The rapid development of rail transit has put forward higher requirements for cable performance – it must withstand extreme temperatures and ensure long-term safe operation. As a benchmark enterprise in China’s rail transit cable field, TST cable has solved the problem of heat resistance through material innovation from traditional materials to cross-linked polyethylene (XLPE), providing more reliable power transmission solutions for high-speed rail, subway and other scenarios.
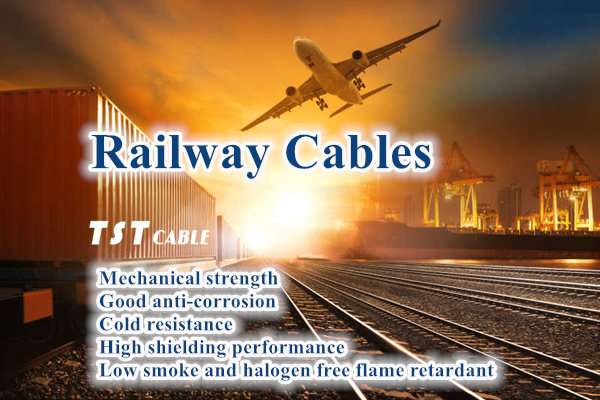
Traditional materials: the dual challenge of heat resistance and safety
Traditional materials (such as polyethylene PE and polyvinyl chloride PVC) were once the mainstream choice for cable insulation, but their linear molecular structure has obvious shortcomings:
Insufficient heat resistance: Ordinary polyethylene cables have a long-term working temperature of only 70°C, and are prone to softening and deformation at high temperatures, resulting in reduced insulation performance and even causing short circuits.
Weak mechanical properties: Polyethylene and polyvinyl chloride are easily affected by environmental stress, and are prone to cracking and accelerated aging in rail scenes with frequent vibrations.
Environmental hazards: PVC releases toxic gases when burned, which does not meet the strict requirements of modern rail transit for low smoke and halogen-free.
These defects are particularly prominent in high-speed, high-load rail transit scenarios. TST cable realized that only material innovation can break through the technical bottleneck.
Cross-linked polyethylene cable (XLPE): the “molecular code” of temperature resistance
Cross-linked polyethylene (XLPE) is a thermosetting material that forms a three-dimensional network structure between ordinary polyethylene molecular chains by chemical methods. This cross-linking process significantly enhances the physical and electrical properties of polyethylene, making it an ideal material for widespread use in power transmission and distribution systems.
Characteristics and advantages of cross-linked polyethylene cable (XLPE)
- Heat resistance: XLPE has higher heat resistance than unmodified polyethylene, can work stably in the operating temperature range of -40°C to +90°C, and can withstand temperatures up to +250°C in short-circuit conditions.
- Mechanical strength: Due to the cross-linking between molecules, XLPE cables have excellent tensile strength and impact resistance, which makes them more durable and less prone to damage during laying.
- Electrical properties: XLPE provides good electrical insulation properties, low dielectric loss, and is suitable for applications with high voltage levels, from 600V to 25kV and even higher.
- Resistance to environmental stress cracking: Compared with ordinary PE, XLPE shows better resistance to environmental stress cracking, which means it is more resistant to problems that may arise from long-term exposure to harsh environments.
- Chemical resistance: XLPE has good resistance to many chemicals, including acids, alkalis and solvents, and is suitable for use in corrosive environments such as chemicals.
- Dimensional stability: Even under high temperature conditions, XLPE can maintain its shape and size without deformation, which is very important for ensuring the stability and safety of the cable after laying.
- Environmental protection characteristics: XLPE does not contain halogens, produces less smoke when burned, and has low toxicity, which meets the environmental protection requirements of modern construction and industrial fields.
TST cable cross-linked polyethylene cable (XLPE) manufacturing process
The manufacture of XLPE cable involves heating the polyethylene raw material to the melting point and adding a cross-linking agent to complete the cross-linking reaction during the extrusion process.
Common cross-linking methods include:
Peroxide cross-linking method: using organic peroxide as an initiator, cross-linking reaction occurs between polyethylene molecules under heating conditions.
Silane cross-linking method: using silane compounds as cross-linking agents, cross-linking is achieved through hydrolysis condensation reaction.
By introducing chemical cross-linking technology, TST cable transforms the linear molecular structure of polyethylene into a three-dimensional mesh structure, achieving a leap in material performance:
High temperature resistance doubled. The mesh structure of XLPE gives it excellent heat resistance: the long-term working temperature is increased to 90°C, the short-term temperature resistance is 150°C, and the thermal life is up to 30 years. Even in high-temperature areas such as high-speed rail power cabins, the cable can still maintain stable transmission to avoid performance degradation caused by thermal aging.
Adaptability to low-temperature environments In response to the severe cold climate in the north, TST cable has developed a cold-resistant XLPE cable, which uses cold-resistant halogen-free materials. It can maintain flexibility at -40°C, avoid brittle cracking of the sheath, and ensure uninterrupted operation of rail transit in extremely cold areas.
Improved comprehensive performance
Insulation enhancement: The dielectric loss tangent is extremely low and is less affected by temperature, ensuring insulation stability under complex working conditions;
Optimized mechanical strength: Improved hardness and wear resistance, and resistant to rail vibration and mechanical stress;
Environmental protection and safety: The combustion products are only CO₂ and H₂O, meeting international flame retardant standards such as EN45545-2, reducing the risk of fire toxicity.
Railway transportation scene application
Application field
Power transmission and distribution: XLPE cables are widely used in underground cable systems, overhead lines, and indoor wiring.
Industrial facilities: such as oil and gas extraction, chemical plants, and other places that require high-performance cables.
Transportation: Power supply networks for public transportation systems such as railways and subways.
Commercial buildings: Power distribution systems for large shopping malls, office buildings, and other places.
Residential construction: Power supply systems within homes.
TST cable deeply integrates XLPE technology into product design to form multi-scenario solutions:
High-temperature power system: used for high-speed rail traction motor cables. Under continuous operation at 90℃, the current carrying capacity is 20% higher than that of traditional cables, supporting high-power power transmission;
Cold-resistant cables: used in Northeast high-cold subway lines. The insulation layer has no cracking under -40℃ environment, ensuring winter operation safety in cold areas;
Fire safety scenario: through CRCC certification and EN50382 standard test, its low-smoke halogen-free XLPE cables have been installed on more than 500,000 vehicles, covering 3,500 high-speed railways, and the operating mileage has exceeded 6 million kilometers.
As a high-performance cable material, cross-linked polyethylene plays an important role in many industries with its excellent heat resistance, mechanical strength and electrical properties. With the advancement of technology, the application scope of XLPE is also expanding.
TST cable’s XLPE technology not only meets domestic standards, but also passes international certifications such as EU EN45545-2. Comparative tests show that after 70 days of accelerated aging at 135°C, the elongation retention rate of domestic XLPE is even better than that of imported materials, confirming its long-term reliability. This breakthrough breaks the situation of high-end cable materials relying on imports and helps China’s rail transit equipment “go overseas”.
Facing the trend of rail transit 4.0, TST cable is also exploring more possibilities of cable materials. From polyolefins to cross-linked polyethylene, TST cable solves the problem of temperature resistance with material innovation, helping the industry move towards safety, intelligence and sustainability. In the future, with the iteration of technology and the deepening of scenarios, this innovation of “molecular structure” will continue to escort every kilometer of global rail transit.
If your rail transit equipment cable needs to upgrade the latest technology, please send an email to contact our TST CABLE cable engineer, and you can also get a free sample.
Also available in:
English