35kV are produced using three-layer co-extruded, high-density cross-linked polyethylene.
The world’s leading manufacturer of low voltage cables TST cables
TST CABLES low voltage cables are crafted for safe and efficient energy transmission. High purity conductors are selected and new environmentally friendly insulating materials are precisely blended to safeguard the purity and safety of each and every electrical energy. TST CABLES is not just a cable, but also our persistent pursuit of a high quality of life, so that the power connection is more stable and life is better. If your industry has low voltage cables, medium voltage cables, high voltage cables, you can send an e-mail to contact us, we can provide free samples.
Also available in:
English