In the cold winter, if wires and cables are exposed to extremely low temperatures, they may increase the risk of damage due to brittle materials, especially those installed outdoors or in unheated areas. In order to ensure the safety and reliability of wires and cables, it is very important to take appropriate antifreeze measures. Below, TST CABLES summarizes some effective ways to prevent freezing of wires and cables in winter:
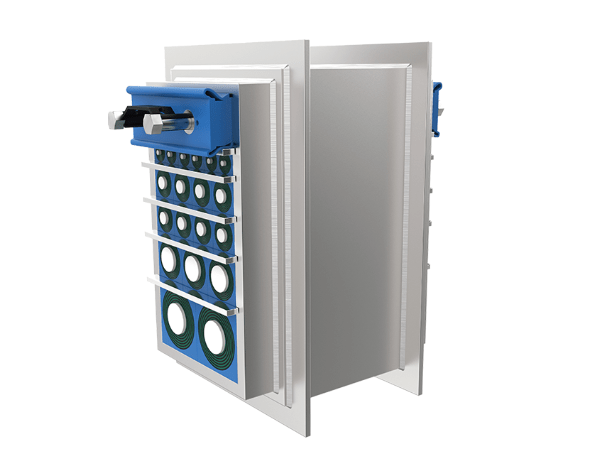
1. Choose the right type of cable
Low-temperature materials: Choose cables designed for low-temperature environments, such as polyvinyl chloride (PVC cable), cross-linked polyethylene (XLPE cable) or other insulation materials with excellent low-temperature performance.
Flexible cables: For applications that require frequent movement or bending, use cables with better flexibility to reduce the risk of hardening and breakage caused by lower temperatures.
2. Maintain a suitable working temperature
Heating protection: For critical equipment or important lines, consider installing self-regulating heat trace cables. These devices can automatically adjust the output heat according to the surrounding environment to maintain the temperature of the cable and its connection points.
Insulation sleeves: Wrapping the cable with insulation sleeves made of foam plastics, rubber and other materials helps reduce heat loss and maintain internal temperature.
3. Avoid extreme conditions
Indoor wiring: Lay the cables inside the building or heated space as far as possible, away from places directly exposed to cold air.
Underground burial: If it must be laid outdoors, bury it as deep as possible below the ground to use the natural insulation effect of the soil to resist the influence of low surface temperatures.
4. Regular inspection and maintenance
Inspection system: Establish a regular inspection mechanism, especially during periods of sudden temperature drops, closely monitor the status of the cables, and promptly detect and deal with possible problems.
Clear snow: Clear snow and ice around the cables in a timely manner to prevent them from melting and freezing again to cause pressure or damage to the cables.
5. Preventive measures
Lubricated joints: For moving parts or joints that may be affected by mechanical stress, apply special lubricants appropriately to reduce friction and avoid jamming or wear caused by temperature changes.
Sealing treatment: Ensure that all cable terminals, joints and other interfaces are well waterproof and moisture-proof sealed to prevent moisture from invading and freezing and expanding to damage the cable structure.
6. Plan the route reasonably
Avoid wind outlets: When planning the cable route, try to avoid areas where strong winds pass, because strong winds will accelerate heat loss and make the cable more susceptible to freezing.
Short-distance laying: shorten the exposed length of the cable to reduce the chance of it being affected by the external environment; for long-distance transmission, intermediate joints should be set up in sections and corresponding protection facilities should be provided.
7. Choose cold-resistant accessories
Metal protection: For metal accessories such as cable brackets and hooks, choose galvanized or other anti-corrosion products to prevent rust from weakening the strength.
Through the above measures, the cold resistance of wires and cables in winter can be greatly improved to ensure their normal operation. Of course, the specific implementation also needs to be combined with the actual situation, such as the specific use of the cable, the climate characteristics of the area, and the budget. If you are responsible for managing a large electrical system or have special needs, please consult TST CABLES professional engineers for more detailed guidance and suggestions, and you can also get free samples.