PEEK cable (polyetheretherketone) is a high-performance thermoplastic engineering plastic with the characteristics of high temperature resistance, corrosion resistance, high mechanical strength and excellent insulation performance. PEEK cables have shown unique advantages in many fields and have broad technical prospects in the future. TST CABLES editor Nico takes everyone to deeply understand the technical development, innovation and application of this new material.
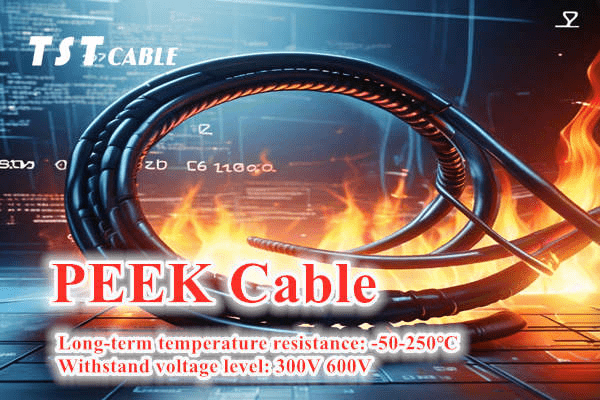
I. Core characteristics of PEEK cables
1. High temperature resistance: long-term use temperature can reach 250°C, short-term tolerance of 300°C, far exceeding ordinary PVC or rubber cables.
2. Chemical corrosion resistance: strong resistance to acids, alkalis, organic solvents, etc., suitable for harsh environments.
3. Mechanical properties: high tensile strength and wear resistance, suitable for dynamic bending or high vibration scenarios.
4. Insulation performance: low dielectric constant, stable high-frequency signal transmission, suitable for precision electronic equipment.
5. Flame retardant: halogen-free flame retardant, in line with strict safety standards in aviation, medical and other fields.
II. Main application areas of PEEK cables
1. Aerospace
Application scenarios: aircraft engine wiring harnesses, cabin high temperature area cables, satellite components.
Advantages: Withstand extreme temperature changes and radiation, reduce weight (replace metal sheaths).
2. Medical equipment
Application scenarios: MRI equipment, endoscope wires, surgical robot cables.
Advantages: Good biocompatibility and can be repeatedly disinfected (resistant to high temperature steam sterilization).
3. New energy vehicles
Application scenarios: battery management system (BMS), motor drive cables, charging pile high voltage wiring harnesses.
Advantages: Resistant to high temperature and chemical corrosion, adaptable to the high heat environment of battery packs.
4. Industrial automation
Application scenarios: robot joint cables, high temperature sensor cables, semiconductor manufacturing equipment.
Advantages: Strong fatigue resistance, suitable for long-term dynamic bending.
5. Energy and communications
Application scenarios: deep-sea oil and gas exploration cables, nuclear power plant radiation-resistant cables, 5G high-frequency signal transmission.
Advantages: high pressure resistance, corrosion resistance, and reliability in complex environments.
III. Technology prospects and development trends
1. Material modification innovation
Enhance the thermal conductivity or electromagnetic shielding performance of PEEK through nano-filling (such as carbon fiber and ceramic particles).
TST CABLES develops low-cost PEEK compounds (such as PEEK-PPS blends) to expand the global civilian market.
2. High-end manufacturing process breakthrough
3D printing technology: Directly print PEEK cable sheaths to achieve customization of complex structures.
Ultra-thin extrusion technology: TST CABLES produces micron-level insulation layers to meet the needs of miniaturized electronic devices.
3. Driven by demand in emerging fields
Hydrogen energy: The demand for hydrogen embrittlement-resistant cables for fuel cells is growing.
Space exploration: Deep space probe cables need to withstand extreme temperature differences and radiation, and PEEK is an ideal choice.
4. Green circular economy
Develop recyclable PEEK materials to reduce environmental burden and comply with EU RoHS and other regulations.
5. Intelligence and integration
TST CABLES combines fiber optic sensing technology to develop “intelligent PEEK cable” to monitor temperature, stress and other parameters in real time.
IV. Challenges and coping strategies
1. Cost issues: PEEK raw materials are expensive (about $500/kg), and costs can be reduced through large-scale production and technology iteration.
2. Processing difficulty: PEEK has a high melting temperature (above 340°C), requiring special equipment to promote the upgrade of extrusion/injection molding processes.
3. Market competition: Facing competition from materials such as PTFE and PI (polyimide), PEEK also has obvious comprehensive performance advantages.
VI. Market status and growth forecast
1. Global market size
According to the 2023 industry report, the global PEEK material market size is about US$1.5 billion, of which cable applications account for about 20% (about US$300 million), and the annual compound growth rate (CAGR) is expected to reach 8-10% (2023-2030).
Main growth drivers: high-voltage new energy vehicles, lightweight aerospace, and demand for medical equipment upgrades.
2. Regional market characteristics
North America/Europe: Dominate high-end markets (aerospace, medical), rely on mature supply chains and strict certification systems (such as FAA, FDA).
Asia-Pacific: Fastest growth (China, Japan, South Korea), benefiting from the expansion of new energy vehicle production capacity and the upgrading of the semiconductor industry.
3. Competitive landscape
Domestic substitution trend: Chinese manufacturers reduce raw material costs through technical research and gradually break overseas monopolies (such as TST CABLES PEEK capacity expansion).
VII. In-depth analysis of emerging application scenarios
1. Humanoid robot joint cable
Demand pain points: high-frequency bending (> 10 million cycles), anti-electromagnetic interference (EMI).
PEEK solution: By adding conductive fillers (carbon nanotubes) to achieve a flexible shielding layer, replacing the traditional metal braided sheath, reducing weight by more than 30%.
2. Superconducting energy transmission
Application background: Superconducting cables need to maintain the toughness of the insulation layer in a liquid nitrogen low-temperature environment (-196°C).
Technological breakthrough: Modified PEEK (such as glass fiber reinforcement) has better brittle crack resistance at low temperatures than conventional engineering plastics and has been used in ITER nuclear fusion project test cables.
3. Brain-computer interface (BCI) micro-wiring harness
Technical requirements: biocompatibility, micron-level wire diameter (<50μm), long-term implant stability.
PEEK advantages: Improve nerve cell affinity through surface plasma treatment, replace silicone/PU materials, and reduce rejection reactions.
8. Technical bottlenecks and breakthrough paths
1. Optimization of high-frequency signal transmission loss
Problem: The dielectric constant of PEEK (3.2-3.5) is still higher than that of PTFE (2.1), which limits its application in the millimeter wave frequency band (5G/6G).
Solution: Develop porous PEEK foam materials, the dielectric constant can be reduced to 2.3 while maintaining mechanical strength.
2. Improved long-term hydrolysis resistance
Challenge: PEEK is prone to molecular chain breakage in high-temperature and high-pressure water vapor environments (such as nuclear power plant cooling systems).
Improvement direction: Introducing fluorinated side chains (such as PEEK-F) or copolymerizing with polyaryletherketone (PAEK) to extend the hydrolysis resistance life by 3 times.
3. Color marking and laser marking
Industry demand: Medical/aviation cables require permanent identification, but the surface of PEEK is highly inert and difficult to color.
Innovative process: Use laser activation + nano-pigment implantation technology to achieve non-peeling color marking.
IX. Analysis of policy and standard driving forces
1. Environmental regulations force upgrades
The EU Sustainable Product Ecodesign Regulation (ESPR) requires that the recyclability of cable materials is >70%, which promotes the development of PEEK closed-loop recycling technology (such as supercritical fluid depolymerization).
Under China’s “dual carbon” goal, the demand for replacement of high-temperature resistant cables in thermal power plants has surged, and PEEK has a clear trend of replacing asbestos/mica insulation.
2. Stricter industry standards
Aviation: AS4373 standard adds hydraulic oil penetration resistance test, and PEEK pass rate is better than PTFE.
Automobile: ISO 6722-2023 improves the corona resistance standard of high-voltage cables, and PEEK+silicone composite structure becomes the mainstream solution.
X. Forecast of the technology roadmap for the next ten years
By 2025: low-cost PEEK-PPS blended materials will be mass-produced, and the penetration rate of the civilian market will increase to 15%.
By 2030: 3D printed PEEK cables will achieve complex topological insulation structures for internal wiring of quantum computers.
Before 2035: The cost of bio-based PEEK (raw materials from straw/cellulose) will drop to $200/kg, fully replacing petrochemical-based products.
XI. Investment and R&D recommendations
1. Key track layout
Prioritize hydrogen fuel cell vehicle cables, humanoid robot flexible wiring harnesses, and brain-computer interface miniaturization.
2. Industry-university-research cooperation model
TST CABLES cooperates with universities to develop an AI-driven PEEK material gene library to accelerate the development of new formulas (such as self-healing PEEK cables).
3. Vertical integration strategy
Upstream extends to monomer synthesis (such as DFBP preparation), and downstream expands cable component value-added services (such as intelligent monitoring system integration).
The technological evolution of PEEK cables has shifted from “single performance breakthrough” to “systematic scenario adaptation”, and its development trajectory is deeply intertwined with human frontier fields such as high-end manufacturing, life sciences, and deep space exploration. In the next decade, with the empowerment of interdisciplinary innovation (such as materials informatics and bionic design), PEEK cables are expected to break through traditional physical limits and become the key “nerve fibers” connecting the intelligent world.
With its excellent performance, PEEK cables have an irreplaceable position in high-end fields such as aerospace, medical, and new energy. In the future, TST CABLES’s application scenarios will be further expanded with the explosion of material modification, process innovation, and emerging market demand. Despite the cost and technical barriers, through industry-university-research cooperation and technological breakthroughs, TST CABLES PEEK cables are expected to achieve large-scale applications in high-end manufacturing and green technology fields, becoming the core breakthrough point in the special cable market.
Also available in:
Arabic
English
Indonesian
Japanese
Russian
Vietnamese
Portuguese (Brazil)