Performance Comparison of Zinc Coaxial Cable and Copper Coaxial Cable(zinc coax vs copper coax)
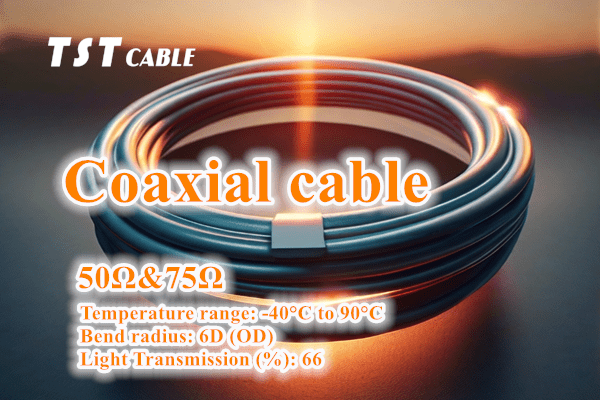
The comparison between zinc coaxial cable and copper coaxial cable mainly focuses on material properties, performance and application scenarios. The following is a detailed comparison of the two cables:
Material properties
·Copper coaxial cable: Copper is an excellent conductive material with very high conductivity and good mechanical strength. It is widely used in various electrical and electronic equipment. The conductivity of copper allows it to effectively transmit high-frequency signals, and its good flexibility also facilitates installation and wiring.
·Zinc coaxial cable: In fact, coaxial cables that directly use zinc as a conductor material are very rare on the market because zinc is far less conductive than copper. Zinc is often used as a coating material to protect cables from corrosion, especially in outdoor or humid environments.
Performance
·Conductivity: Copper is about 6 times more conductive than zinc, which means that under the same conditions, copper cables can provide lower resistance and less energy loss.
·Signal attenuation: Due to the better conductivity of copper, copper coaxial cables can maintain higher signal quality and reduce signal attenuation when transmitting over long distances.
·Interference resistance: Both materials can resist electromagnetic interference (EMI) with proper shielding design, but copper’s higher conductivity helps improve shielding effectiveness.
·Durability and reliability: Although zinc coating can help prevent oxidation and corrosion, zinc may powder after long-term exposure to harsh environments; copper has better durability, especially when anti-oxidation treatment is used.
Application scenarios
·Copper coaxial cable: It is suitable for a wide range of communication fields, such as television broadcasting, satellite communications, closed-circuit television surveillance systems (CCTV), computer networks, etc. Copper is the preferred material for applications that require high bandwidth and high-quality signal transmission.
·Zinc coaxial cable: If there is a so-called “zinc coaxial cable”, they may refer to cables with zinc coating or other forms of zinc protective layer on the outside. This design is mainly used to enhance the weather resistance and corrosion resistance of the cable, rather than to improve the internal signal transmission characteristics. This type of cable may be more suitable for applications in certain special environments, such as seaside or chemical plants with strong corrosive environments.
Cost factors
·Cost: Generally speaking, the price of copper is higher than that of zinc, so the cost of coaxial cable made of pure copper will also increase accordingly. However, given the performance advantages of copper, many users are willing to pay a premium for better performance and service life.
In most cases, the term “zinc coaxial cable” is not common, and may be a misunderstanding or a description of cables with a zinc coating protective layer. In actual applications, which type of coaxial cable to choose depends on specific needs, budget and working environment requirements. If you do encounter a product marked as “zinc coaxial cable”, please carefully check the product’s detailed description and technical parameters to ensure that you understand its true characteristics and scope of application.
Performance comparison of copper coaxial cable and aluminum coaxial cable
There are some significant differences between copper coaxial cable and aluminum coaxial cable in terms of material properties, performance performance and application scenarios. Here are the main comparisons between the two:
Material properties
Conductivity: Copper is more conductive than aluminum, with copper conductivity being about 60% of aluminum. This means that at the same size, copper cables can provide lower resistance, thereby reducing energy loss during signal transmission.
Mechanical strength: Copper is harder and more ductile than aluminum, which makes copper wires easier to bend and less likely to break, and also helps to improve the reliability of connection points.
Weight: Aluminum has a lower density, so aluminum wire of the same length and specification will be much lighter than copper wire, which is an advantage for applications where weight is a concern, such as aviation or suspension installation.
Performance
Signal attenuation: Since copper has better conductivity, copper coaxial cable exhibits lower signal attenuation over long distances, especially at high frequencies.
Anti-interference ability: Copper’s higher conductivity also means that it can block external electromagnetic interference (EMI) more effectively in the shielding layer, providing better protection for internal signals.
Temperature coefficient: The resistance of aluminum varies greatly with temperature, and rising temperature will cause resistance to increase, affecting transmission efficiency; copper is much more stable in this regard.
Application scenarios
Copper coaxial cable: It is widely used in occasions with high signal quality requirements, such as radio and television, satellite communications, cable television networks (CATV), closed-circuit television monitoring systems (CCTV), computer networks, etc. Copper is the preferred material for applications that require high bandwidth and high-quality signal transmission.
Aluminum coaxial cable: Due to its lighter weight, aluminum coaxial cable is often used in broadcast antenna feeders (such as FM/TV broadcast towers), especially in those weight-sensitive applications. In addition, aluminum wire costs are generally lower than copper wire, so it is also used in some cost-sensitive but not particularly demanding applications.
Cost Factors
Cost: Aluminum is generally cheaper than copper, so aluminum coaxial cable may be cheaper. However, considering the long-term maintenance costs and performance differences, the choice of which material needs to be comprehensively evaluated.
Installation and Maintenance
Connection Difficulty: Copper wire is easier to handle and connect in terms of terminal processing and connection due to its good flexibility and processability. In contrast, aluminum wire may require special tools and techniques for proper connection to avoid poor contact problems caused by oxidation and other reasons.
Copper coaxial cable, aluminum coaxial cable, and zinc coaxial cable each have their own advantages and disadvantages, and the specific choice depends on factors such as application requirements, budget constraints, and environmental conditions. For most commercial and professional audio and video applications, copper coaxial cable is preferred due to its excellent electrical properties and stability; for specific large-scale wiring projects or applications that are extremely sensitive to weight, aluminum coaxial cable can be considered.
If you are not sure which coaxial cable to choose, you are welcome to send an email to communicate with TST CABLES cable engineers to obtain solutions and free samples.
Also available in:
English
Japanese
Russian
Portuguese (Brazil)