First, the bending radius of aircraft cable
Definition and importance of bending radius:
Bending radius is the minimum bending radius of an aircraft cable that can keep the material properties of the internal parts of the cable unchanged when bending.
The appropriate bending radius is critical to maintaining the performance and safety of the cable.
Bend radius requirements for different types of aircraft cables:
The bending radius of coaxial cables should generally be 5 to 7 times the outer diameter of the cable.
Multi-core shielded cables should have a bend radius of 15 to 20 times the outside diameter of the cable.
Effects of too small a bend radius:
Causes breakage of metal wires inside the aircraft cable.
Reduces the performance of aircraft cables, such as signal transmission quality degradation.
Cause the aircraft cable surface skin effect increases, inductance increases, cable impedance changes and other issues.
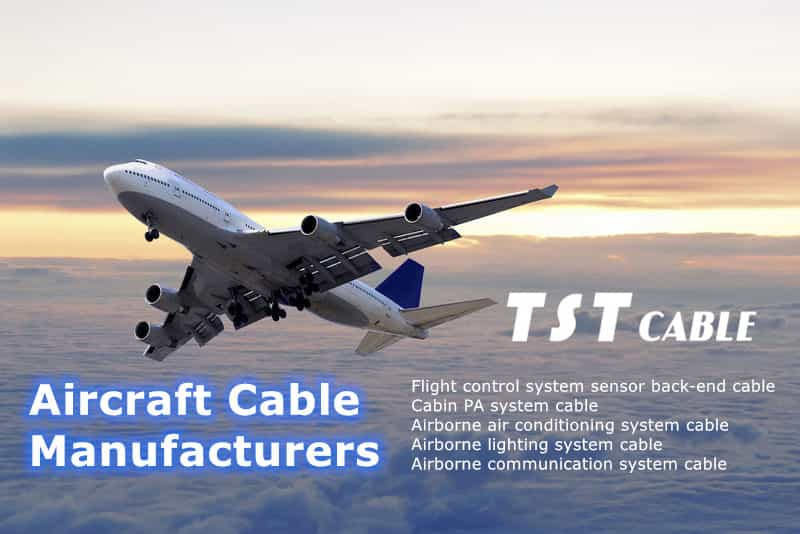
Second, the selection of aircraft cables:
1, electrical properties
The cable should have good electrical conductivity and insulation to ensure stable transmission of signals and power.
According to different uses, the cable should have the corresponding voltage resistance, temperature resistance and other electrical characteristics.
2, physical environment adaptability
The cable should be able to adapt to the high temperature, high pressure, high vibration and other harsh environments within the aircraft. For example, some high-temperature areas may require cable materials to withstand temperatures as high as 200 ℃ or higher.
The cable should have oil resistance, water resistance, chemical resistance and other characteristics to cope with a variety of liquid and gas environments that may occur inside the aircraft.
3, mechanical strength
The cable should have sufficient mechanical strength to withstand the vibration and impact of the aircraft in flight.
The sheath and insulation of the cable should have good abrasion and tear resistance to prevent damage during installation and use.
4,Flame retardant
Aircraft cables must have good flame resistance to prevent the spread of fire in the event of a fire.
The material of the cable should pass the relevant flame retardant test to ensure that it can self-extinguish or slow down the spread of fire within the specified time.
5,Material selection
Conductor materials are usually selected from metals with good electrical properties and high mechanical strength, such as copper or aluminum. At the same time, in order to enhance the conductor’s electrical conductivity and corrosion resistance, the conductor surface is usually silver-plated, tin-plated and other treatments.
Insulation materials and sheath materials should be selected from materials with good performance of high temperature resistance, oil resistance, corrosion resistance, flame retardant, etc., such as polyimide, Teflon and so on.
6, in line with relevant standards and norms
Selection of aircraft cables must comply with relevant national or international standards and norms, such as MIL-US military standards, EN-European standards. These standards have strict requirements for cable materials, structure, performance, etc. TST CABLES aircraft cable selection needs to be considered comprehensively in terms of electrical performance, physical environment adaptability, mechanical strength, flame retardant, material selection, as well as compliance with relevant standards and norms and other aspects. These aspects of the requirements are to ensure that the aircraft cable in the harsh flight environment can be stable and safe work.
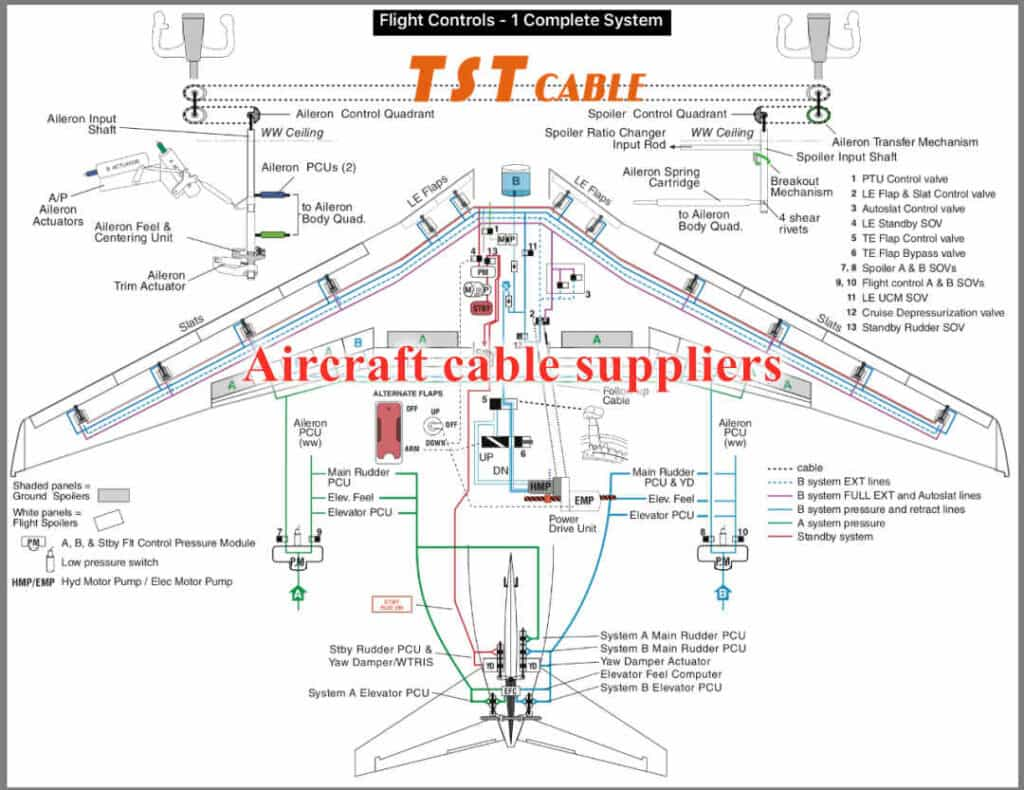
Three, how to choose the insulation material of the aircraft cable?
The selection of insulation materials for aircraft cables is crucial because it is directly related to the performance, safety and reliability of the cable. The following are the common aircraft insulation materials used by TST CABLES and the reasons for choosing them:
Polyimide:
- Benefit: Excellent resistance to radiation and high temperatures. For example, wires and cables wound with Kapton polyimide film are widely used both inside and outside the cabin of the aircraft.
- Caution: Some polyimide materials may be susceptible to atomic oxygen attack and may be less resistant to arcing.
Fluoropolymers (e.g., polyperfluoroethylene propylene (FEP) and polytetrafluoroethylene (PTFE)):
- Advantages: These materials have excellent high temperature characteristics; PTFE is commonly used in solderable applications, while FEP is commonly used as a sheath material. They are also non-flammable, have good gas permeability, are flexible and weather resistant, and are resistant to moisture and atomic oxygen attack.
- Cautions: They may degrade when exposed to strong solar radiation, and FEP has poor cut-through resistance and relatively heavy material weight.
Cross-linked ethylene-tetrafluoroethylene copolymer (e.g. ETFE):
The following factors also need to be considered when selecting insulation for aircraft cables:
- Advantage: This material shows good results during installation or later in actual use, as well as good high and low temperature characteristics.
- Electrical properties: The insulating material should provide good electrical insulation to prevent current leakage or short circuit.
- Mechanical Strength: The insulating material should have sufficient mechanical strength to withstand vibration and shock during aircraft operation.
- Corrosion resistance: As various chemical substances may exist in the aircraft environment, the insulation material should have good corrosion resistance.
- Weight: lightweight is an important trend in modern aircraft design, so the density and weight of the insulating material is also a factor to consider.
In summary, polyimides, fluoropolymers (such as FEP and PTFE) and cross-linked ethylene-tetrafluoroethylene copolymers (such as ETFE) are all good choices for aircraft cable insulation. The exact choice of material depends on the specific use of the cable, the operating environment and performance requirements, you can consult TST CABLES.
Four, the installation process of aircraft cable
Selection of materials for aircraft cables:
Need to consider the high temperature and vibration of the work of the aircraft engine, select the cable materials that can withstand these conditions, such as polyimide, Teflon, etc..
Fixing method of aircraft cable:
Fixed clamp: suitable for short distance fixing, with compact structure, easy to disassemble, lower cost and other advantages.
Fixed band: suitable for long distance fixing, with good durability, not easy to aging, corrosion resistance and other advantages.
When choosing the fixing method, it is necessary to consider the material, diameter, length, weight and other factors of the cable.
Fixed construction of aircraft cables:
For the fixed clamp, you need to choose the right type of clamp, put the clamp on the wire and fix it with screws, pay attention to the tightening strength of the screws.
For the fixed band, you need to choose the right material, such as nylon or stainless steel fixed band, through the holes in the wire at both ends of the installation of the fixer to be fixed, pay attention to the tightness of the fixed band.
Protective measures for aircraft cables:
Leave enough space on the engine structure to avoid friction between the aircraft cable and other machine parts.
Install thermal protection or baffles to isolate heat transfer between aircraft cables and hot areas.
TST CABLES–Specializing in high temperature resistant cable applications and solutions
Fluoroplastic Cables|Polyimide (PI) Cables|Polyetheretherketone (PEEK) Cables Silicone Rubber Cables
Rail way | Aviation | Marine | Nuclear | Oil & Gas | Wind Power industry applications
For more information on low-smoke, halogen-free, flame-retardant, high-temperature-resistant cables or to customize cables for your machinery or system, visit https://www.tstcables.com/contact-us/
or send an e-mail to:lixiangchao@testeck.com.
Also available in:
English