
Fire Resistant
EN45545-2
- Customized Design Production
Small MOQ
light Weight Small Size
- Long Time Guarantee
- Home
- /
- Electromagnetic Wire Winding Wire...
Electromagnetic wire | Winding wire | Polyimide cable application guide
Electromagnetic wire is a very delicate raw material in motor products
Electromagnetic wire, also known as winding wire, is an insulated wire used to make coils or windings in electrical products.
We generally call the coil wire of electrical machines electromagnetic wire. In other words, electromagnetic wire is “wire that converts electrical energy and magnetic energy into each other”.
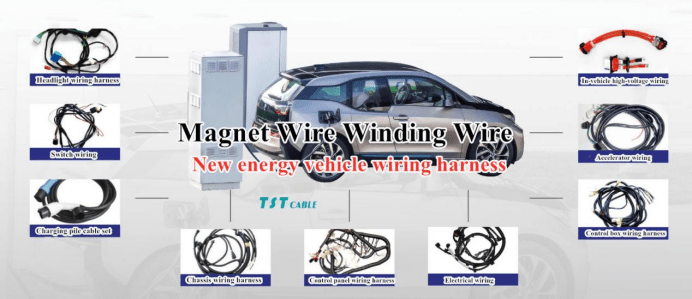
It uses Faraday’s electromagnetic induction effect, uses the magnetic field generated by the current or cuts the magnetic lines of force to generate induced current, thereby promoting the mutual conversion between electrical energy and magnetic field energy. There are many types of electromagnetic wires. According to the type, they can be divided into enameled wire, wrapped wire, enameled wrapped wire and inorganic insulated wire; according to the shape, they can be divided into round wire, flat wire, special-shaped wire, etc. Its downstream market mainly covers home appliances, industrial motors, automobiles and other industries.
Electromagnetic wire is one of the most delicate, critical and sensitive raw materials in motor equipment. It not only directly affects the performance and reliability of the motor, but also requires strict quality control and delicate processing during the manufacturing process. Electromagnetic wire must meet a variety of usage and manufacturing process requirements. The former includes its shape, specifications, ability to work at high temperature for a short time and for a long time, as well as to withstand strong vibration and centrifugal force at high speed in certain occasions, withstand corona and breakdown at high voltage, and resist chemical corrosion in special atmospheres; the latter includes the requirements for withstanding stretching, bending and abrasion during winding and embedding, as well as swelling and erosion during impregnation and drying.
Basic structure of electromagnetic wire | winding wire | polyimide cable
Electromagnetic wire is usually composed of the following parts:
Conductor: Usually a single or multiple stranded wires made of copper or aluminum. Copper is a more commonly used material due to its excellent conductivity and mechanical strength.
Insulation layer: The insulation layer is to prevent current from leaking to other conductors or the surrounding environment. Common insulating materials include enameling, polyester film, glass fiber, etc. Enameled wire is one of the most common types of electromagnetic wire, and its surface is coated with a layer of insulating varnish.
Shielding layer (optional): Some applications may also include a shielding layer to reduce electromagnetic interference (EMI).
Outer sheath (optional): In some cases, an outer sheath may be added to further protect the electromagnetic wire.
Electromagnetic wire | Winding wire | Polyimide cable application areas
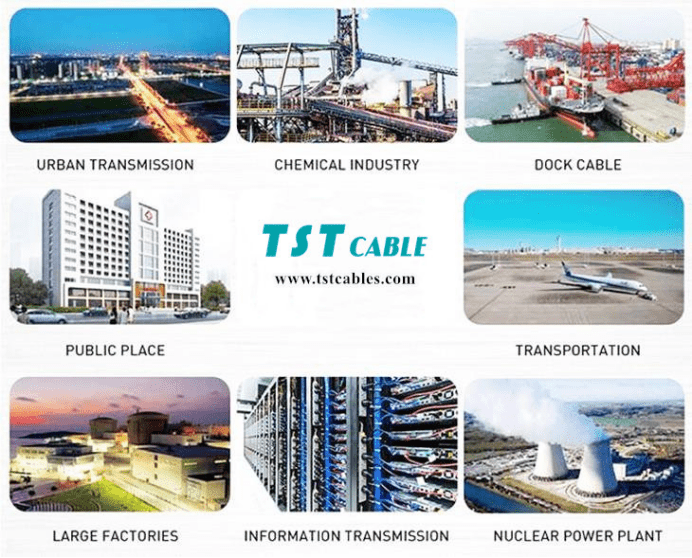
The application areas of electromagnetic wire are very wide, covering several important industries. Specifically, its main application areas include:
Some main application areas of polyimide cable:
Power industry
Transformer: power transformer, distribution transformer, etc., used for voltage conversion in power systems.
Generator: generator winding, used to convert mechanical energy into electrical energy.
Power transmission and distribution equipment:
winding components in high-voltage transmission equipment to ensure the efficiency and safety of power transmission.
Manufacturing industry
Industrial motor: motor used to drive various mechanical equipment, such as pumps, compressors, conveyor belts, etc.
Servo motor: servo motor in precision control applications, used in automated production lines.
Stepper motor: used in CNC machine tools and other occasions requiring precise position control.
Household appliances
Household motor: motors in household appliances such as air conditioners, refrigerators, washing machines, etc.
Fan: motor windings in household appliances such as ceiling fans and desktop fans.
Transportation
Electric Vehicles (EV): Winding components in electric vehicle drive motors and battery management systems.
Railway: Traction motors in rail vehicles such as trains and subways.
Aerospace: Special motors in aircraft and other aircraft.
Military and Space
Military Equipment: Special motors and sensors in military equipment.
Space Equipment: Precision motors and control systems in spacecraft such as satellites and rockets.
Medical Equipment
Medical Instruments: Small motors and controllers in medical equipment such as MRI machines and X-ray machines.
Communication Technology
Signal Transmission: Transformers and filters used in signal processing equipment such as communication base stations and radar systems.
Recommended electromagnetic wire products: 240-grade polyimide cable
Classification of electromagnetic wire
- Classification of electromagnetic wire | winding wire | polyimide cable by use
The uses of electromagnetic wire can be divided into two types:
① General use, mainly used in motors, electrical appliances, instruments, transformers, etc., by winding coils to generate electromagnetic effects, and using the principle of electromagnetic induction to achieve the purpose of converting electrical energy into magnetic energy;
② Special use, applied to electronic components, new energy vehicles and other fields with special characteristics, such as fine electronic wires are mainly used in the electronics and information industries to achieve information transmission, and special wires for new energy vehicles are mainly used in the production and manufacturing of new energy vehicles.
- Classification of electromagnetic wire | winding wire | polyimide cable by type
① Enameled wire: The insulating varnish is applied to the conductive wire core and dried to form a paint film as an insulating layer. Ordinary enameled wires can be divided into acetal, polyester, polyurethane, epoxy, polyesterimide, oily enameled wire, etc. Special enameled wires include self-adhesive straight welding enameled wire, self-adhesive enameled wire, and cryogen-resistant enameled wire.
Enameled wire
The corresponding lacquer solution is applied to the outside of the conductor, and then the solvent evaporates and the paint film solidifies and cools to make it. Enameled wire can be divided into polyester enameled wire,
polyesterimide enameled wire, polyamideimide enameled wire, polyimide enameled wire, polyesterimide/polyamideimide enameled wire, corona-resistant enameled wire, as well as oily paint, acetal paint, polyurethane enameled wire, etc. according to the insulating paint used. Sometimes it is also classified according to the specificity of its use, such as self-adhesive enameled wire, refrigerant-resistant enameled wire, etc.
The earliest enameled wire was oily enameled wire, made of tung oil, etc. Its paint film has poor wear resistance and cannot be directly used to manufacture motor coils and windings. When used, it needs to be wrapped with cotton yarn. Later, polyvinyl alcohol formal enameled wire came out, and its mechanical properties were greatly improved. It can be directly used for motor windings and is called high-strength enameled wire.
With the development of weak current technology, self-adhesive enameled wire has appeared, which can obtain coils with better integrity without dipping and baking. However, its mechanical strength is poor and it can only be used in micro motors and small motors. In addition, in order to avoid the trouble of removing the paint film before welding, direct soldering enameled wire has been developed. Its coating can fall off by itself in the high-temperature tinning tank, making the copper wire easy to weld.
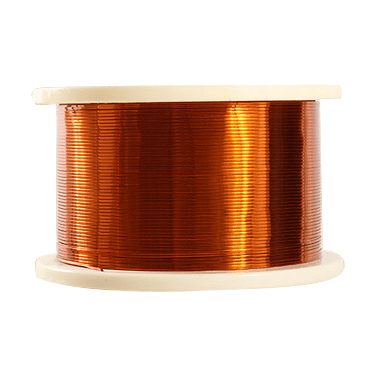
Due to the increasing application of enameled wire and increasingly stringent requirements, composite enameled wire has also been developed. Its inner and outer paint films are composed of different polymer materials, such as polyesterimide/polyamideimide enameled wire.
② Wrapped electromagnetic wire, the electromagnetic wire formed by tightly wrapping insulating paper, glass fiber, natural silk and synthetic silk on the bare wire or enameled wire to form an insulating layer is called wrapped electromagnetic wire. Including silk-wrapped wire, glass-wrapped wire, paper-wrapped wire, film-wrapped wire, etc.
Wrapped wire
Wrapped wire is an important variety of electromagnetic wire winding wire. In the early days, cotton yarn and silk were used, called yarn-wrapped wire and silk-wrapped wire, which were used in motors and electrical appliances. Due to the large insulation thickness and low heat resistance, most of them have been replaced by enameled wire. At present, it is only used as high-frequency winding wire. In large and medium-sized winding wires, when the heat resistance level is high and the mechanical strength is large, glass fiber wrapped wire is also used, and appropriate adhesive paint is used during manufacturing.
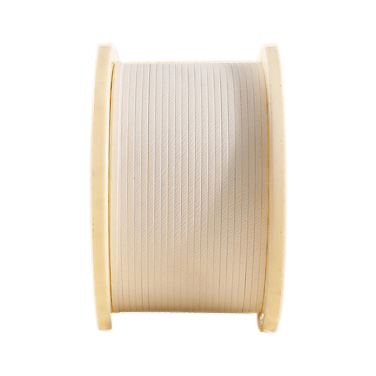
Paper-wrapped wire still occupies a considerable position in the wrapped wire, and is mainly used in oil-immersed transformers. The oil-paper insulation formed at this time has excellent dielectric properties, low price and long life. Paper-wrapped wire is a wire made of oxygen-free copper rod or electrical round aluminum rod extruded or drawn through a certain specification of die and then annealed, and then wrapped with two or more layers of insulating paper (including telephone paper, cable paper, high-voltage cable paper, inter-turn insulation paper, etc.) on the copper (aluminum) conductor. It is suitable for oil-immersed transformer coils and other similar electrical winding wires. NOMEX paper-wrapped wire is a winding wire made of oxygen-free copper rod or electrical round aluminum rod extruded through a certain specification of die, and then wrapped with NOMEX insulating paper produced by DuPont of the United States. It is mainly used for transformers, welding machines, electromagnets or other similar electrical equipment product windings. Electrical bare copper (aluminum) wire produced by extrusion process is the most ideal material for producing cable paper-wrapped wire.
In recent years, film-wrapped wire has developed rapidly, mainly polyester film and polyimide film-wrapped wire.
Recently, there are also mica tape-wrapped polyesterimide film-wrapped copper flat wires for wind power generation.
③ Inorganic insulated electromagnetic wire: electromagnetic wire with inorganic insulating materials such as ceramics, glass films, oxide films, etc. as insulation layers.
Insulated wire
When the heat resistance grade requirement exceeds the limit of organic materials, inorganic insulating paint is usually used for coating. Existing inorganic insulated wires can be further divided into glass film wires, oxide film wires and ceramic wires.
④ Special electromagnetic wire: It is an electromagnetic wire with insulation structure and characteristics suitable for special occasions, such as medium and high frequency winding wires, polyethylene insulated nylon sheathed submersible motor windings, etc.
⑤ Others: There are also combined conductors, transposed conductors, etc.
3. Classification of electromagnetic wire | winding wire | polyimide cable products
240 grade polyimide cable
- Material: copper
- Insulation layer: polyimide
- Heat resistance level: 240 grade (maximum operating temperature can reach about 400°C)
- Features: Good high temperature stability, suitable for use under extreme conditions
- Application: Motors, transformers and other electrical equipment in high temperature environments
Corona resistant enameled copper round wire
- Material: copper
- Insulation layer: special corona resistant material
- Features: Excellent anti-corona performance and extended service life
- Application: Suitable for electrical equipment working in high frequency and high voltage environments
Self-adhesive enameled copper round wire
- Material: copper
- Insulation layer: self-adhesive enameled
- Features: Can melt and bond when heated to enhance mechanical strength
- Application: Electrical equipment in high frequency vibration environments
TST CABLES electromagnetic wire | winding wire | polyimide cable production process
- Material preparation
The raw materials of the electromagnetic wire are transported to the production site by carts. The preparation of insulating varnish is completed in the paint preparation room. TST CABLES cable technology engineers fully mix a certain proportion of varnish and thinner according to the different insulation levels of various electromagnetic wires and evenly add them to the enameling machine.
- Wire drawing
Wire drawing is carried out in the wire drawing machine, and is drawn once or multiple times according to the required wire diameter. The temperature during drawing can generally reach 60-100℃, and water-soluble lubricants are used for lubrication and cooling. When the temperature exceeds 100℃, supplementary cooling and heat removal are carried out.
- Annealing
Annealing is generally carried out in an annealing furnace by electric heating. The annealing temperature is generally controlled at 300-600℃. During annealing, water vapor is used for protection to prevent oxidation. After annealing, a hair dryer is used for air cooling, and it enters the impregnation section at about 40℃.
- Impregnation
The impregnation section is carried out in the enameling machine and is completed multiple times according to the requirements of the insulation layer. During impregnation, an appropriate proportion of thinner is added according to the needs of the coating. The thinner contains flammable and toxic liquids such as cresol and xylene.
- Drying
The drying of electromagnetic wire is carried out in a drying furnace. The drying temperature is determined according to the speed of wire drawing, generally 300-400℃. The highest temperature can reach 670 degrees Celsius. Drying and exhaust gas removal are carried out simultaneously. The exhaust gas (temperature is 300-400 degrees Celsius) contains toxic and flammable vapors such as cresol, phenol, and xylene. After the catalytic reaction reaches the environmental protection index, it is discharged into the atmosphere by the exhaust fan.
- Reeling
Reeling is to use the reeling device to wind the dried electromagnetic wire product on the reel. A small amount of lubricant (974 gasoline, cyclohexane) needs to be added when reeling.
- Packaging and warehousing
After passing the inspection, the wound reel is wrapped with plastic film and loaded into a carton or paper tube, packaged into a wire drag according to user needs, and loaded and unloaded into a special warehouse.
Precautions for electromagnetic wire | winding wire | polyimide cable
The storage of electromagnetic wire is a very important link. If the storage method is not appropriate, it will damage the quality of the electromagnetic wire product and affect the safety of use. Notes on the storage of electromagnetic wire:
- During storage, it should be rolled regularly;
- The shelf life of the wire is 12 months, generally not more than 6 months, and no more than 1 year;
- Keep ventilation, the best condition is constant temperature and humidity, the temperature is 20-25 degrees, and the humidity should be controlled (below 60%);
- Avoid high temperature, absolutely cannot be stored in the open air, about 30 cm from the ground is appropriate to have a moisture-proof effect;
- Be careful to handle with care to avoid tipping and collision;
- When taking the wire, never directly touch the surface of the wire.
TST CABLES electromagnetic wire | winding wire | polyimide electromagnetic flat wire has low loss and obvious technical advantages
According to the shape of the material, electromagnetic wire can be divided into round wire, flat wire, and special-shaped wire. Round wire technology has experienced a development process of hundreds of years and is currently the largest and most widely used electromagnetic wire. However, since there will be a travel gap after the entire wire is rolled into a coil, the utilization rate of the space is not maximized, so improving the conversion rate of motor efficiency has become one of the research hotspots in the industry. In this context, TST CABLES flat wire technology has received widespread attention. Flat wire motors are based on a winding technology with a square cross-sectional area of electromagnetic wire, and the cross-section of the winding copper wire is generally rectangular. When manufacturing the stator bracket, the winding is made into a hairpin shape and inserted into the pre-stator slot, and then the winding is twisted and merged at the other end to form a complete winding. In the cross-section of the square stator, the circular arrangement will leave many gaps, while the square copper wire can completely fill the entire cross-section, greatly improving the efficiency of the copper wire.
Polyimide electromagnetic flat wire can greatly reduce copper consumption
Today, the energy conversion efficiency of permanent magnet synchronous motors has reached nearly 97%, of which about 3% of the motor loss mainly comes from copper loss, iron loss and wind loss. The loss of copper is because the conductor is not completely filled, and the flat wire motor changes the cross-sectional area of the copper wire to a square, which cleverly solves the problem of copper loss and improves space utilization. The trend of flat wire substitution has already appeared in the industry, and the first to realize flat wire motors was foreign automobile companies. In 2007, flat wire motors were first used by foreign automobile companies. As early as 2007, the Chevrolet Volt was equipped with Magna’s flat wire motors. Toyota and Nissan were also equipped with Denso’s flat wire motors, and Schaeffler also completed research on flat wire motors. At this stage, domestic motor factories are also accelerating the research on flat wire technology, including SAIC, BYD, BAIC, Great Wall, TST CABLES and other companies’ motor factories have achieved phased results.
TST CABLES electromagnetic wire products are diverse
When you choose electromagnetic wire, you need to consider multiple factors, such as manufacturing process, material ratio, test standards, operating temperature, voltage level, mechanical strength, chemical resistance, etc. In addition, the specific requirements of the application environment need to be considered, such as whether it needs UV resistance, oil resistance, wear resistance, waterproof, dustproof, tensile resistance and other characteristics. If you have any needs or questions about electromagnetic wires, you are welcome to email TST CABLES technical engineers
(email: lixiangchao@testeck.com)
Related by TST:
TST cables low smoke halogen free cable: “invisible guardian” in fire
In a smoke-filled environment, 80% of casualties are not caused...
Read MoreCharacteristics and Applications of LSZH Multi core Charging Cables
Low Smoke Zero Halogen (LSZH) multi-core charging cables are designed...
Read More600℃ High Temperature Resistant Cable Selection Guide for Aviation cable
In the fields of aviation and aerospace, the importance of...
Read MoreComparison between rail transit cables and other cables
With the development of high-speed railways and urban rail transit,...
Read MoreAlso available in:
Arabic
English
German
Indonesian
Japanese
Russian
Spanish
Thai
Vietnamese
Portuguese (Brazil)