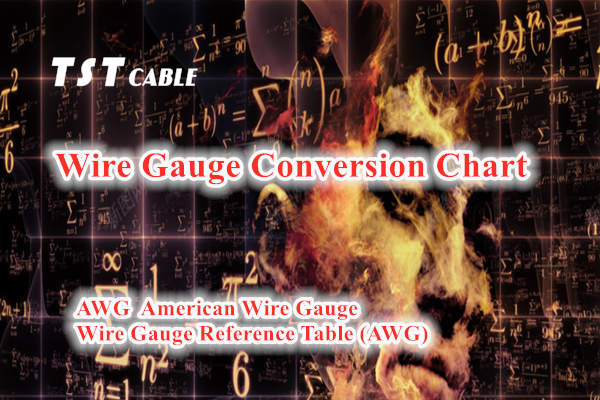
- Material usage of wires and cables
The usual calculation method for copper weight without conversion: cross-sectional area * 8.89 = kg/km
For example, 120 square millimeters: 120 * 8.89 = 1066.8 kg/km - Conductor usage: (Kg/Km) = d^2 * 0.7854 * G * N * K1 * K2 * C /
d = copper wire diameter G = copper specific gravity N = number of wires K1 = copper wire twisting rate K2 = core wire twisting rate C = number of insulated core wires - Insulation usage: (Kg/Km) = (D^2 – d^2) * 0.7854 * G * C * K2
D = insulation outer diameter d = conductor outer diameter G = insulation specific gravity K2 = core wire twisting rate C = number of insulated core wires - Outer sheath usage: (Kg/Km) = ( D1^2 – D^2 ) * 0.7854 * G
D1 = Finished outer diameter D = Upper process outer diameter G = Insulation specific gravity - Tape usage: (Kg/Km) = D^2 * 0.7854 * t * G * Z
D = Upper process outer diameter t = Tape thickness G = Tape specific gravity Z = Overlap rate (1/4Lap = 1.25) - Winding usage: (Kg/Km) = d^2 * 0.7854 * G * N * Z
d = Copper wire diameter N = Number of wires G = Specific gravity Z = Twisting rate - Braiding usage: (Kg/Km) = d^2 * 0.7854 * T * N * G / cosθ
θ = atan( 2 * 3.1416 * ( D + d * 2 )) * Mesh / 25.4 / T
d = Braided copper wire diameter T = Number of spindles N = Number of wires per spindle G=Specific gravity of copper
Specific gravity: copper-8.89; silver-10.50; aluminum-2.70; zinc-7.05; nickel-8.90; tin-7.30; steel-7.80; lead-11.40; aluminum foil Mylar-1.80; paper-1.35; Mylar-1.37
PVC-1.45; LDPE-0.92; HDPE-0.96; PEF (foaming)-0.65; FRPE-1.7; Teflon (FEP) 2.2; Nylon-0.97; PP-0.97; PU-1.21
Cotton tape-0.55; PP rope-0.55; cotton yarn-0.48
II. Calculation formula for materials other than conductors
- Sheath thickness: outer diameter before extrusion × 0.035 + 1 (in accordance with the nominal thickness of the sheath of power cables and single-core cables should not be less than 1. 4mm, the nominal thickness of multi-core cable should not be less than 1.8mm)
- Online measurement of sheath thickness: sheath thickness = (circumference after sheath extrusion – circumference before sheath extrusion)/2π
or sheath thickness = (circumference after sheath extrusion – circumference before sheath extrusion) × 0.1592 - Thinnest point of insulation thickness: nominal value × 90% – 0.1
- Thinnest point of single-core sheath: nominal value × 85% – 0.1
- The thinnest point of multi-core sheath: nominal value × 80% – 0.2
- Steel wire armor: number of roots =
{π×(outer diameter of inner sheath + wire diameter)}÷(wire diameter×λ)
Weight =π×wire diameter 2×ρ×L×number of roots×λ - Weight of insulation and sheath =π×(outer diameter before extrusion + thickness)×thickness×L×ρ
- Weight of steel strip ={π×(outer diameter before wrapping + 2×thickness-1) ×2×thickness×ρ×L}/(1+K)
- Weight of wrapping tape ={π×(outer diameter before wrapping + number of layers × thickness)×number of layers × thickness×ρ×L}/(1±K)
Where: K is the overlap rate or gap rate, if it is overlap, it is 1-K; if it is gap, it is 1+K
ρ is the material specific gravity; L is the cable length; λ is the twist coefficient
Also available in:
English