
Teflon procession
Support Global standards
- Customized Design Production
Small MOQ
Short Lead Time
- Long Time Guarantee
- Home
- /
- High Temperature Cable...
High temperature cable | Teflon wire & cable
An accidental discovery changed the course of human social development
History of Teflon
Teflon in a narrow sense
In the early days, Teflon referred to polytetrafluoroethylene, which was accidentally discovered by chemist Dr. Roy J. Plunkett in DuPont’s New Jersey laboratory in 1938. When he tried to make a new chlorofluorocarbon refrigerant, polytetrafluoroethylene polymerized in a high-pressure storage container (the iron on the inner wall of the container became a catalyst for the polymerization reaction). DuPont obtained its patent in 1941 and registered the trademark under the name “Teflon” in 1944. From then on, everyone called it Teflon etc., are all transliterations of “Teflon”.
Teflon is a revolutionary material with a history full of innovations and technological breakthroughs. Scientists describe the invention of PTFE as “a coincidence, a flash of inspiration, a lucky accident – or even a mixture of the three.” Whatever the case, one thing is certain: PTFE has revolutionized the plastics industry and spawned endless applications that benefit mankind.
- 1938: Roy J. Plunkett, a chemist at DuPont, accidentally discovered PTFE while studying refrigerants.
- During World War II: PTFE was used for military purposes due to its excellent chemical inertness and electrical insulation, such as as an insulation material in the Manhattan Project of the atomic bomb.
- Commercialization: In 1945, DuPont began to commercialize PTFE and named it Teflon. The initial applications were mainly concentrated in the industrial field, such as linings and anti-corrosion coatings for chemical equipment.
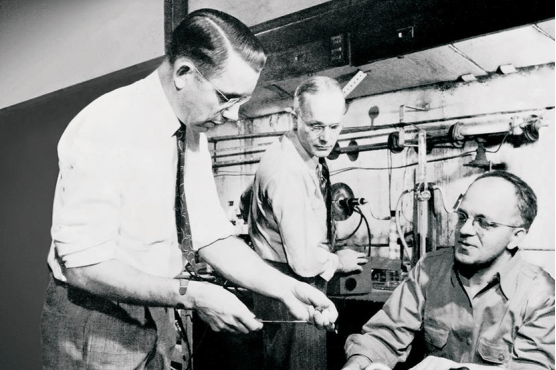
- 1950s: With the advancement of technology, PTFE began to be used in more fields, such as cookware coatings, because of its non-stick properties and easy cleaning.
- 1960s: PTFE was introduced into textiles to make waterproof and breathable fabrics, such as Gore-Tex.
- 1970s: PTFE was used in the medical field, such as vascular grafts and surgical sutures.
- 1980s to present: The application scope of PTFE continues to expand, including automobiles, aviation, construction, electronics and other industries.
Teflon in a broad sense
Subsequently, DuPont developed a series of products in addition to Teflon polytetrafluoroethylene resin. Therefore, Teflon now refers to the fluoroplastic family products, including PTFE (polytetrafluoroethylene), ETFE (ethylene-tetrafluoroethylene copolymer), FEP (fluorinated ethylene propylene copolymer), PFA (perfluoroalkyl compound) and PVDF (polyvinylidene fluoride), etc.
These Teflon materials are widely used in various industries due to their excellent high temperature resistance, chemical corrosion resistance and electrical insulation performance. It has a series of unique properties and advantages, which make it surpass other plastic materials in many aspects, so Teflon has the reputation of “King of Plastics” and has excellent high temperature resistance (temperature resistance: -200℃~+260°C). Teflon is widely used in many industrial fields, such as chemical industry, rail transportation, energy, aviation, automobile and medical equipment.
High temperature Teflon cable industry application
Due to the excellent performance of Teflon cables, they are widely used in the following industries:
- Aerospace: Suitable for ultra-high temperature wires in aircraft and spacecraft.
- Petroleum industry: As winding wires and connecting wires for submersible pump motors, they maintain performance under extreme temperatures.
- Nuclear power plants: Winding coils used for nuclear island drive mechanisms, which can be used for a long time under irradiation conditions.
- Shipbuilding industry: Seawater resistance and lightweight design make it widely used in ships.
- High-speed traction locomotives: Suitable for high-speed trains and other transportation equipment.
- Automobile manufacturing: Suitable for automotive electronic systems.
- Natural gas: Used in antenna sleeves, valve seats, electrical connectors, etc., capable of handling extreme temperatures and high pressure environments.
- Semiconductors and electronics: Teflon is used as an electrical insulating material and mechanical component for semiconductor production and electronic equipment.
- Food processing: Teflon’s non-stick and easy-to-clean properties make it suitable for food contact applications.
- Medical equipment: Used for cables that require high purity and low signal interference, such as MRI machines and X-ray equipment.
- Military and defense: Used for communications and control systems in harsh environments.
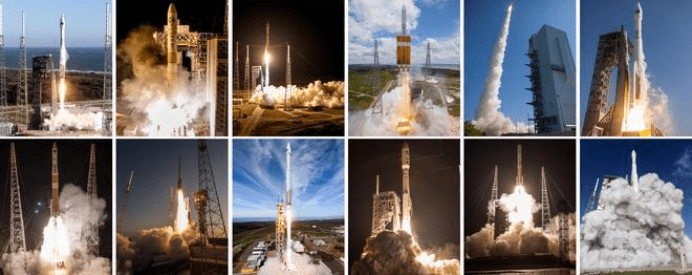
High temperature Teflon cable structure
- Conductor: Copper or silver-plated copper conductors for efficient transmission of power or signals.
- Insulation: One or more of the above mentioned Teflon materials, providing electrical insulation and protection.
- Jacket: Some cables may also include an additional jacket of Teflon or other materials for increased mechanical and environmental protection.
- Shield: Cables may include a metal braid or foil shield where it is necessary to reduce electromagnetic interference.
Technical Parameters
- Operating temperature: -200°C to +260°C
- Insulation material: Teflon (PTFE)
- Conductor material: Bare copper or silver-plated copper-nickel
- Insulation thickness: Depends on cable specifications and standards
- Flame retardant rating: Meets UL1581 standard
Special properties and advantages of high temperature Teflon cables
Special properties
- High and low temperature resistance: Teflon materials have a wide temperature resistance range, from low temperature -200°C to high temperature above 260°C, and can maintain good physical and electrical properties even at extreme temperatures.
- Chemical corrosion resistance: Teflon materials have excellent resistance to most chemicals, including acids, alkalis, solvents, etc., which allows cables to be safely used in harsh environments such as the chemical industry.
- Low friction coefficient: Teflon has an extremely low friction coefficient, which means that dirt and corrosive substances are not easily attached to the surface of the cable, making it easy to clean and maintain.
- High dielectric strength: Teflon cables have high dielectric strength and can withstand high voltage without breakdown, making them suitable for high-voltage power transmission and signal transmission.
- Non-stickiness: Teflon’s non-stickiness reduces the possibility of cable accumulation of contaminants during use, especially in applications in the food processing and pharmaceutical industries.
- UV and radiation resistance: Teflon materials have good UV and radiation resistance, making them suitable for cable applications in outdoor and high-radiation environments.
High temperature Teflon cable material characteristics and temperature range
The high temperature resistance range of Teflon varies depending on the model, thickness and processing method. Generally speaking, Teflon can withstand the following temperatures:
1. Short-term temperature resistance: around 260°C (430°F).
2. Long-term temperature resistance: In actual applications, Teflon can usually withstand temperatures up to 260°C (430°F), but long-term use at this temperature may cause material aging and performance degradation.
- Polytetrafluoroethylene (PTFE): PTFE is a highly stable fluoropolymer with short-term temperature resistance up to 260°C and long-term use temperature range of -196°C to 260°C (430°F).
- Tetrafluoroethylene-perfluoroalkoxy vinyl ether copolymer (PFA): PFA is similar to PTFE, but has a lower melt viscosity, making it easier to process into complex shapes. PFA has an operating temperature range similar to PTFE, but has better mechanical strength at high temperatures.
- Fluorinated ethylene propylene copolymer (FEP): FEP also has good high temperature and chemical resistance and an operating temperature range of about -200°C to 200°C.
- Cross-linked polytetrafluoroethylene (XLETFE): PTFE has mechanical strength and heat resistance enhanced by chemical cross-linking, and its temperature range is similar to PTFE.
- Ethylene-tetrafluoroethylene copolymer (ETFE): ETFE has high wear and tear resistance and an operating temperature range of about -70°C to 150°C, but some special grades of ETFE can withstand higher temperatures.
- Ethylene chlorotrifluoroethylene copolymer (ECTFE): ECTFE has good chemical resistance and mechanical strength, and the operating temperature range is about -65°C to 150°C.
- Polyvinylidene fluoride (PVDF): PVDF has excellent weather resistance and chemical corrosion resistance, and the operating temperature range is about -46°C to 150°C.
Performance table of various fluoroplastics
The high temperature resistance range of Teflon varies depending on the model, thickness and processing method. Generally speaking, Teflon can withstand the following temperatures:
1. Short-term temperature resistance: around 260°C (430°F).
2. Long-term temperature resistance: In actual applications, Teflon can usually withstand temperatures up to 260°C (430°F), but long-term use at this temperature may cause material aging and performance degradation.
The difference between LSZH cable and ordinary PVC cable
Fluoroplastic properties | ||||||||
performance | ASTM/Unit | PTFE | FEP | PFA | ETFE | ECTFE | PVDF | PCTFE |
Mechanical properties | ||||||||
Relative density | D792 | 2.18 | 2.15 | 2.15 | 1.74 | 1.68 | 1.77 | 2.13 |
Elongation at break/% | D638 | 200~~450 | 250~330 | 280~400 | 420~~460 | 200~300 | 300~450 | 150 |
Tensile Strength/MPa | D638 | 14~48 | 19~35 | 28~31 | 42~~47 | 41~~54 | 31~43 | 36.5 |
Bending Strength/MPa | D790 | not break | not break | not break | 38 | 48 | 59~66 | 59 |
Compression strength/MPa | D695 | 24 | 15 | 17 | 8. 8~~12 | 8.8~12 | 80 | 38 |
Tensile modulus of elasticity (Young’s modulus)/MPa | D638 | 393 | 345 | 500~~600 | 586~655 | 1655 | 1103 | 1427 |
Flexural modulus/MPa | D750 | 490~~586 | 538~~634 | 648~-682 | 883~~1179 | 1655 | 621~1158 | 1241 |
Hardness (Shore D) | D636 | D50~~65 | D5S | D55~60 | D7S | D75~90 | D75~85 | D90 |
Friction coefficient | Relative Example | 0.02 | 0.05 | 0.2 | 0.06 | 0.19 | 0.4 | — |
Wear resistance 1000 times | Taber | 12 | 14~~20 | 9~17 | 0.005 | 5~15 | ||
lzod notched impact strength (23°C)/(kJ/amp) | D256 | 6.3 | not break | not break | not break | not break | 8.4 | 10.5 |
Thermal properties | ||||||||
Melting point/℃ | 327 | 260 | 305 | 267 | 240 | 171 | 212 | |
Maximum continuous operating temperature (20000h)/℃ | 260 | 200 | 260 | 150 | 150~170 | 129 | 132 | |
Flame retardancy (UL94) | V-o | V-o | V-o | V-o | V-O | V-o | V-0 | |
Linear expansion coefficient (D696)/(×10-3℃-1) | >11.6 | 8.3-~10.5 | 13 | 13 | not break | 4.2 | 7.0 | |
Brittle temperature/℃ | -268 | -268 | 268 | 100 | -76 | -62 | 240 | |
Electrical properties | ||||||||
Dielectric constant | (D150,101Ha) | 2.1 | 2.1 | 2.1 | 2.6 | 2.5 | 7.72 | |
(DI50.10*Hz) | 2.1 | 2.1 | 2.1 | 2.6 | 2.59 | 6.43 | ||
Dielectric strength (0.254unm static film) / (kV/mm) | (D149) | >1400 | >2000 | >2000 | 1600 | — | >1080 | |
Volume resistivity | (T257) | >101* | >101 | >1018 | >104 | >104 | 2×1014 | 101* |
Surface resistivity | (D257) | >10U | >101T | >10Ir | >104 | 10i4~10it | 5×10i4 | 101s |
General Features | ||||||||
Chemical solvent resistance | D543 | good | good | good | good | good | good | good |
Water absorption rate (24h)/% | D570 | <0.01 | <0.01 | <0.03 | <0.03 | <0.1 | <0.04 | <0.01 |
Refractive Index | 1.35 | 1.338 | 1.34 | 1. 40 | 1. 447 | 1.42 | ||
Limiting oxygen index | D2863 | >95 | >95 | >95 | 31 | 60 | 43 | 100 |
It should be noted that the above data is for reference only. The temperature range in actual application may be affected by factors such as material quality, thickness, processing method and environmental conditions. When you choose Teflon material, please be sure to refer to the product manual or email TST CABLES engineers to obtain accurate temperature resistance information.
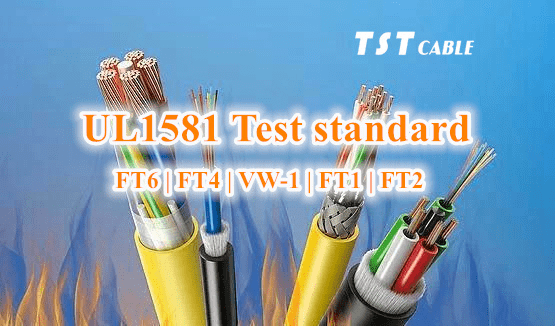
High Temperature Teflon Cable Standards and Tests
- UL1581 standard: Teflon cables must comply with the requirements of UL1581 standard, including tests on electrical performance, combustion performance, physical performance, etc.
- Electrical performance test: including conductor resistance test, voltage resistance test, insulation resistance test, etc.
- Combustion performance test: including vertical combustion test, horizontal combustion test, etc., to ensure that the cable has good flame retardant properties.
- Physical performance test: including tensile test and tensile test before and after aging, to evaluate the mechanical strength and durability of the cable.
- Environmental adaptability test: including high and low temperature resistance test, chemical corrosion resistance test, etc., to ensure the performance and safety of the cable under different environmental conditions.
Application scenarios and characteristics of various grades of low-smoke halogen-free flame-retardant cables
Class A halogen-free low-smoke flame-retardant cables
Class A halogen-free low-smoke flame-retardant cables have the best flame-retardant properties and are suitable for high-risk occasions such as crowded places, confined places, and difficult escape. They have the following characteristics:
(1) Very good flame-retardant properties, which can effectively prevent the spread of fire and protect personnel safety.
(2) Long service life, with good durability and anti-aging properties.
(3) Wide range of applications, can be used for wiring in various buildings and external power supply systems.
Cooperate with custom cable manufacturer TST CABLES to customize Teflon high temperature cables
TST CABLES Teflon cables challenge the high temperature limit of modern industry. Excellent temperature resistance, -200°C to 260°C; anti-corrosion, no fear of chemical erosion. Flexible and wear-resistant, stable transmission, escort your equipment. Aerospace military quality, making every meter of cable a model of safety and efficiency. If you have any needs for Teflon cables or want to get free samples, you are welcome to contact us by email or phone at any time (lixiangchao@testeck.com), looking forward to win-win cooperation with you!
Related by TST:
TST cables low smoke halogen free cable: “invisible guardian” in fire
In a smoke-filled environment, 80% of casualties are not caused...
Read MoreCharacteristics and Applications of LSZH Multi core Charging Cables
Low Smoke Zero Halogen (LSZH) multi-core charging cables are designed...
Read More600℃ High Temperature Resistant Cable Selection Guide for Aviation cable
In the fields of aviation and aerospace, the importance of...
Read MoreComparison between rail transit cables and other cables
With the development of high-speed railways and urban rail transit,...
Read MoreAlso available in:
Arabic
English
German
Indonesian
Japanese
Russian
Spanish
Thai
Vietnamese
Portuguese (Brazil)