Development Status of Aluminum Alloy Cable
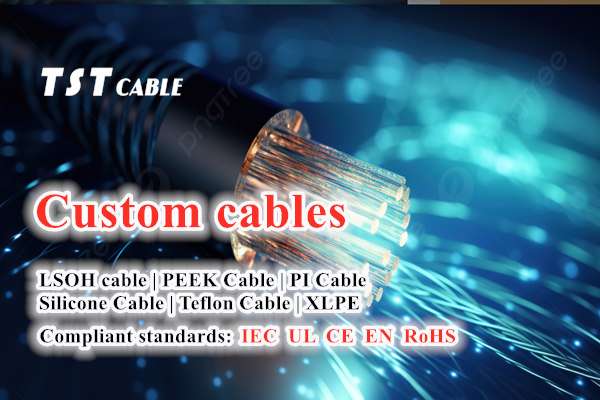
Foreign Status
Since 1968, the United States has begun to develop and produce alloy power cables, and has begun to promote and apply them in the United States, Canada, Mexico and other countries. It is mainly used in construction projects such as airports, military bases, office buildings, residences, hotels, supermarkets, colleges, stadiums, hospitals, and factory buildings. The United States has successfully applied alloy cables for more than 40 years, and there has never been any safety accidents. This is one of the important reasons for the rapid promotion and application of new material alloy power cables throughout the country.
Domestic Status
Aluminum alloy cables are no longer a new thing, and their performance and price advantages have also been tested by authoritative testing. Statistics show that copper wire cables still account for more than 90% of the market share. Of course, this cannot prevent the good momentum of aluminum alloy cables being gradually recognized and accepted by the public. Through the company’s order status and user feedback, it clearly expresses its confidence in the future of aluminum alloy cables.
According to the data, aluminum alloy cables with higher cost performance and superior electrical performance have a history of nearly 40 years of use in European and American countries, and their use rate in hospitals, churches, and government agencies is particularly prominent. In general, the sales volume of aluminum alloy cables is far behind that of copper wire cables, but small orders from governments, factories, hospitals, and residential buildings show a clear upward trend, which means that aluminum alloy cables have been widely recognized in the most basic cable application fields and in the most complex use conditions, which also means that aluminum alloy cables have a bright future!
The same is true in medical and civil projects. Many hospitals still use copper wire cables in the main buildings in the early stage, and try aluminum alloy cables with better corrosion resistance in outdoor and corridor lighting with complex environments and changing working conditions. The use effect is good and plans to use aluminum alloy cables to save copper wire cables in the next cable replacement.
Service life of aluminum alloy cables
1. There are two main types of corrosion of conductor parts: chemical corrosion and electrochemical corrosion
Chemical corrosion: refers to the corrosion of metals in the atmosphere under the action of oxygen, chlorine, sulfur dioxide, hydrogen sulfide and other gases.
After the metal surface reacts with oxygen, different metal oxides are generated.
Aluminum oxide can form a dense surface protective film with a certain hardness.
Iron oxide has a loose structure and is easy to fall off. It continues to penetrate and diffuse into the metal, destroying the material.
Copper oxide is commonly known as verdigris, which is between the above two and is a toxic substance.
Electrochemical corrosion: refers to the corrosion process of metal formed by the primary battery composed of metal and medium. When two metals with different electrode potentials are connected, and there is water or other electrolytes in between, a current will be generated between the two metals to form a primary battery. One metal is at a positive potential and the other is at a negative potential. The metal at the negative potential will continue to accumulate in an ion state through the electrolyte to the metal at the positive potential. The metal at the negative potential is gradually lost and destroyed, forming electrochemical corrosion. The greater the difference in electrode potential between the two metals, the stronger the electrochemical corrosion. The higher the temperature, the more serious the corrosion of the metal.
Different metals have different electrode potentials. The electrode potential order of several commonly used metals is; metal Ag (silver) Cu (copper) Pb (lead) Sn (tin) Fe (iron) Zn (zinc) Al (aluminum). Potential +0.8+0.334-0.122-0.16-0.44-0.76-1.33 The more negative the electrode potential of a metal is, the stronger its tendency to become an ion in the electrolyte is, that is, the more susceptible it is to corrosion. The negative value of the electrode potential of aluminum is relatively large, but because there is often a protective layer of oxide film on its surface, its corrosion resistance can be improved.
Rare earth aluminum alloy material is the addition of rare earth elements to aluminum, which can purify, improve purity, fill surface defects, and refine grains. It reduces segregation and eliminates the role of local corrosion caused by microscopic unevenness. At the same time, it also brings about the negative shift of the electrode potential of aluminum, has a sacrificial anode effect and excellent conductivity, thereby greatly improving the corrosion resistance of aluminum. For corrosion problems such as C1- in marine environments and S, H2S+C02 in petroleum and chemical environments, this material has a unique anti-corrosion mechanism. The strong reducing property of rare earth metals can effectively combine with the strong oxidizing property of S, H2S, and C1-, interact with each other, and generate stable compounds (C1- and rare earth aluminum alloys generate stable coordination compounds), organically unifying the oxidation and reduction processes in chemical reactions, interacting with each other, and fundamentally stopping the corrosion damage caused by the oxidation activities of corrosive media such as S, H2S, and C1-, thereby completely solving the problem that has not been well solved in developed countries around the world, including the United States. According to the testing and engineering case data analysis of national testing departments such as the Beijing Nonferrous Metals Research Institute, the annual corrosion rate of rare earth aluminum alloys is zero or almost zero under the conditions of chloride ions, seawater, marine atmosphere, salt spray environment (dry and wet alternation), saturated HzS, sulfur, and high temperature and high pressure environments.
2. Insulation part
The current carrying capacity of power cables refers to the maximum current allowed to pass through the cable conductor at the highest allowable temperature. When designing and selecting cables, the heat generated by the loss of each part of the cable should not exceed the maximum allowable temperature of the cable. In most cases, the transmission capacity of the cable is determined by the maximum temperature limit of the cable. The maximum allowable temperature of the cable mainly depends on the thermal aging performance of the insulation material used. Because the working temperature of the cable is too high, the aging of the insulation material will be accelerated and the life of the cable will be greatly shortened. If the cable operates above the maximum allowable temperature, the cable will work safely for 30 years.
XLPE is the abbreviation of the English name of cross-linked polyethylene. Polyethylene is a linear molecular structure that is very easy to deform at high temperatures. The cross-linking polyethylene process turns it into a mesh structure. This structure has strong resistance to deformation even at high temperatures.
The excellent anti-aging properties and super heat-resistant deformation of cross-linked polyethylene determine that large currents can be allowed to pass under normal operating temperature (90C), short-term faults (130C) and short circuits (250C). Because its operating temperature is 20C higher than that of polyvinyl chloride, it has excellent thermal resistance, increases the anti-aging performance of insulation, and greatly increases its life.
Aluminum alloy cable economic performance
Direct procurement cost
Price comparison between aluminum alloy cable and copper core cable: Aluminum alloy cable has superior safety performance, electrical performance, mechanical performance and longer service life, and the price of aluminum alloy cable is only about 75% of copper cable.
Reduced installation cost
Save installation cost: Due to the good bending performance and light weight of aluminum alloy cable, it is easy to install.
Disadvantages of aluminum alloy cable
1. Forbidden area of aluminum alloy cable application. Aluminum alloy cable is best not to be used in high-rise buildings with dense population. For safety reasons, engineers generally use copper cable as the shaft power supply trunk line of high-rise buildings with dense population.
2. Not suitable for 16mm cables. Aluminum alloy cable has a greater advantage for cables with larger cross-sections. The Building Electrical Branch of the China Architecture Society and technical personnel from non-EE international organizations once held a forum in Shanghai on the application of aluminum conductor cables. The conclusion drawn at the meeting was: For cables below 16mm2, copper conductors are recommended due to mechanical strength issues. Because the weight of aluminum conductors is less than that of copper conductors, the advantages of aluminum conductors are more obvious for larger cross-sections.
3. Aluminum alloy cables are not suitable for use in important occasions. The application scope of aluminum cables is mainly in relatively common buildings, such as factories, schools, residences, commercial buildings and other fields. In some common fields, aluminum conductor cables can completely replace copper cables. However, in some important places and some special places, such as urban power supply trunk lines, large power plants, heavily polluted environments and other environments that are not easy to maintain, aluminum conductor cables are not the best choice. Because these places must ensure the safety and reliability of power supply, and require very high stability of power supply, it is better to use safer copper cables as the first choice.
Common specifications and models
Common domestic aluminum alloy specifications and models
YJHV (TC90) aluminum alloy cable, namely: cross-linked polyethylene insulated PVC sheathed aluminum alloy power cable, is a non-armored alloy cable; YJHLV8 (AC90) aluminum alloy cable, namely: cross-linked polyethylene insulated aluminum alloy with interlocking armored aluminum alloy power cable, is a flexible self-locking aluminum armored alloy cable;
YJHLV82 (ACWU90) aluminum alloy cable, namely: cross-linked polyethylene insulated aluminum alloy with interlocking armored PVC sheathed aluminum alloy power cable, is a flexible self-locking aluminum armored sheathed alloy cable;
YJHLV22 aluminum alloy cable, namely: cross-linked polyethylene insulated steel belt armored PVC sheathed aluminum alloy power cable, the armor layer uses high-strength double steel belt armor;
YJHLY83 aluminum alloy cable, namely: cross-linked polyethylene insulated aluminum alloy with interlocking armored polyolefin sheathed aluminum alloy power cable, is a halogen-free and low-smoke self-locking aluminum armored alloy cable.
Common aluminum alloy specifications abroad
AC90, ACWU90, SER, SEU, RW90, RWU90, MC, UD-1350, UD-8000, MHF, XHHW-2, etc.
Manufacturing standards
In North America and other regions, aluminum alloy cables are mainly produced and inspected according to ASTM B800-05 (2011), ASTM B801-07 (2012), C22. 2 No. 51-09, and UL1569. At present, the aluminum alloy cable standard implemented in my country is the energy industry standard “Rated voltage 0.6/lkV aluminum alloy conductor cross-linked polyethylene insulated cable” (NB/T 42051—2015).
According to the website of the National Standardization Administration, the national standard “Rated voltage 1kV (Um = 1.2kV) to 35kV (Um = 40. 5kV) aluminum alloy core extruded insulation power cable” (GB/T31840-2015) was officially released on July 3, 2015, and will be officially implemented on February 1, 2016.
Aluminum alloy cable application standards
1) International standard: ASTM B800-05 (2011), Chinese name: 8000 series aluminum alloy wire standard in annealing and intermediate heat treatment state for electrical use.
2) Domestic standards: “Aluminum alloy wire for cable conductor” (GB/T 30552-2014), “Conductor of cable” (GB/T3956-2008), “Electrical round aluminum rod” (GB/T3954-2014).
The relevant application standards of domestic aluminum alloy cables are relatively complete. The national industry standards (Residential Building Electrical Design Code) (JGJ 242-2011) and “Store Building Design Code” issued by the Ministry of Housing and Urban-Rural Development (JGJ 48-2014), national building standard design atlas 10CD106 “Aluminum Alloy Cable Laying and Installation” and other national guiding standards and specifications, as well as local guiding standards and specifications such as “Aluminum Alloy Cable Engineering Design, Construction and Acceptance Regulations” issued and implemented by provincial management departments such as provincial housing and urban-rural development departments, have substantial guiding value.
Also available in:
English