The conductor twisting of cross-linked polyethylene cable (XLPE cable) is a key step in the manufacturing process, which directly affects the overall performance and quality of the cable. TST CABLES will give a detailed introduction to the common XLPE cable conductor twisting process on the market.

1. XLPE cable Conductor material preparation
Selection of suitable conductor material: High-purity oxygen-free copper or aluminum is usually used as the conductor material, which has good conductivity and processing performance.
Wire preparation: Copper or aluminum ingots are made into fine wires through wire drawing process, and the wire diameter is determined according to the required final conductor cross-sectional area.
2. XLPE cable Single wire pretreatment
Annealing treatment: In order to increase flexibility and reduce internal stress, single wires may be annealed before twisting. Apply lubricant and protect the metal surface from damage.
3. Twisting process
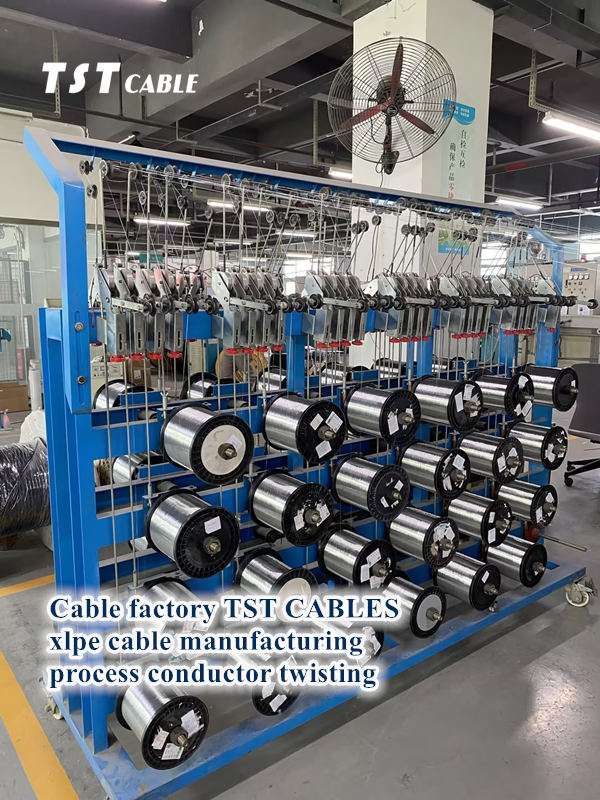
Center wire selection: First select one or more thicker wires as the center wire, depending on the required conductor structure (such as single core, double core, etc.).
Layered twisting: Twisting is performed layer by layer around the center wire in a specific direction and pitch. Each layer can be composed of wires of different numbers and specifications, and the number of layers and arrangement are customized according to standard regulations or customer needs.
Control of twisting parameters: including but not limited to twisting angle, pitch ratio, compression coefficient, etc., which are important factors affecting conductor performance and must be strictly controlled.
Compression treatment: For some types of conductors, compression treatment will be carried out after twisting to make the conductors more compact, reduce their outer diameter, and improve mechanical strength and electrical performance.
4. XLPE cable Inspection and testing
Visual inspection: Ensure that the conductor has no obvious defects, such as scratches, cracks or other physical damage.
Dimension measurement: Verify whether the outer diameter of the conductor meets the design requirements.
Resistance test: Measure the DC resistance of the conductor to ensure that it meets the corresponding standard limits.
Other tests: Mechanical performance tests such as bending tests and torsion tests may also be carried out as needed.
5. XLPE cable Subsequent processes
Insulation extrusion: After the twisting is completed, the conductor will be sent to the next process – that is, a layer of XLPE insulation material is extruded on the outside of the conductor.
Sheath molding: If necessary, a protective outer sheath will be added to the outside of the insulation layer.
During the entire stranding process, XLPE cable manufacturer TST CABLES needs to follow strict process specifications and technical standards to ensure that the produced XLPE cables have excellent electrical and mechanical properties. In addition, TST CABLES’ advanced production equipment and automated control systems also help improve production efficiency and product quality consistency. If you have more specific questions or are particularly interested in a certain XLPE cable production process, please email and communicate with TST CABLES cable engineers, and you can also get free XLPE cable samples.
Also available in:
Arabic
English
Japanese
Russian
Portuguese (Brazil)